DB Group achieve 77 percent CO2 reduction using Cemfree concrete on M25 pilot project
Working on behalf of Connect Plus, a team from Jackson, DB Group and Axtell have achieved a 77% reduction in CO² by using volumetric mix trucks to pour ultra-low carbon Cemfree concrete on the Woodford West Viaduct.
This is the first time Cemfree has been used volumetrically, and the potential for reducing carbon emissions on future highways projects is extensive.
Cemfree was successfully piloted at the Woodford West Viaduct to pour a concrete hardstanding underneath the structure. This initial application amounted to 52 m³ of concrete, leading to a saving of 9.4 tonnes of CO², when compared to using a conventional mix, greatly reducing the environmental impact.
Jackson has been working with low carbon concrete for the past few years, however, it has always been challenging to use on the M25, due to the availability of batching plants, which usually shut at night.
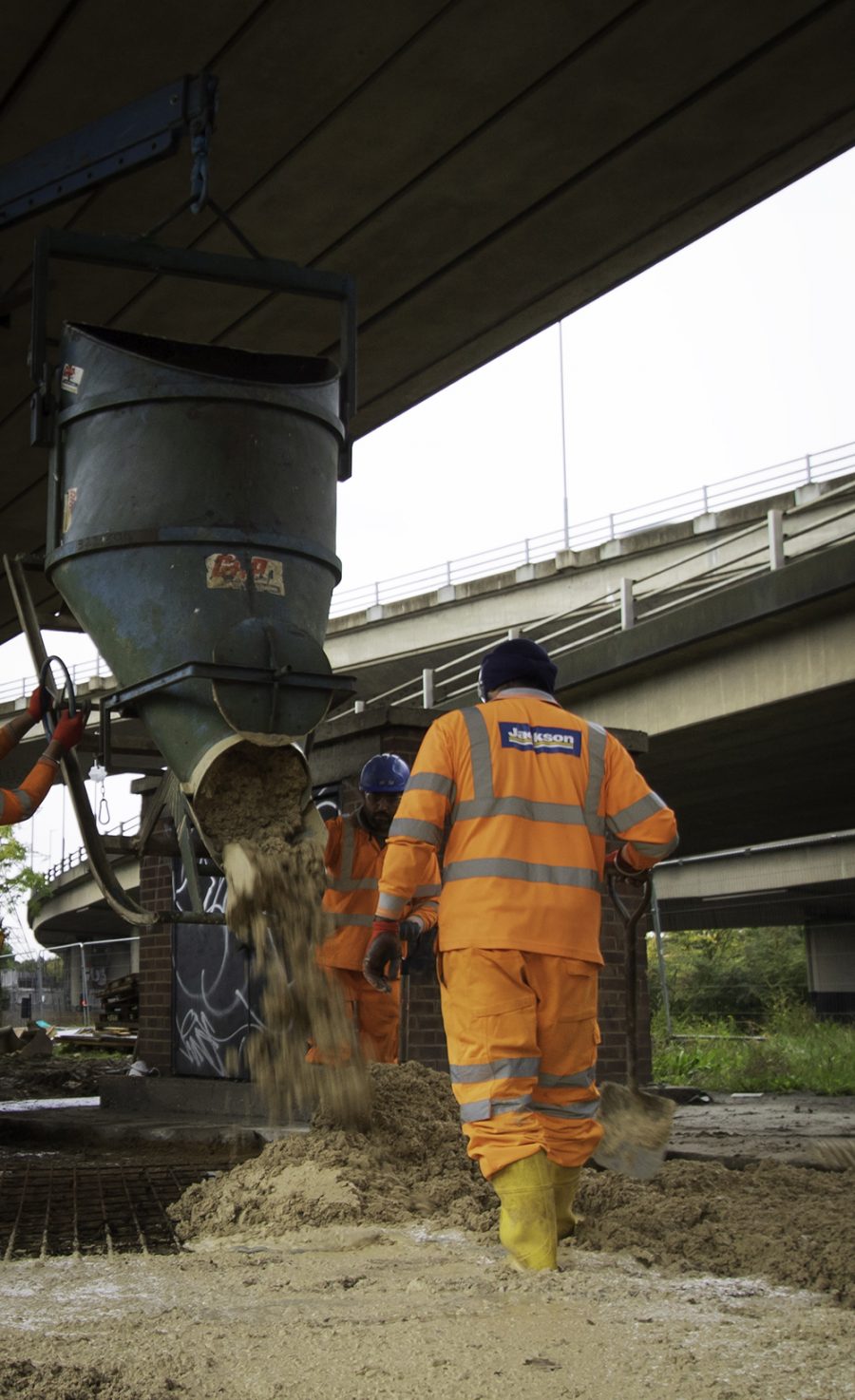
Instead, this trial has proven the suitability of volumetric mix trucks, which are able to produce just the right amount, and crucially, at the right time, day or night, without having to rely on a batching plant to dedicate an entire silo to the product.
Tony Sheridan, DB Group’s Commercial Manager, said: “As well as enabling significant carbon savings versus a more traditional concrete mix, Cemfree offers enhanced durability and considerable savings in water consumption. Cemfree also allows contractors to consider larger pours with fewer joints as the relatively low heat generated during the curing process leads to less cracking in the finished concrete. Interest in Cemfree has grown considerably over the past few years as environmental issues and climate change have come more into public focus.”
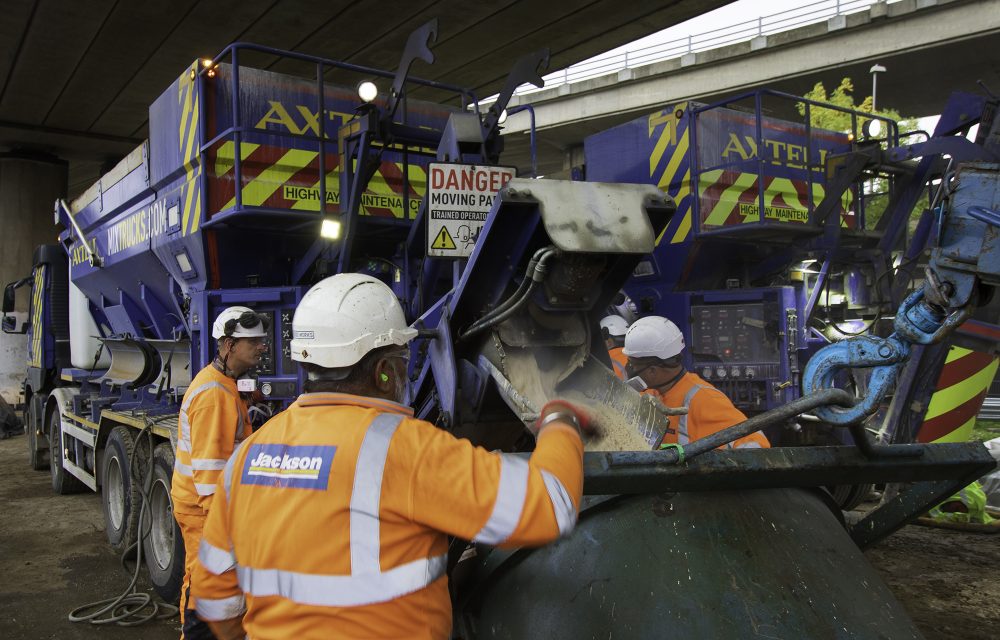
Jackson’s Highways Division Director, Paul Watson said: “We’re really pleased to have introduced ultra-low carbon concrete to the M25, and credit must go to our client Connect Plus, whom, as an intelligent client, supports us to trial new materials.
“Our work with Axtell has proven that we’re able to supply the low-carbon material at no extra cost, and without having to place a large order with a ready-mix supplier, which makes the material far more accessible to use on the M25. We hope this marks a turning point on the M25, and the wider Highways sector for using low carbon alternatives.”
Conventional concrete uses Ordinary Portland Cement (OPC) as a component which causes almost a tonne of CO² per tonne of material produced. The manufacturing process of OPC contributes 8-10% of global greenhouse gas emissions, twice as much as aviation, and is a major contributor to construction industry emissions.
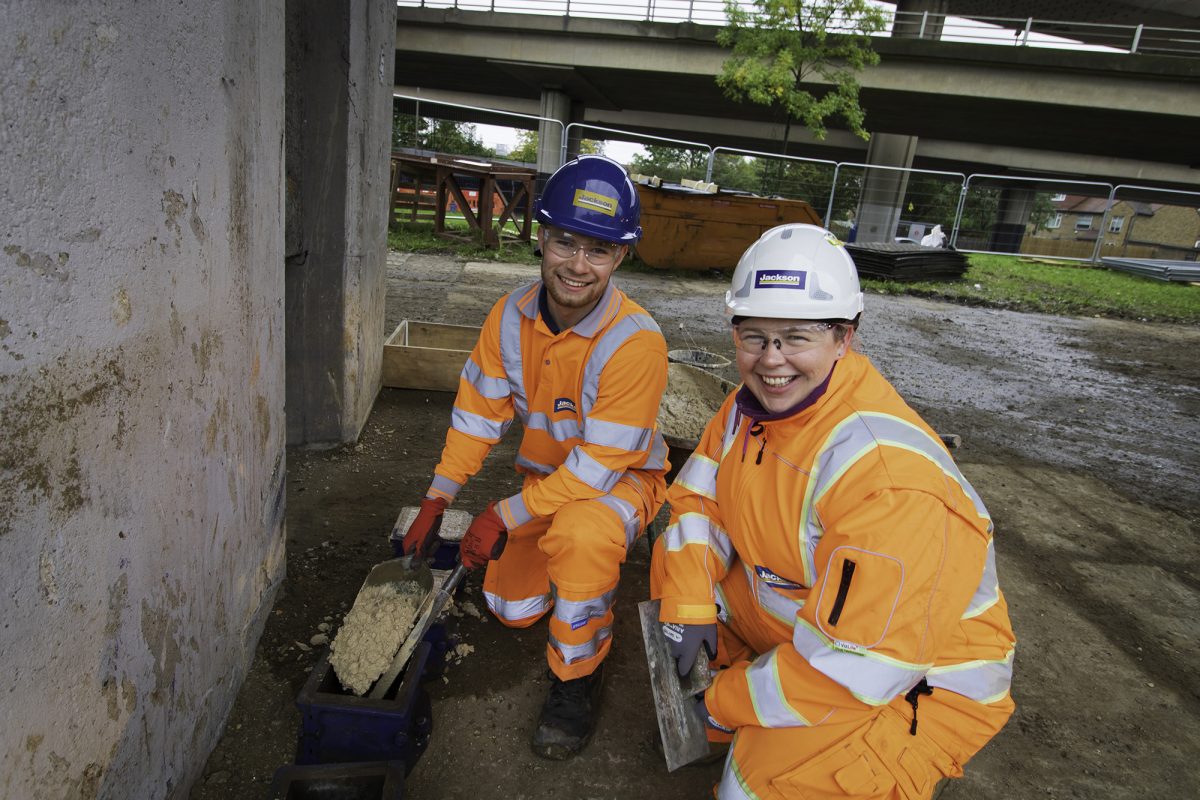
Cemfree removes the need for OPC completely using 95% ground-granulated blast-furnace slag and a 5% alkali activator instead. The CO² value of Cemfree is 114 kg per tonne, 77% lower than conventional mixes.
Andy Dean, CEO of Connect Plus, said: “Connect Plus is committed to reducing carbon emissions across the M25 network and we’re thrilled to be supporting this progressive innovation.”
Andrew Axtell, proprietor of Axtell said: “We’re keen to offer this low-carbon cement alternative as part of our various offerings as we know that this is definitely the future.“