Hytera Global Manufacturing Centre adopts Industry 4.0 Smart Manufacturing
The smart factory transformation is beginning to take place in many different manufacturing sectors and the Professional Mobile Radio (PMR) industry is no exception. The new Hytera Global Manufacturing Centre, a 110,000m² Industry 4.0 smart factory in Shenzhen, already operates with an automation rate of 50%.
The Centre’s Intelligent Manufacturing Management System provides visual oversight of the whole process from raw materials entering the factory to finished products leaving the Centre using a 5G-enabled, camera-based AI detection system. This is also used to enhance worker safety by detecting if a worker has collapsed, for example, and sending an alert.
Smart processes are introduced right from the start as raw materials entering the factory are carefully inspected to eliminate flaws, which helps to reduce product failure later on. Class 4 laser marking is used to create a code for each printed circuit board, so its origin can be traced. Every small component that goes into a product is made traceable and trackable for more efficient handling within the factory.
Printed circuit boards lie at the heart of any radio product, so it is essential that they are manufactured and assembled in clean conditions to avoid foreign objects like dust getting in. To prevent this, Hytera has created Class 100,000 cleanrooms by deploying advanced micron-scale dust removal technology.
Surface-mount technology (SMT) pick-and-place equipment is used to manufacture the printed circuit boards. SMT ensures components are precisely aligned on the printed circuit boards in a consistent way. Quality control is enhanced by the deployment of contour automatic optical inspection (AOI) detection technology.
Once the individual components and units are finished they are integrated on the fully automated assembly line. This provides rapid, efficient and highly reliable equipment assembly to ensure a consistent product build process. This helps to guarantee the quality of the finished product.

Products are then subject to stringent quality control tests conducted in the Reliability Test Laboratory (RLT), which provides material certification testing, new product testing, and product cycle reliability testing. Over 50 types of test equipment are deployed to carry out 22 reliability tests to make sure every product meets the required quality standard.
If problems are detected, the Failure Analysis Laboratory analyses the component or product to find out why it has failed. The results are fed back to designers to see if similar problems can be eliminated in the future.
Improving sustainability is a key consideration in smart factory design. The Hytera facility was able to save 3.6 million kWh of electricity in 2021, while energy consumption was reduced by 30%. The energy saving was achieved via the smartphone-based Energy Consumption Monitoring System app, which auto-controls major energy consumption devices in the factory such as air-conditioning and water cooling systems.
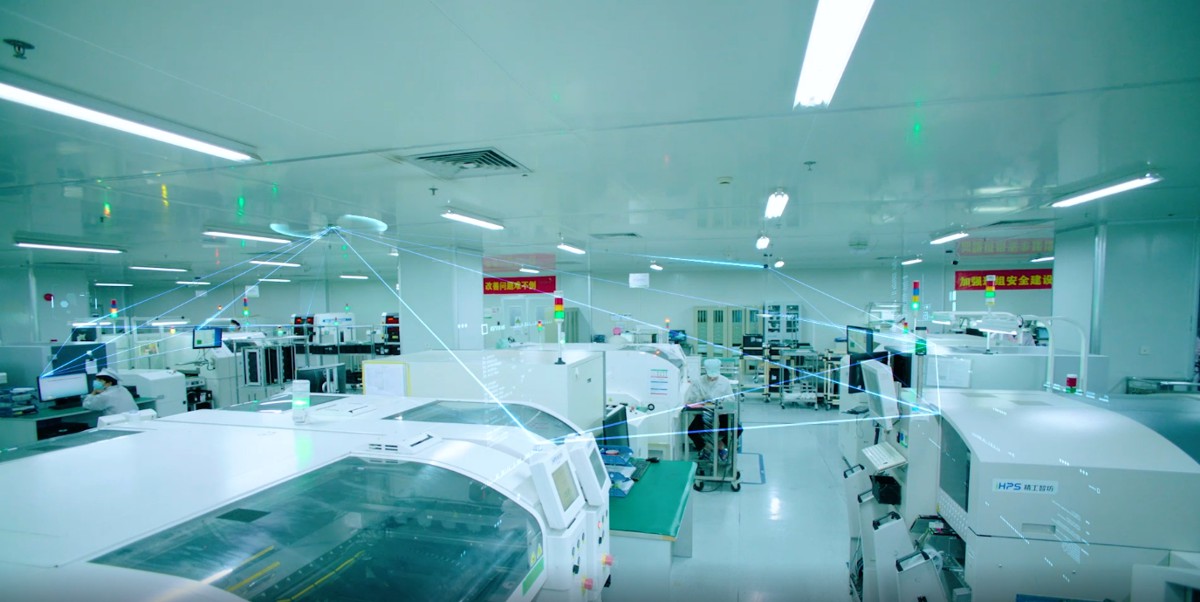
Smart manufacturing is still a relatively new concept, but the digitalisation of manufacturing is clearly the way of the future. By deploying new technology, such as automated processes, combined with near or real-time performance data analysis, manufacturers can improve product development, design and manufacture. When smart supply chain management, sales and post-sales support are added, customers will enjoy a better experience.
For most manufacturers, the key priorities are to reduce direct and indirect costs, but it should not be forgotten that improving the customer experience is equally important. Improving product quality, reliability and reducing time to market will deliver a better customer experience.
The 200 manufacturing engineers and 2,000 skilled workers in the Hytera Global Manufacturing Centre are at the forefront of the digital transformation of manufacturing in the PMR industry. In 2021, the Centre produced and shipped more than 1.3 million professional mobile radio terminals to Hytera customers across the globe to provide them with high-quality products they can rely on.
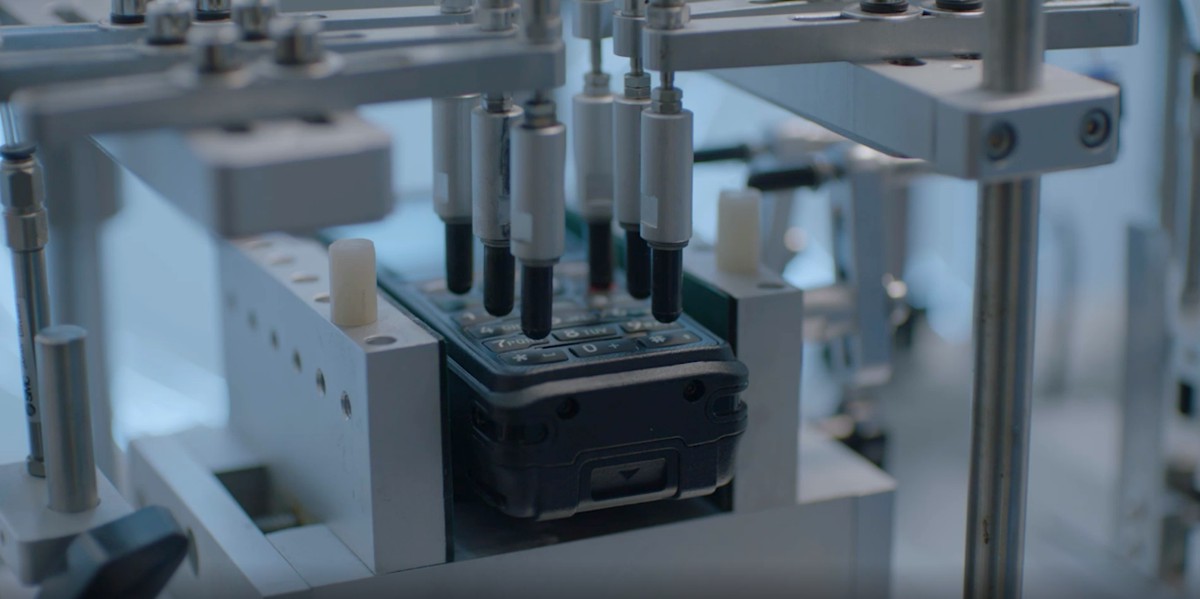