Desktop Metal launches Process Simulation Software for Metal Additive Manufacturing
Desktop Metal, a leader in mass production and turnkey additive manufacturing solutions, is launching Live Sinter™, a software solution designed to eliminate the trial and error required to achieve high-accuracy parts via powder metallurgy-based additive manufacturing processes like binder jetting.
The software launch follows Desktop Metal’s recent signing of a definitive business combination agreement with Trine Acquisition Corp. to accelerate its go-to-market efforts and further drive its relentless efforts in advanced R&D.
A breakthrough software application, Live Sinter not only corrects for the shrinkage and distortion parts typically experience during sintering, but also opens the door to printing geometries that, without the software, would present significant challenges to sinter. By improving the shape and dimensional tolerances of sintered parts, first-time part success for complex geometries is improved and the cost and time associated with post-processing are minimized. In many cases, the software even enables parts to be sintered without the use of supports.
While compatible with any sintering-based powder metallurgy process, including metal injection moulding (MIM), Live Sinter will first be available to customers of Desktop Metal’s Shop System™, shipping in late 2020, and Production System™, shipping in 2021.
“The manufacturing industry is witnessing the transformative power that additive manufacturing has across many industries, from automotive and aerospace, to heavy machinery and consumer products with respect to quality, performance, and cost savings. We believe Live Sinter will be a critical companion in continuing to drive forward the success of additive manufacturing,” said Ric Fulop, CEO and co-founder of Desktop Metal. “As manufacturers look to capitalize on the flexibility of volume production delivered through technologies such as binder jetting, Live Sinter is a first-of-its-kind solution that offers a path to predictable and repeatable outcomes by demystifying the sintering process.”
Challenges of Sintering & Powder Metallurgy-based Additive Manufacturing
Sintering is a critical step in powder metallurgy-based manufacturing processes, including binder jetting. It involves heating parts to near melting in order to impart strength and integrity, and typically causes parts to shrink by as much as 20 percent from their original printed or moulded dimensions. During the process, improperly supported parts also face significant risk of deformation, resulting in parts that emerge from the furnace cracked, distorted, or requiring costly post-processing to achieve dimensional accuracy.
Sintering distortion has been a reality for the powder metallurgy industry for decades. For much of that time, the solution has been to rely on the experience of industry veterans who, based on repeated trial and error, combine adjustments to part designs with various sintering supports, or “setters”, to enable stable, high-volume production. Live Sinter changes the game by minimizing the reliance on trial and error and offering a streamlined, easy-to-use software solution that delivers accurate parts without requiring users to be experts in powder metallurgy.
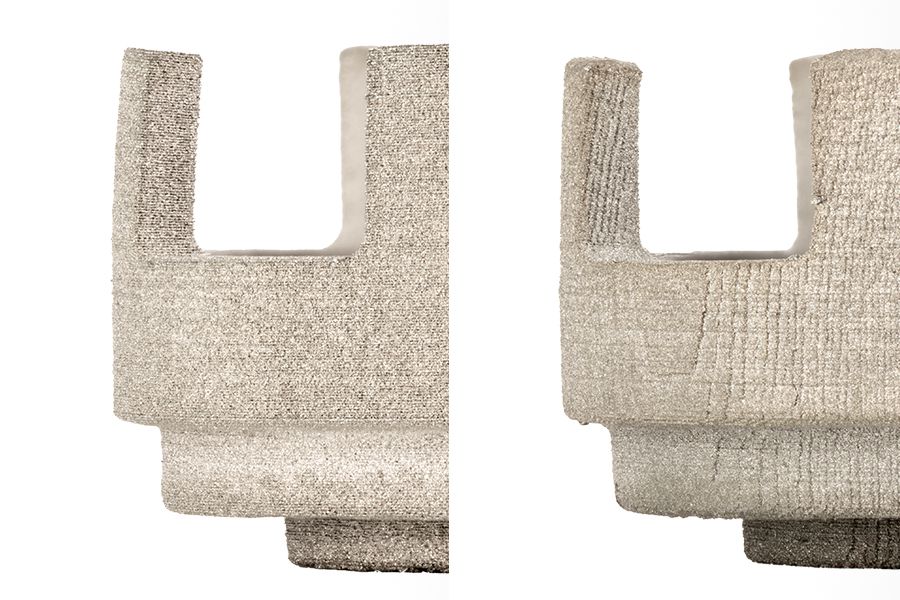
Software-generated “Negative Offset” Geometry Compensates for Distortion
Developed in collaboration with Desktop Metal materials scientists, Live Sinter can be calibrated to a variety of alloys. It predicts the shrinkage and distortion that parts undergo during sintering, and automatically compensates for such changes, creating “negative offset” geometries that, once printed, will sinter to the original, intended design specifications. These negative offsets are the result of a GPU-accelerated iterative process, in which the software proactively pre-deforms part geometries by precise amounts in specific directions, allowing them to achieve their intended shape as they sinter.
Sintering simulation is a complex multi-physics problem that involves modelling how parts and materials respond to a number of factors, including gravity, shrinkage, density variations, elastic bending, plastic deformation, friction drag, and more. Moreover, the thermodynamic and mechanical transformations that occur during sintering take place under intense heat, making them difficult to observe without either halting the sintering process mid-cycle or installing windows in the furnace to observe distortions from images taken at high temperature. While such methods are potentially tolerable in R&D environments, they create significant delays and costs in time to market for production applications.
“Live Sinter was developed by joining forces with – instead of fighting against – sintering-based challenges. In doing so, the software generates negative offset part geometries that sinter to the intended shapes and dimensional specifications,” said Andy Roberts, Desktop Metal VP of Software. “It also tackles some of sintering’s biggest challenges, such as the use of setters. For years, creating setters that prop up parts in the furnace relied on the intuition of few engineers with years of hands-on experience. Now, the process is easier, more predictable, and more controllable using Live Sinter.”
High-speed Simulation Powered by GPUs and Streamlined Calibration
Live Sinter runs on a GPU-accelerated multi-physics engine, capable of modelling collisions and interactions between hundreds of thousands of connected particle masses and rigid bodies. The multi-physics engine’s dynamic simulation is refined using an integrated meshless finite element analysis (FEA), which computes stress, strain, and displacement across part geometries used to predict not only shrinkage and deformation, but also risks and failures, validating the feasibility of a part for sintering-based additive manufacturing before the build begins.
Armed with this dual-engine approach, which strikes a balance between speed and accuracy, Live Sinter can simulate a typical sintering furnace cycle in as little as five minutes and generate negative offset geometries that compensate for shrinkage and distortion in as little as fifteen minutes, compared to more general-purpose simulation tools that use complex meshes and require complex setups and hours to complete. Moreover, the software can be calibrated to new materials and sintering hardware and process parameters with minimal additional effort.
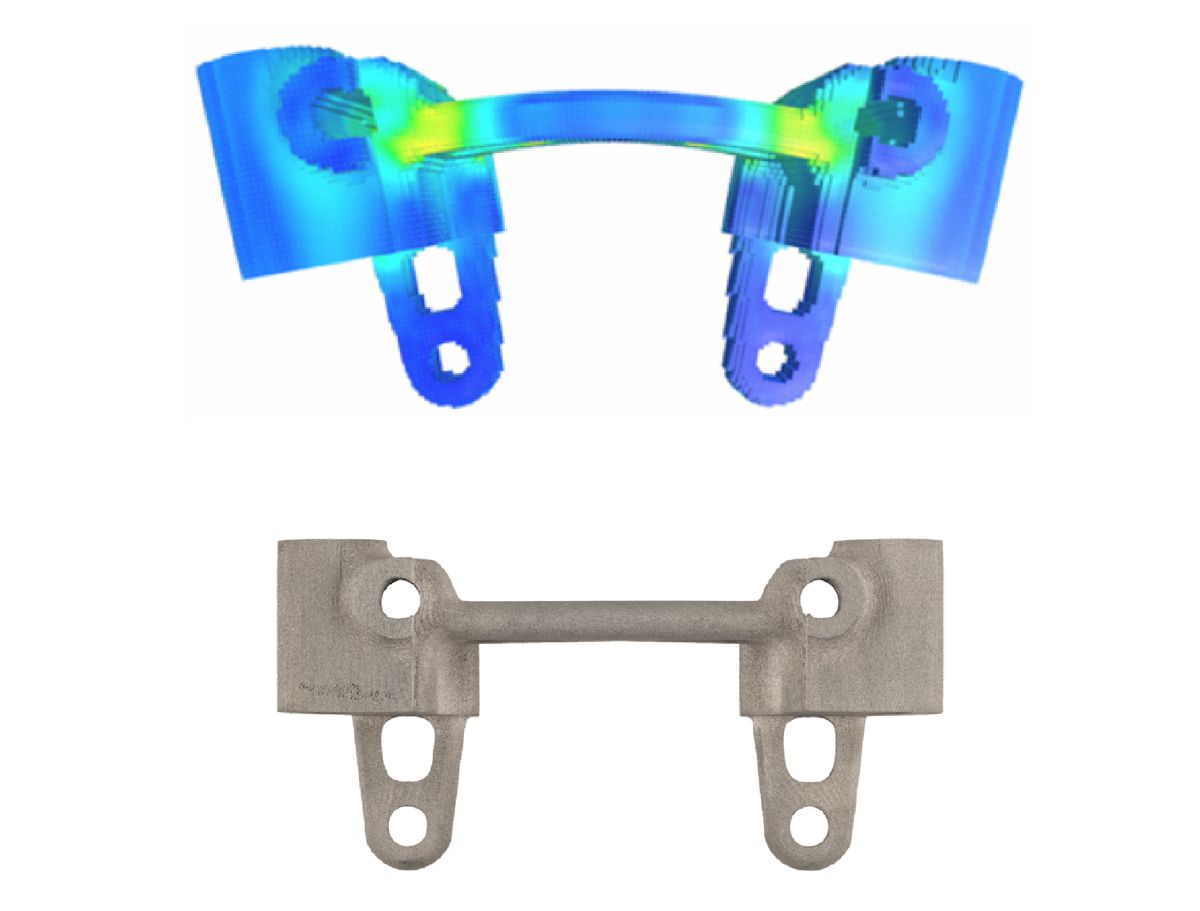
Bundled with Desktop Metal Binder Jetting Technology
Live Sinter will first be available in Q4 2020 to customers of Desktop Metal’s Shop System and Production System additive manufacturing solutions. In time, the Company may offer the process simulation software to users of any sintering-based powder metallurgy process.
The Shop System is designed to bring metal additive manufacturing to machine and job shops with an affordable, turnkey solution that achieves exceptional surface finish parts with rich feature detail at speeds up to 10 times those of legacy powder bed fusion additive manufacturing technologies. Created by leading inventors of binder jetting and single-pass inkjet technology, the Production System is designed to be the fastest way to 3D print metal parts at scale.
The system is an industrial manufacturing solution designed to achieve speeds up to 100 times those of legacy powder bed fusion additive manufacturing technologies, enabling production quantities of up to millions of parts per year at costs competitive with conventional mass production techniques.
Desktop Metal, which is celebrating its fifth year anniversary in the fall 2020, recently signed a definitive business combination agreement with Trine Acquisition Corp. a special purpose acquisition company led by Leo Hindery, Jr., and HPS Investment Partners, a global credit investment firm with over $60 billion in assets under management.