Battery Health Measurement Technology upgraded with AI
Measuring battery health and safety continuously is an important challenge as more electric vehicles, grid-scale energy storage devices and other clean energy technologies enter the market.
Industry needs better ways to diagnose the batteries that power these devices to ensure their safety, performance and reliability from inception to recycling. For example, lithium-ion batteries, despite their extensive use in multiple applications from consumer electronics, telecommunications and automotive, can experience several challenges over their lifetimes such as unintended capacity loss, short circuits and thermal runaway.
In 2011, Idaho National Laboratory researchers developed an award-winning technology for measuring battery health and safety.
By sending multiple waves of electrical current simultaneously through a battery, the Inline Rapid Impedance Spectroscopy (iRIS) technology determines the battery’s resistance and can monitor how the resistance changes over time. This data tells a lot about the battery’s state of charge, health and safety. Loveland, Colorado-based Dynexus Technology, Inc. exclusively licensed the iRIS technology from Idaho National Laboratory in 2015.
Now, iRIS is getting a boost of artificial intelligence thanks to a private industry collaboration between Dynexus and Pattern Computer, Inc., a company that uses pattern recognition to make complex datasets understandable and actionable.
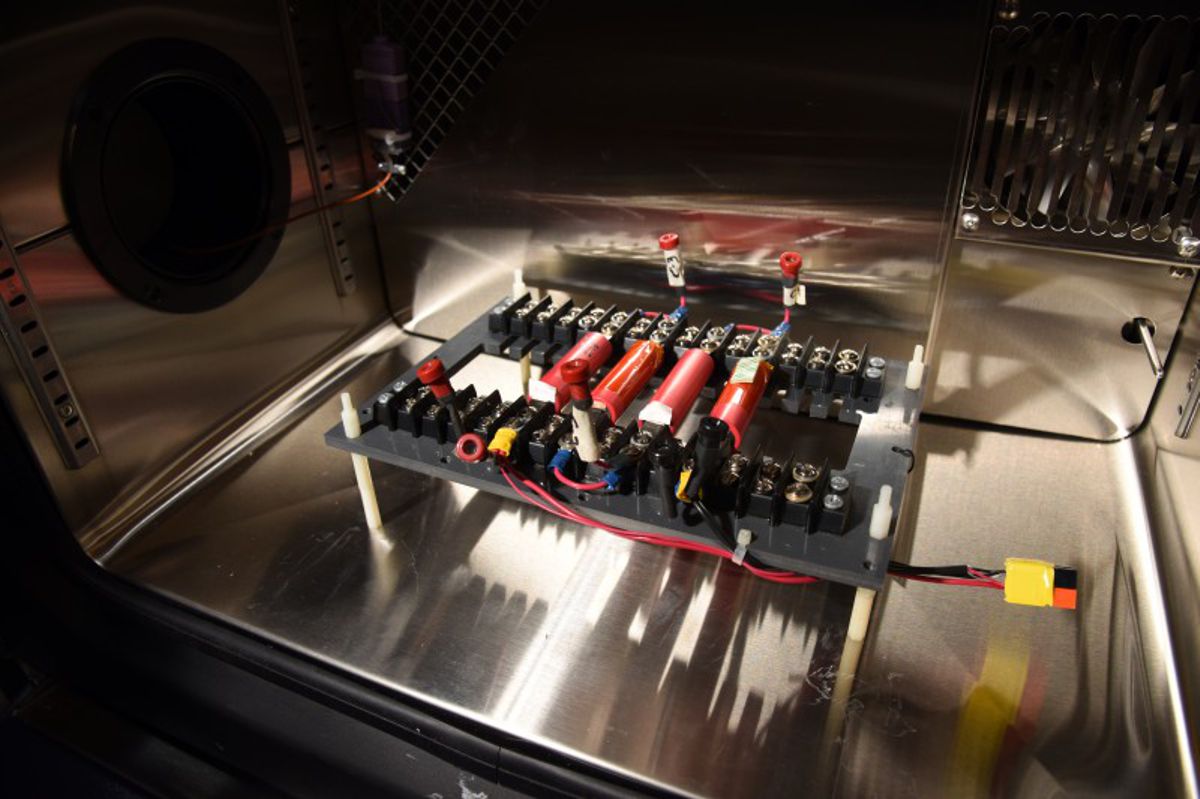
iRIS improves battery diagnostic
Even without artificial intelligence, iRIS improves upon other, similar battery diagnostic tools because it is much faster—it can generate a wealth of data within seconds, instead of minutes—and it can take measurements while the battery is charging or discharging.
The iRIS can measure up to 50 volts, though Dynexus researchers are working on a version that can measure up to at least 100 volts, which can be used for various battery module configurations.
That makes iRIS suitable for performing quality control functions in a battery factory or measuring the health of older batteries (in EV batteries that have reduced capacity, for instance) so they might be repurposed for a secondary use.
By combining iRIS with Pattern’s Pattern Discovery Engine, researchers hope to make the tool even more powerful.
“In order for the reuse and remanufacture of batteries to be sustainable, we need to be able to finance and insure second use battery assets,” said David Sorum, CEO of Dynexus Technology, Inc. “We need to understand the remaining capacity and state of health throughout a battery’s lifecycle. Working together, Dynexus and Pattern can significantly help solve that challenge.”
Battery integrators could use the hybrid iRIS/Pattern technology for difficult diagnostic challenges such as predicting battery failures or matching similar batteries together within the same device so they deliver optimal performance.
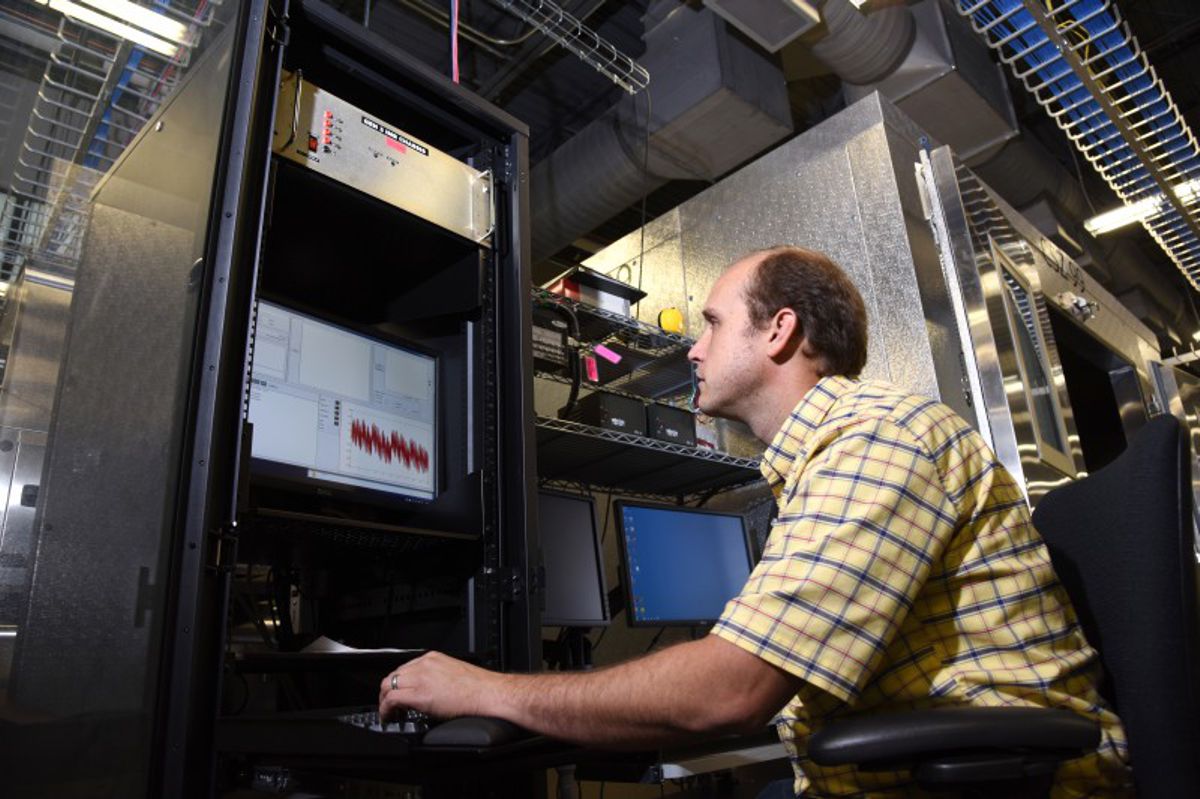
INL tech makes big impact
Tanvir Tanim, a senior battery research and development scientist at INL, uses iRIS during his research, and benchmarks the technology against other diagnostic tools.
“It is one of the diagnostics that may be useful to understand battery performance, life and safety early on,” he said. “If you just look at conventional measurements—voltage, temperature and current—it is often difficult to accurately measure a battery’s state of health and state of safety.”
The Dynexus-Pattern collaboration is one example of how a technology developed and tested at INL, and commercialized by private companies, could potentially have a big impact on industry, said INL commercialization manager Ryan Bills.
“With iRIS, Dynexus has attracted interest from customers in industry and government,” he said. “Now, the Pattern partnership forms the basis for something new. Together, they are going to improve how battery health is measured, moving the needle from battery diagnostics to battery prognostics to help maximize battery value and improve safety.”