When it comes to building bridges Doka are the experts
People tend to cross bridges as quickly as possible; because you never know. Experts even have a term for this phenomenon: gephyrophobia or “bridge anxiety”. Yet these valley-spanning structures are true expressions of supreme engineering skill, as illustrated by the new Aftetal bridge in North Rhine-Westphalia.
It’s a common enough experience for all motorists: you reduce your speed, see a warning sign for slippery roads or side winds, plus the obligatory windsock – followed by the brief rattle of the transitions, which cause a slight bump in the road. That’s usually all you notice of a bridge. Travellers are rarely able to appreciate their true beauty. Who knows the name of a bridge, let alone the names of the companies involved in its construction?
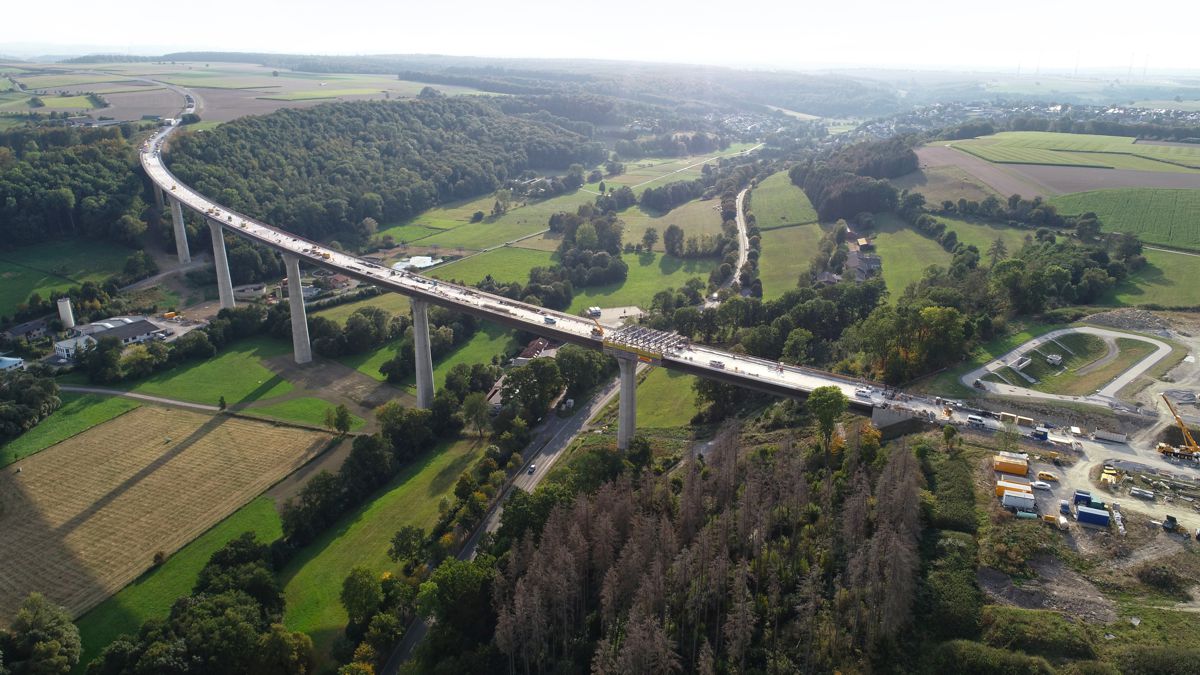
Probably only a handful of people are familiar with the team around Matthias Urban and Markus Mühlnickel from formwork expert Doka – although they are actually always on hand wherever a complex bridge project involving concrete is underway in Germany. This is true, regardless of whether the bridge in question uses cantilevering, incremental launching or launching-girder equipment/load-bearing systems. An impressive example is the steel-concrete colossus named the Aftetal bridge – almost 800 meters long, with around 66 metres high piers, some of them at distances of up to 120 meters. It is a valley bridge, which aims to ease the traffic situation in the Westphalian town of Bad Wünnenberg and facilitate travel between Brilon and Paderborn in the long run.
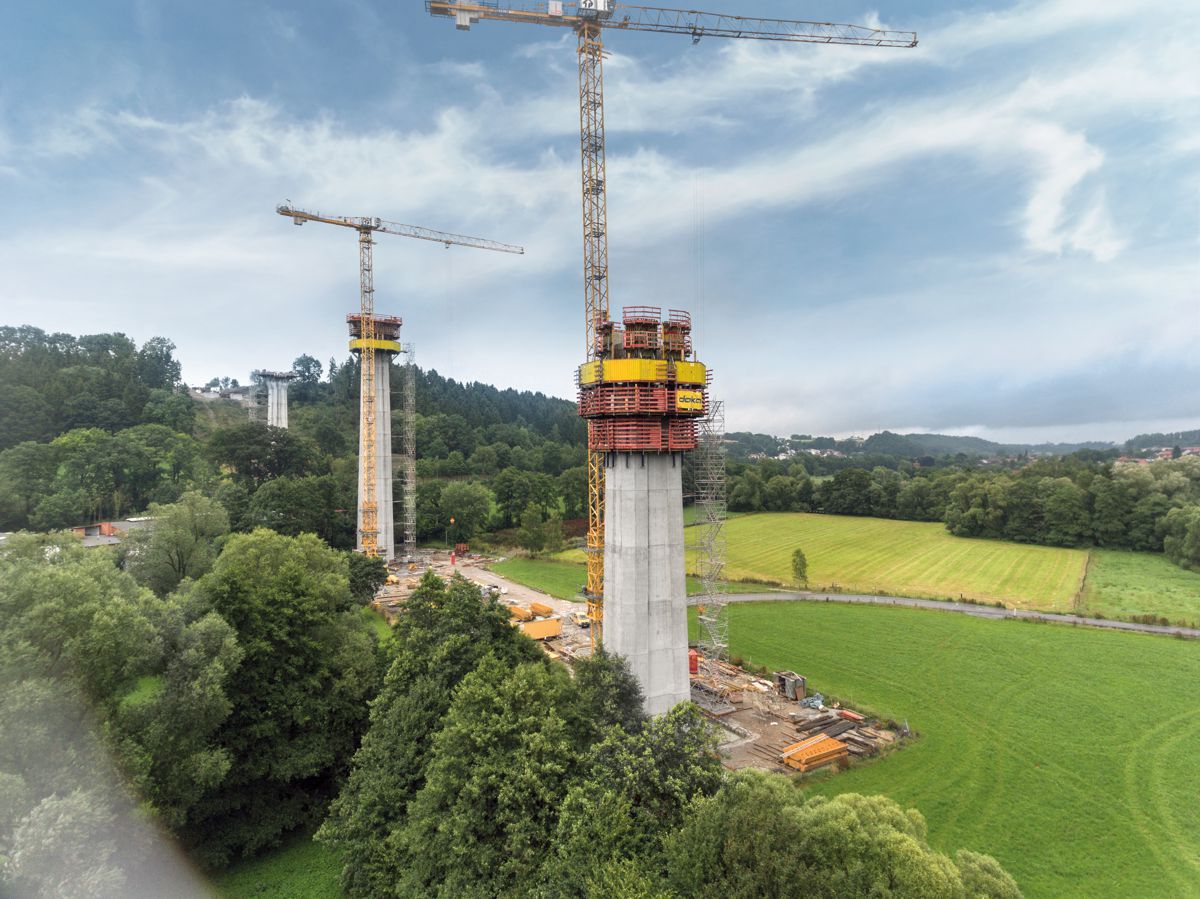
Matthias Urban, the project manager, emphasises: “It is an imposing, very long and wide bridge, and the piers are very massive. You don’t get that very often.” And that says a lot: After all, Doka has been supplying equipment and engineering expertise for cross-valley and cross-river traffic routes such as the Lahntal, the Nuttlar, Pfädchensgraben or Tiefenbach bridge for some time now. Even after 15 and 27 years respectively on the job, the engineers stress, “our department is passionate about bridges”. Markus Mühlnickel, the group leader, quotes Antoine de Saint-Exupéry, who wrote about the importance of teaching people to long for the infinite, vast sea, if you want them to build a ship. This is probably also true if you want to build a bridge: it is best to keep the image of free-flowing traffic in mind right from the start. This is how you encourage motivation and enthusiasm. A bridge, says the engineer, is always a prominent feature and decisively shapes the landscape. It feels wonderful to watch it grow and ultimately create connections between places and people.
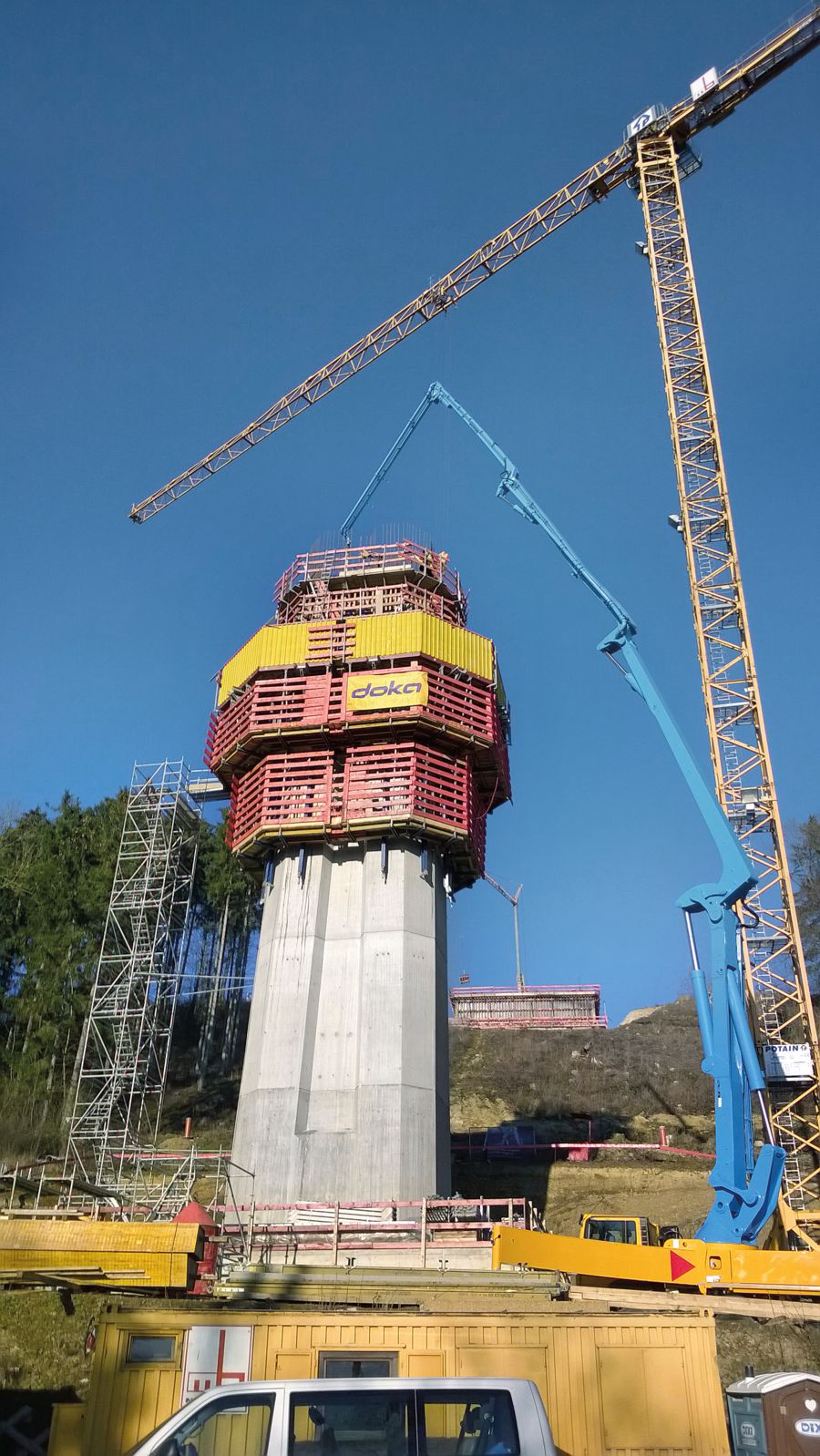
“Bridges are classic civil engineering,” says Urban, because they usually consist of abutments and piers, pier heads and a superstructure. Nevertheless, they only look alike at first glance. When you take a closer look, they actually entail quite different engineering technologies. And with the complexity of the bridge geometry, formwork requirements grow. From this perspective, the Aftetal bridge is one of the more challenging constructions – with its height, the complex geometry of its piers, the massive pier heads and not least because of its length and span. In principle, engineers tend to rely on standard systems for such a project as well. However, some aspects will always need individual solutions. Urban mentions the special engineering skills required for bridges and the special solutions and interface planning, which are indispensable at this level. A good formwork supplier does more than just supply components and systems. They also know how to make the most of its potential for the project at hand. It’s all about process, deadline and cost certainty.
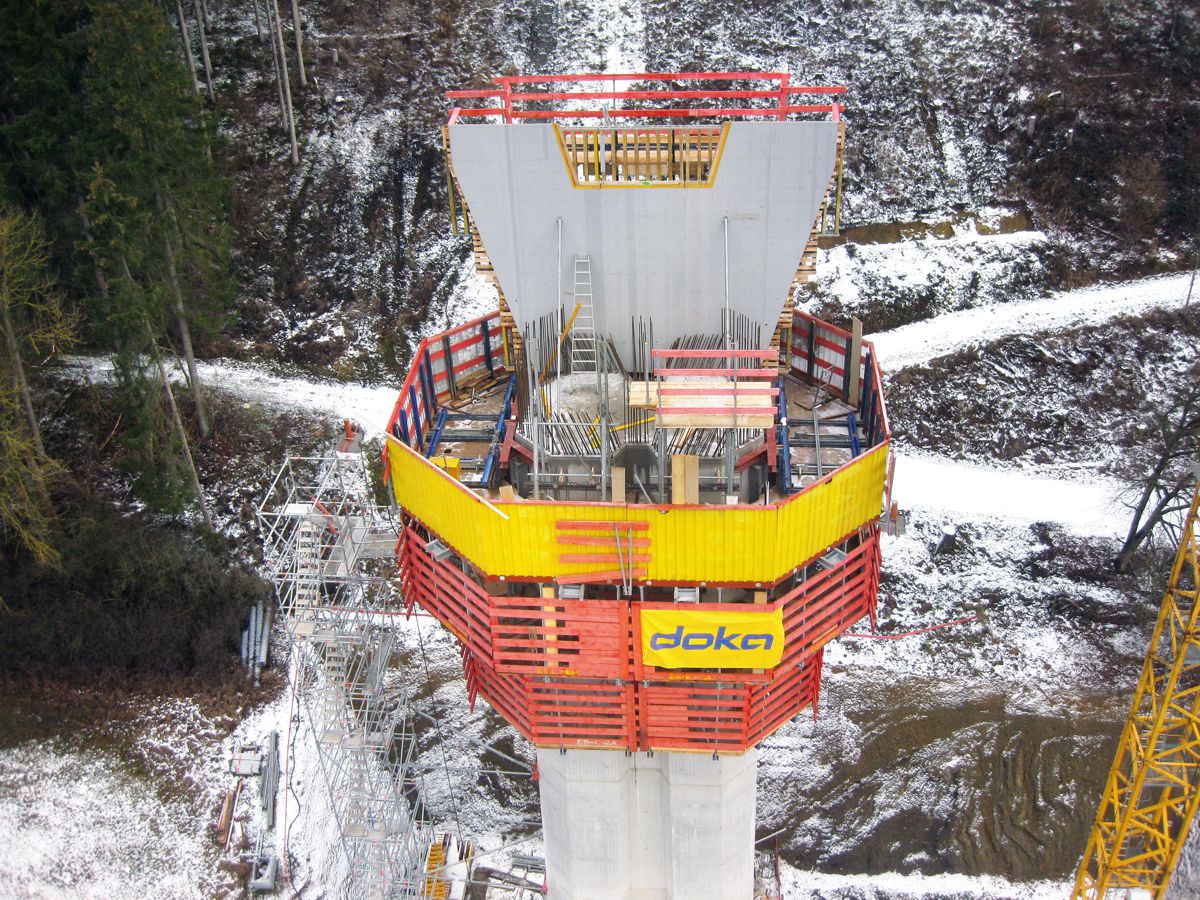
“Clients often give us their plans and expect that we already have a ready-made solution up our sleeves,” adds Mühlnickel. But for a bridge like this, there are no ready-made solutions. You have to sit down with the project partners, involve the team, plan, calculate, check, revise, meet again and continue to coordinate. “It’s about arriving at the best solution, which is ideally also the safest,” says Mühlnickel. “At the end of the day, the workers want to return home safely to their families.” After all, it’s not only about averting the risk of falling, it is also important to ensure that the equipment is ergonomic and minimises physical strain.
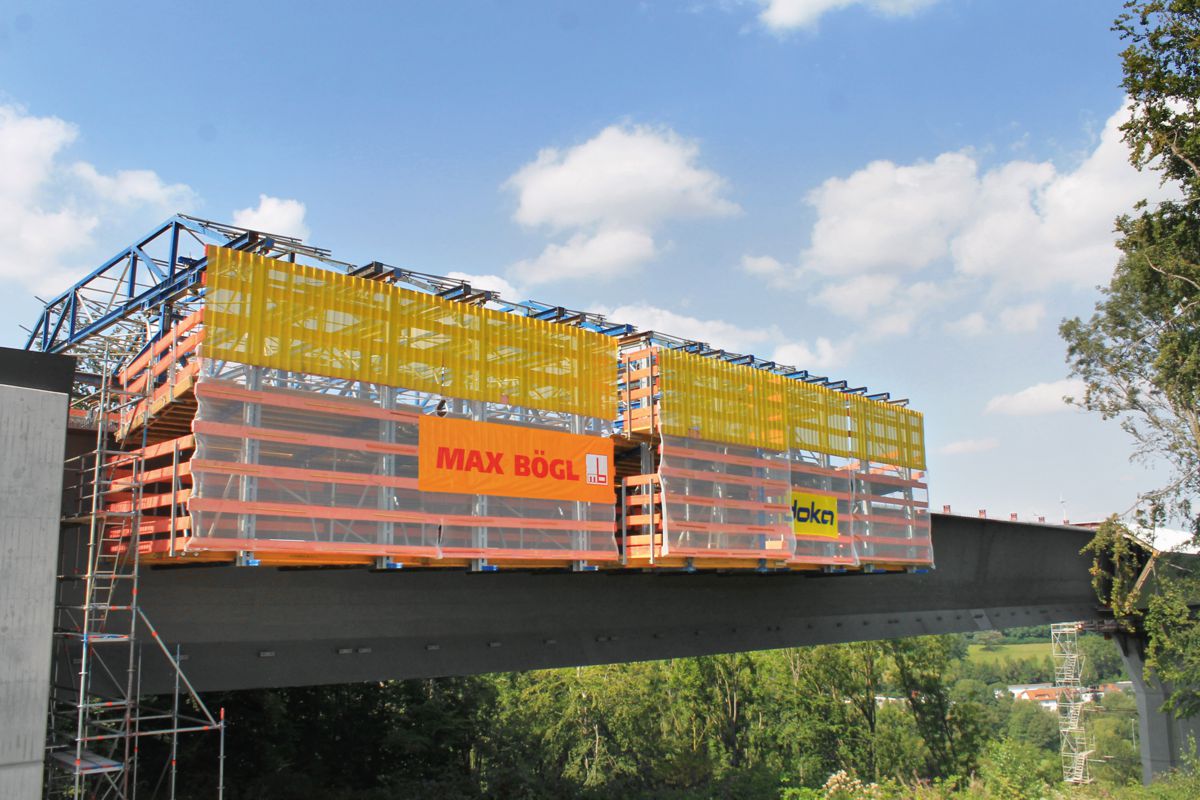
It is up to Doka to provide its partners with good advice, and to show the advantages and disadvantages of various methods, to make the right decisions with regard to provision and operating time. On top of that, we must design solutions that are safe for life and limb – a “return on prevention”, as it is called in technical jargon. Studies have shown that every euro invested in safe and ergonomic working conditions pays off twice or three time over.
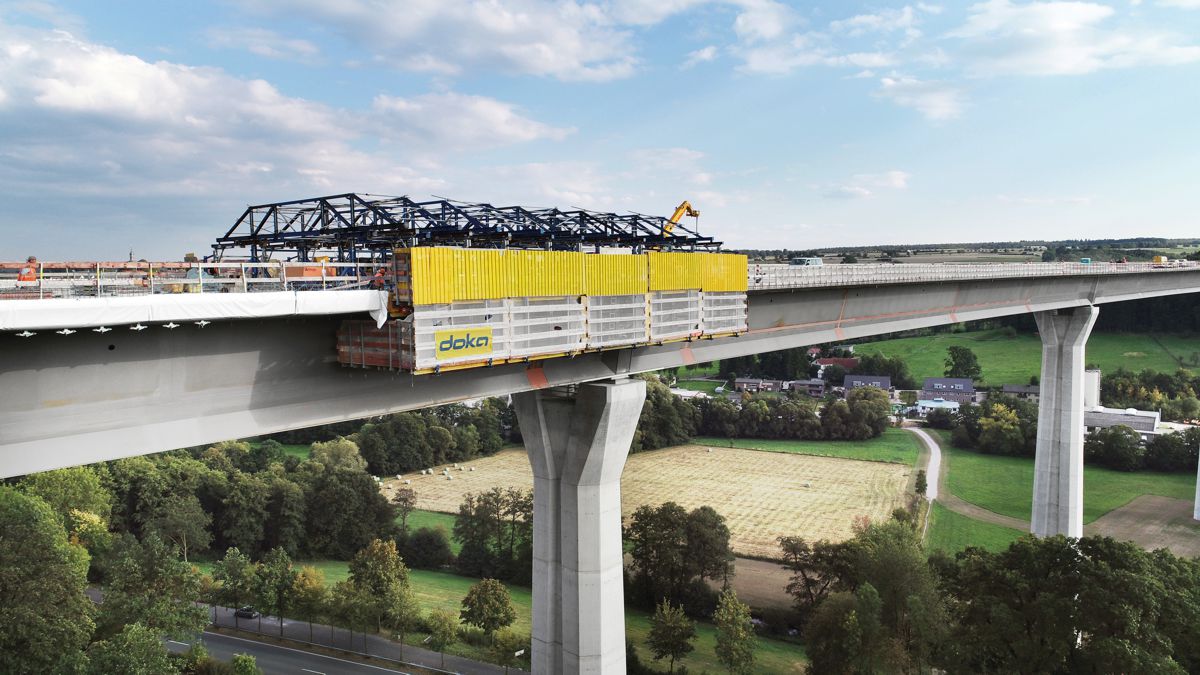
In other words, before an actual bridge is built, we have to build interpersonal bridges. Only in this way great things – such as the Aftetal bridge – can happen. In the case of the massive piers, the responsible construction company Max Bögl relied on the principle of automatic climbing formwork. The high-performance, fully hydraulic system from Doka climbed accurately and precisely, every step of the way. The distances climbed were always between five and six meters, up to the V-shaped pier heads, which required another special solution from the formwork experts.
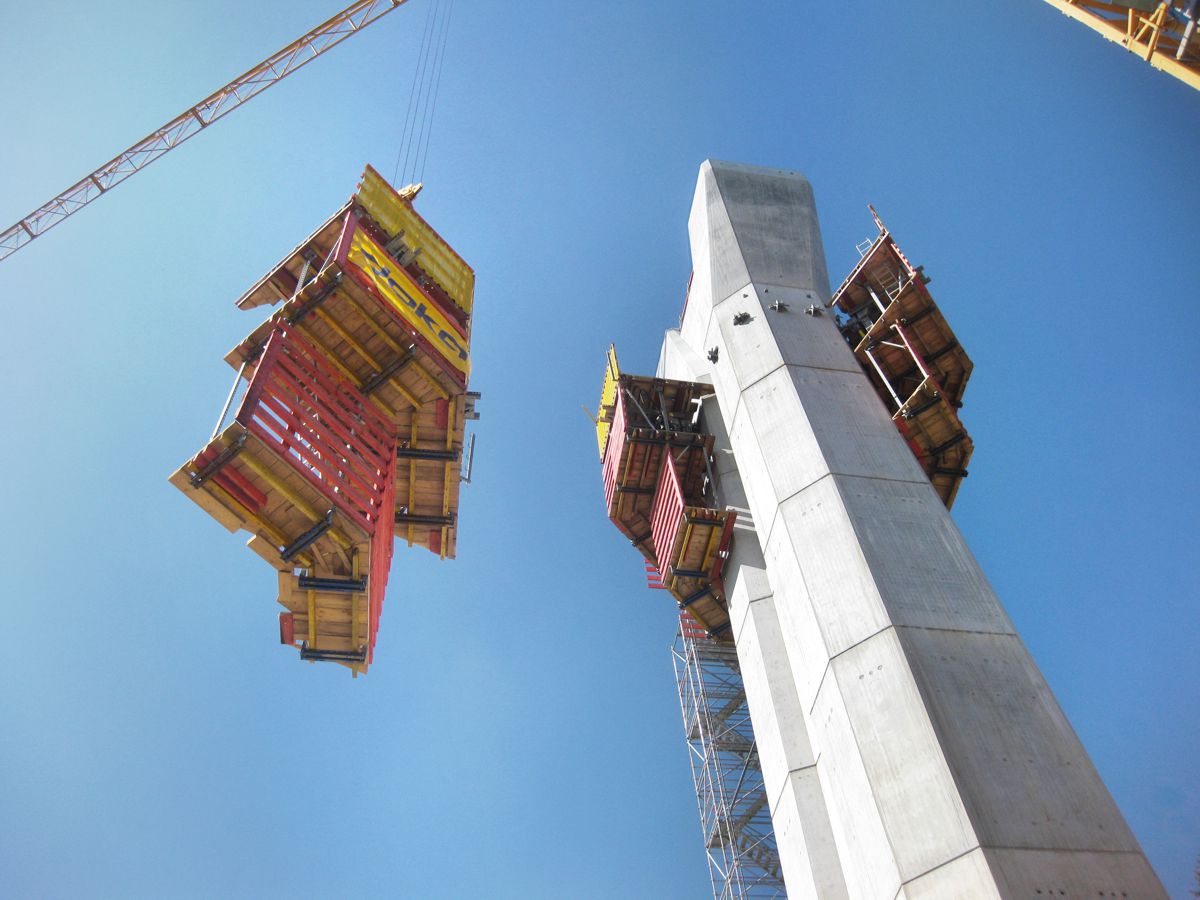
This is where the formwork preassembly team came into play. This Doka service pays off especially in the case of exceptional assembly activities, for example when assembling and dismantling or moving the formwork from one pier head to the next – especially since the in-house Doka service results in fewer interfaces and coordination work at the construction site. This is particularly relevant since, in addition to cost savings, it is always the time factor that makes project partners more open to innovative or unconventional solutions. For example, Max Bögl used two composite forming carriages at the Aftetal bridge to join the steel trough with the concrete of the deck slab.
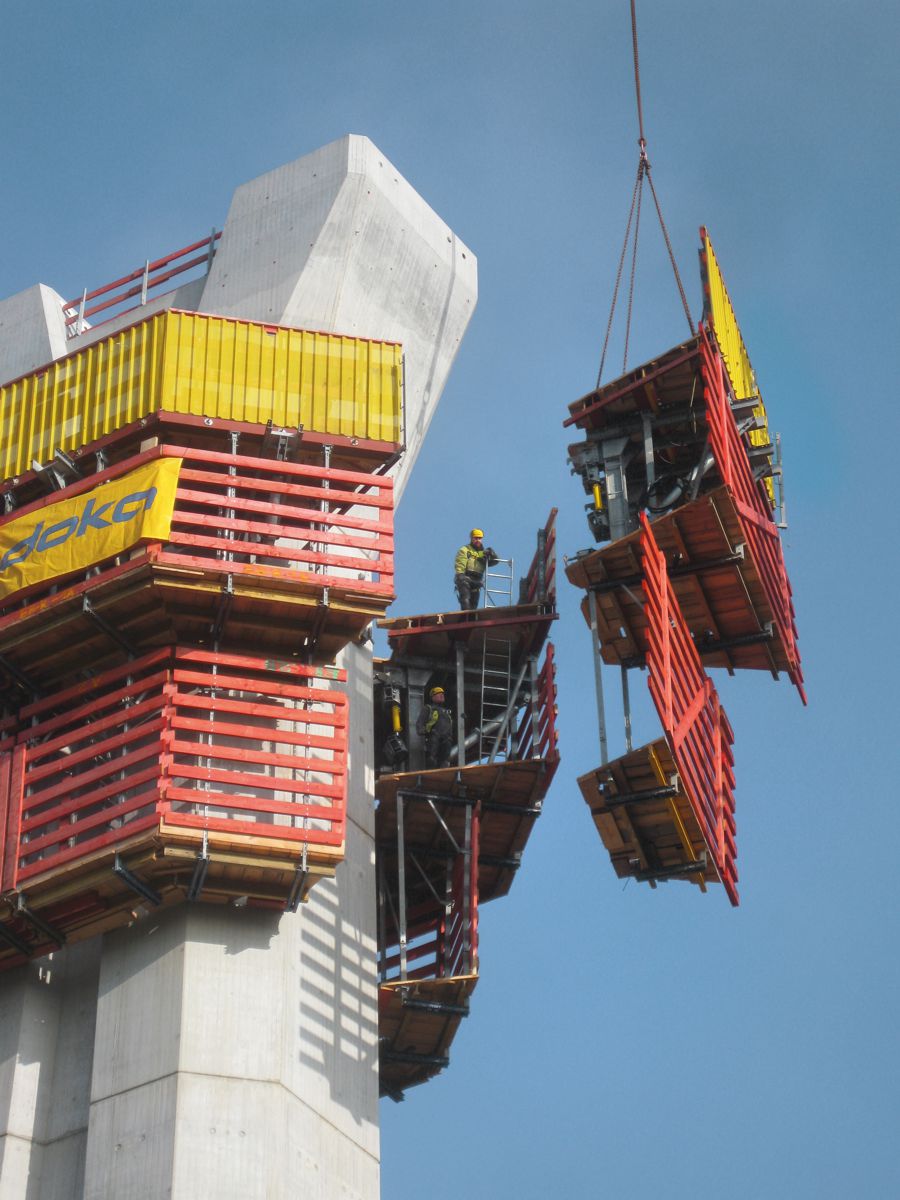
To create the cantilevered parapets with parapet wall, a composite forming carriage with two trailing parapets forming wagons, the so-called Forming wagon TU, was deployed. This “pas de deux” saved a lot of time, as the engineers are pleased to point out – especially since the construction site also relied on the experienced formwork preassembly technicians.
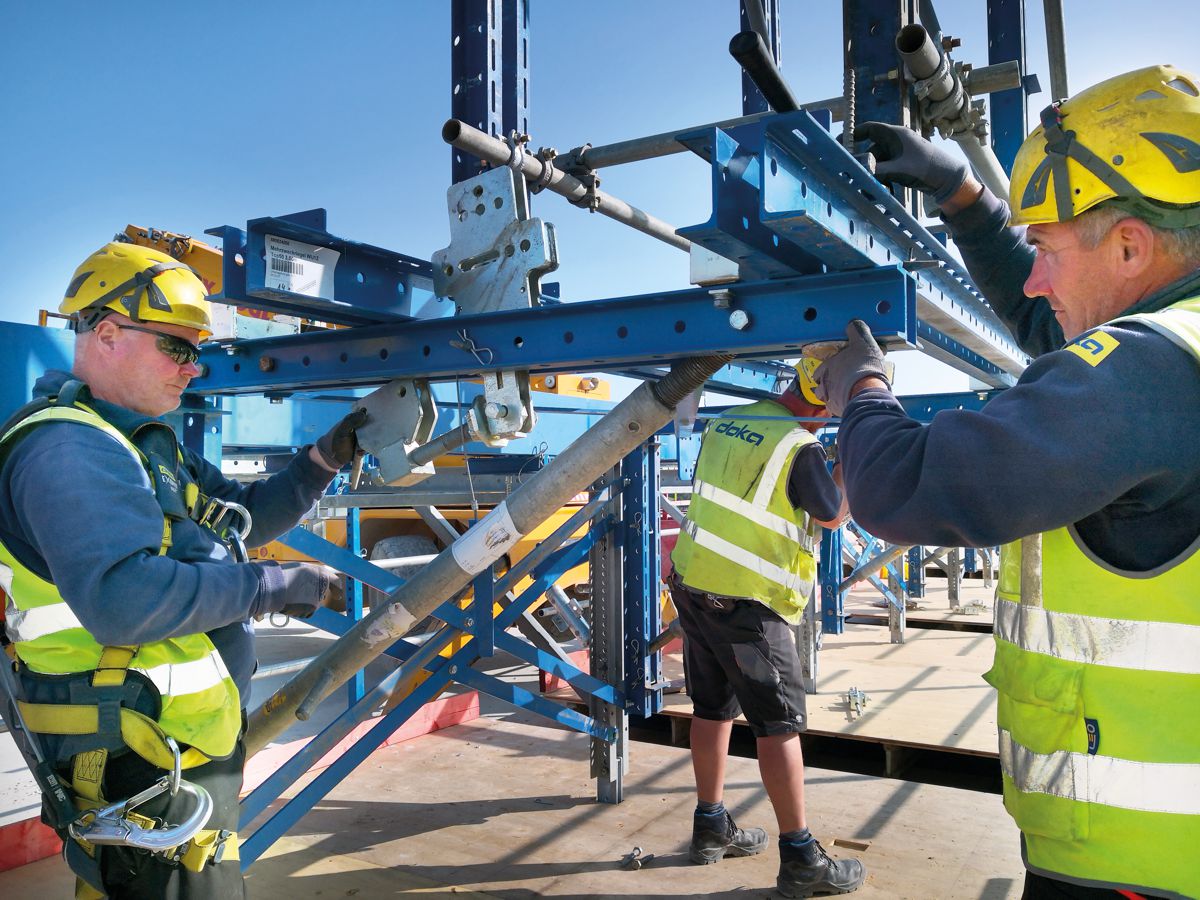
So what is the takeaway after four years of working on the Aftetal bridge project? The joy of having provided comprehensive support for the project. The high priority that was given to the issue of safety. And the fact that Doka provided the highest levels of consultation and service. And not only because high above and far beyond is in the nature of bridge structures.
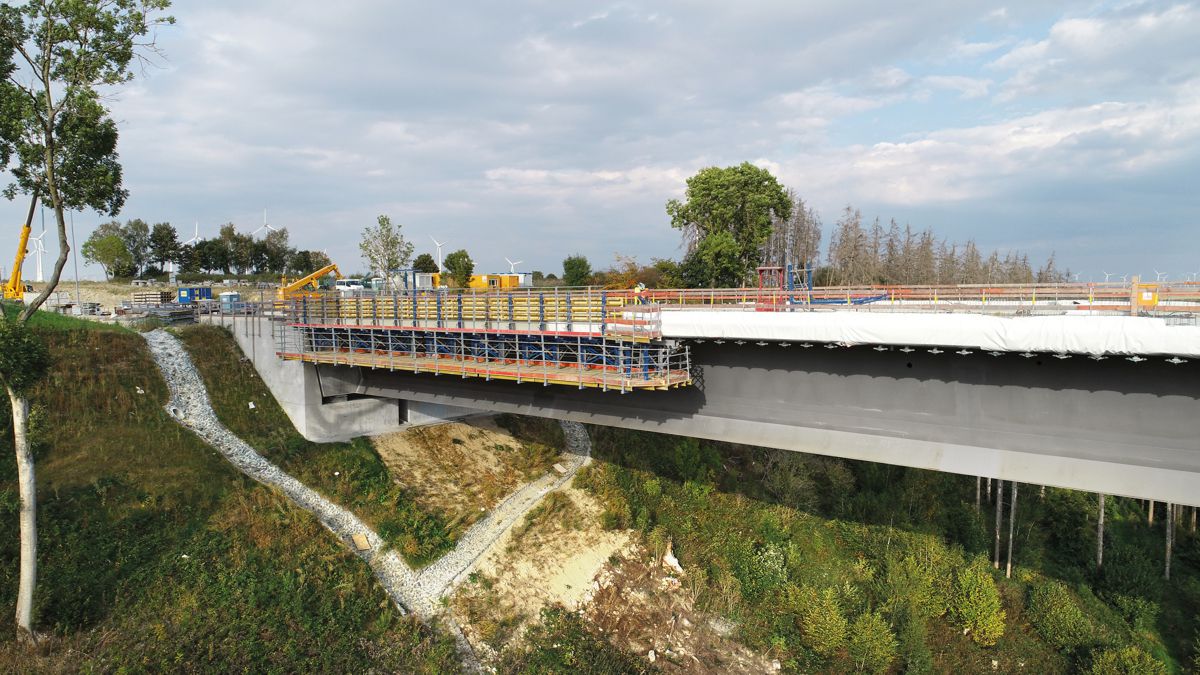