Wirtgen Slipform Pavers bringing innovation and a world premiere to bauma 2022
In addition to the SP 15(i) and SP 20(i) offset pavers at this year’s Bauma, Wirtgen is also showing a complete paving train for fully reinforced concrete paving.
This consists of a WPS 102(i) placer/spreader, an SP 94(i) inset paver and a TCM 180(i) texture curing machine. Also making an appearance at the show is an SP 124(i) with a new, integrated dowel bar inserter. All compatible machines at the show will also feature Wirtgen’s own, specially developed, AutoPilot 2.0 control system for stringless paving.
World premiere of the SP 20(i) offset paver
The production of concrete safety barriers with a height of up to 2 metres and the paving of flat surfaces with widths of up to 2.5 metres are typical applications for the SP 20(i) offset paver. With the new machine, Wirtgen offers its customers the ideal combination of productivity and mobility. Despite the large paving widths and heights it offers, the machine has a low transport weight and compact dimensions.
The compact SP 15(i) has been delivering outstanding performance in a wide range of application scenarios around the world for many years. In Munich, it can now be seen in a version fitted with a ‘Curb Depressor Mould’. This enables the automatic paving of lowered curb profiles, e.g. for access to driveways. The paving process can proceed without interruption and the need for manual reworking is significantly reduced.
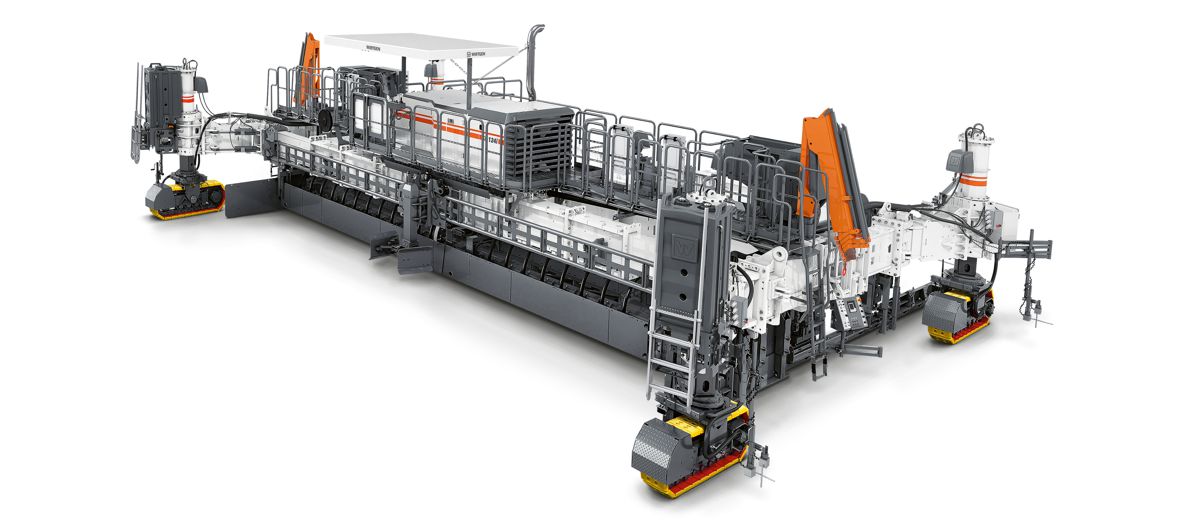
Concrete paving train for high quality, cost-effectiveness and flexibility
In the case of the inset pavers, Wirtgen is showing a train of three perfectly coordinated machines for the paving of high quality concrete traffic infrastructure. All three feature concrete paving equipment with the Imperial dimensions typical for the US market.
The paving train is set up for a working width of 24 ft (7.3 m). A placer/spreader such as the WPS 102(i) generally comes into play when paving over pre-placed steel rebar. It travels in front of the slipform paver over the pre-placed steel rebar, while concrete is fed to the belt conveyor swung out from the side from a concrete mixer or a tipper truck. The concrete is poured evenly over the pre-placed reinforcement in front of the slipform paver and distributed across the entire working width.
The SP 94(i) slipform paver then compacts and paves the concrete mix. The paver at the show, which has a maximum working width of 9.5 metres (32 ft), is fitted with a TeleMold system. It enables fast and convenient alteration of the working width by up to 0.9 metres (3 ft) on each side, resulting in an overall increase of 1.8 metres (6 ft). This increases the flexibility and productive utilisation time of the machine by the reduction of down times. The final link in the process chain is the TCM 180(i). This field-proven texture curing machine applies the desired finish to the surface of the freshly paved concrete.
It enables the realisation of lengthwise and crosswise textures and pre-defined surface roughness in accordance with project specifications. It also allows the application of a range of different curing agents to the concrete surface, for example a concrete surface retarder.
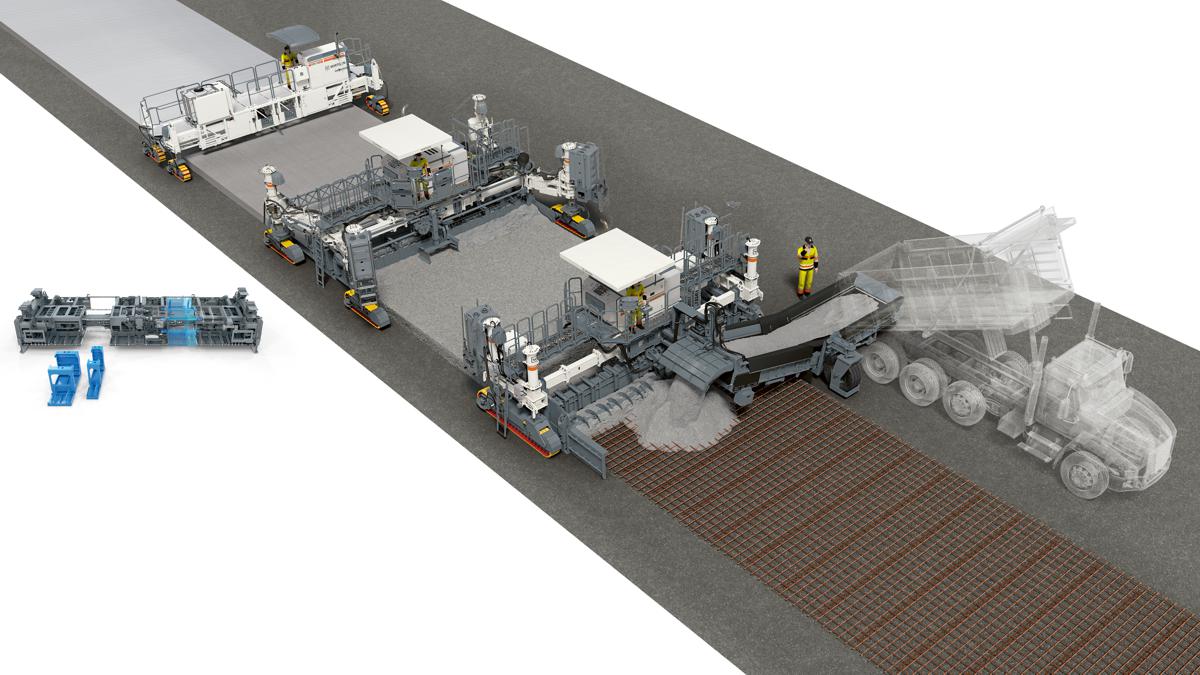
SP 124(i) 12-metre paving width, 4 swing arms, new dowel bar inserter
The largest slipform paver on show at this year’s Bauma is the SP 124(i). The 4-track paver can be configured for paving at a working width of 12 metres and fits seamlessly into the fleet-wide operating concept of slipform pavers from WIRTGEN.
The machine is fitted with the latest generation of the integrated dowel bar inserter. The dowel bars are extracted from the magazine by a chain feed system with an endless chain and automatically transported to the insertion location. ‘Smart’ cylinders with displacement sensors precisely position the dowel bar inserter at the desired locations.
The high degree of automation reduces the amount of manual work required, increases process reliability and, ultimately, the cost-effectiveness of the process.
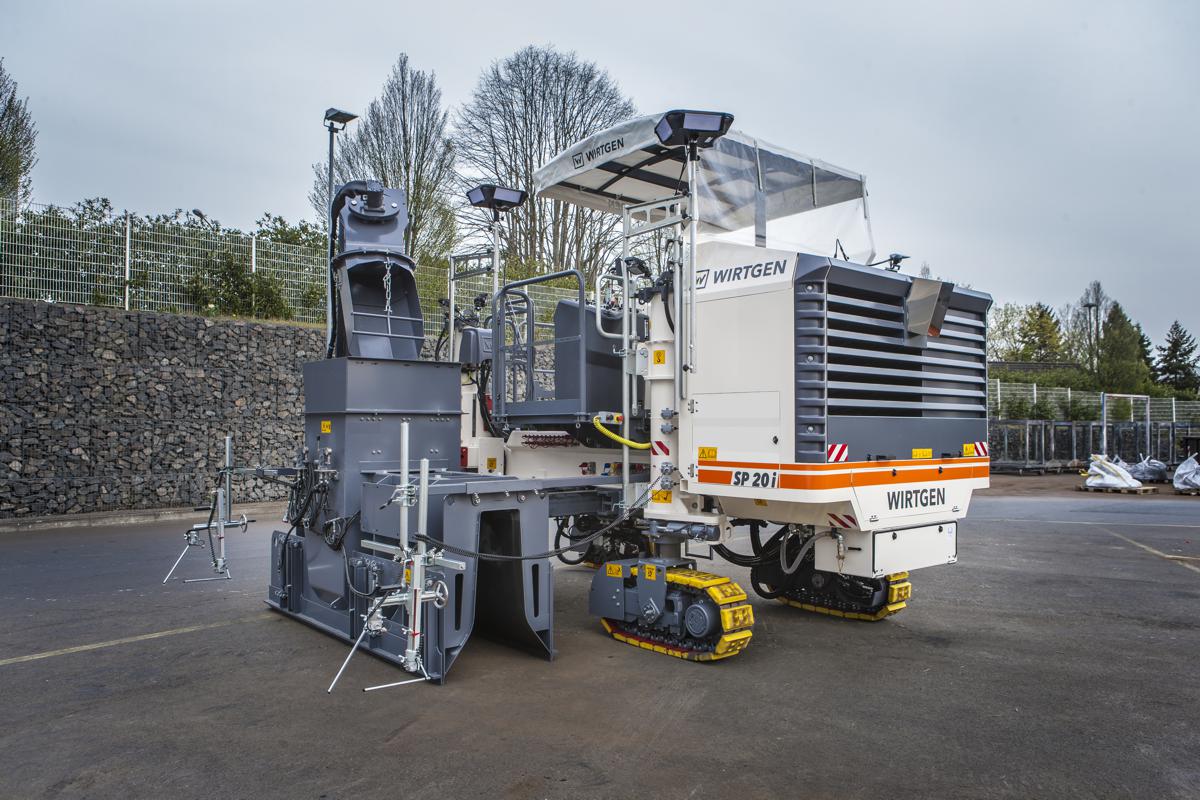
AutoPilot 2.0: stringless control for concrete paving
Developed in-house by Wirtgen, AutoPilot 2.0 is a control system for stringless paving that serves as an alternative to the conventional method of mechanically scanning a stringline.
The system, which precisely controls both the height adjustment and steering of the machine, is available for all offset pavers and placer/spreaders. A GNSS signal and, depending on the configuration, various local sensors (e.g. an ultrasonic sensor on the machine), serve as a reference.
The time and effort otherwise required for setting up and removing the stringline is eliminated. It also enables fast and precise paving of tight radii and complex geometries. The system is conveniently operable from a tablet PC, which also supports the generation and editing of terrain models.
Wirtgen AutoPilot 2.0 is the only system that offers machine control and stringless control for concrete paving in one.