The Concrete Maturity Method and why you should validate your maturity curve
The maturity method is an ASTM-standardized, non-destructive test method for estimating concrete strength that provides real-time results. Typically, cylinders and beams are required to be cast and broken for quality control and 28-day acceptance.
It is common practice to simply cast and break additional samples, sometimes referred to as companion samples, for estimating early-age strength of in-place concrete for purposes such as early form removal, post-tensioning of elevated slabs, and fast-track pavement construction and repair. However, the strength gain of these cylinders may not reflect the strength gain of the in-place concrete.
For example, when placing concrete in ideal or hot-weather conditions, strength gain will likely occur faster for in-place concrete than for companion cylinders or beams simply because of the difference in size and heat generation during hydration.
For the same reason in cold weather, it may be that in-place concrete gains strength slower than companion cylinders particularly if companion cylinders are cured at warmer temperatures. Maturity bridges the gap between what is tested for in companion samples and what field conditions are assumed.
Maturity uses sensor technology to provide real-time updates of in-place temperature and age, allowing users to estimate strength based on a maturity curve developed by breaking cylinders or beams.

What is the maturity curve and how is it developed?
The relationship between concrete maturity and strength can be graphically represented using a maturity curve. To develop a maturity curve with cylinders according to ASTM C 1074, concrete cylinders are cast from a trial mix.
A sensor is embedded at the centres of two cylinders. The cylinders are all cured in the same environment, then at 24 hours, 72 hours, 7 days, 14 days, and 28 days (unless alternate intervals are otherwise specified by an engineer), a minimum of two cylinders are broken.
The compressive strengths are averaged and recorded. At the same times the cylinders are broken, maturity is calculated using the sensors’ temperature history data. The resulting data is then plotted on a graph with maturity on the x-axis and strength on the y-axis, and a curve is fit to the data.
This resulting correlation curve can be used in future field applications—users can simply compare the measured maturity value of the concrete to the curve and estimate the strength.

How do you validate the maturity curve?
Each concrete mix design has its own unique maturity curve. Changes to the mix, such as a change in aggregate type or content, water to cement ratio, cement type, or supplementary cementitious material (SCM) source, can influence the relationship between maturity and strength.
To successfully implement the maturity method in the field, the concrete delivered must be consistent with the concrete used during testing to create the maturity curve.
Because maturity curves are unique, it is important to ensure that the proper curve is being used to estimate strength. ASTM C 1074 includes a few options for this validation process including cast-in-place cylinders, penetration resistance test, and pull-out test, but the most commonly used option is early-age tests of field-moulded cylinders instrumented with maturity sensors.
To validate the maturity curve, follow these steps:
- When pouring concrete at the construction site, cast three cylinders using the same concrete as being placed. Place a temperature sensor in one of the cylinders and be sure all three cure together in the same environment.
- When you are ready to validate, break the two cylinders without sensors and find their average compressive strength.
- Then, read the maturity index from the embedded sensor and use the maturity curve to find the estimated strength.
If the measured compressive strength and the estimated strength agree within 10%, then the maturity curve is validated. If the strengths differ by more than 10%, then this indicates enough change in the mix that a new curve should be generated to better represent the mix.
Validation of the maturity curve should be performed periodically, and at specific intervals (weekly, monthly, seasonally, etc.), depending on different job specifications. Though validation is not required before every use of the maturity curve, it should be performed regularly as it is crucial to performing this test method properly.

Why is it important to validate the maturity curve?
Validation is part of the ASTM-standardized maturity test method and is recommended periodically as a best practice to achieve the highest accuracy possible. Since each curve is particular to the concrete mix it was designed for, if any mix condition or constituent has changed significantly, the correlation between the maturity and strength changes as well, and the estimations for strength based on the maturity curve may not reflect the true strength of the concrete.
This can result in liability issues or structural issues—if the concrete is mistakenly assumed to have reached sufficient strength when it has not, it may fail under the load it was designed for.
Validation can also work as quality control. If the measured strength and estimated strength differ by more than 10%, it may be a result of inconsistency between the concrete delivered to the jobsite and the concrete tested in the laboratory. In this case, corrective action can be taken before extensive rework would be necessary.
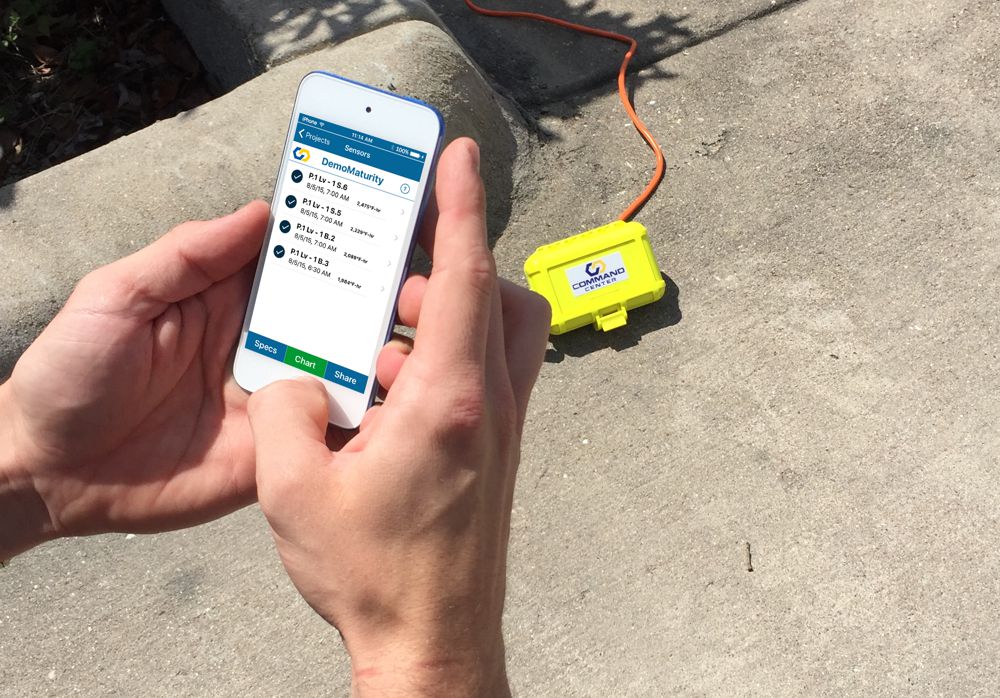
Systems like COMMAND Center greatly ease the process of validation by automatically creating maturity curves based on a user’s break data. Affordable smart sensors are embedded in the concrete and continuously collect temperature and maturity data.
Users can retrieve the data wirelessly to their iOS device or using a handheld device connected directly to the sensors. Then the data can be viewed and analyzed on COMMAND Center’s free, powerful software. There, the user can see a complete temperature and maturity history of the concrete and create maturity curves.
Estimating in-place concrete strength using the maturity method is the easiest and most efficient way of finding real-time strength. To ensure that this method is being executed properly and accurate results are being obtained, it is recommended that the maturity curve be validated before use.