New Battery Cathode design promises better Lithium-ion Batteries
Researchers at the U.S. Department of Energy’s (DOE) Argonne National Laboratory have a long history of breakthrough discoveries with lithium-ion batteries. Many of these discoveries have focused on a battery cathode known as NMC, a nickel-manganese-cobalt oxide. Batteries with this cathode now power the Chevy Bolt.
Argonne researchers have made another breakthrough with the NMC cathode. The team’s new structure for the cathode’s micro-sized particles could lead to longer lasting and safer batteries able to operate at very high voltage and power vehicles for longer driving ranges.
“The present-day NMC cathode has posed a major barrier to operation at high voltage,” said Guiliang Xu, assistant chemist. With charge-discharge cycling, performance rapidly declines due to cracks forming in the cathode particles. For several decades, battery researchers have been seeking ways to eliminate these cracks.
One past approach involved microscale spherical particles consisting of numerous much smaller particles. The large spherical particles are polycrystalline, with differently oriented crystalline regions. As a result, they have what scientists refer to as grain boundaries between particles, which cause cracking upon battery cycling. To prevent this, Xu and Argonne colleagues had previously developed a protective polymer coating around each particle. This coating surrounds the large spherical particles and smaller ones inside them.
A different approach to avoid this cracking involves single-crystal particles. Electron microscopy of these particles indicated they have no boundaries.
The problem the team faced was that cathodes made from both coated polycrystals and single crystals still formed cracks with cycling. So, they subjected these cathode materials to extensive analyses at the Advanced Photon Source (APS) and Center for Nanoscale Materials (CNM), DOE Office of Science user facilities at Argonne.
Different X-ray analyses were carried out at five APS beamlines (11-BM, 20-BM, 2-ID-D, 11-ID-C and 34-ID-E). It turned out that what scientists had believed were single crystals, as evidenced by electron and X-ray microscopy, actually had boundaries inside. Scanning and transmission electron microscopies at CNM verified the finding.
“When we look at the surface morphology of these particles, they look like single crystals,” said physicist Wenjun Liu. “But when we use a technique called synchrotron X-ray diffraction microscopy and other techniques at the APS, we find boundaries hiding inside.”
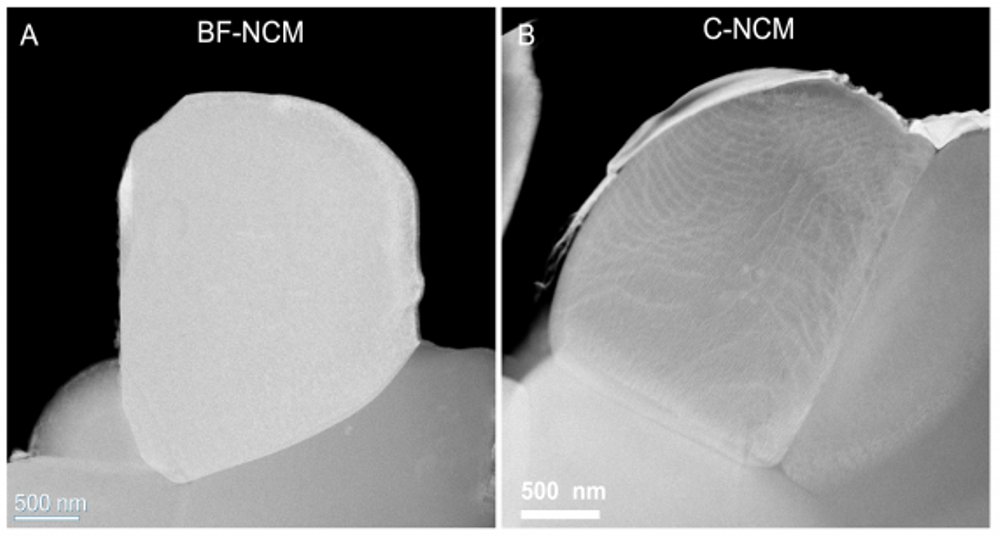
Importantly, the team developed a method for producing boundary-free single crystals. Testing of small cells with such single-crystal cathodes at very high voltage showed a 25% increase in energy storage per unit volume, with almost no loss of performance over 100 cycles of testing. By contrast, over the same cycle life, the capacity declined by 60% to 88% in NMC cathodes composed of single crystals with many internal boundaries or with coated polycrystals.
Calculations at the atomic scale revealed the mechanism behind the capacity decline in the cathode. According to nanoscientist Maria Chan in CNM, compared to the regions away from them, boundaries are more vulnerable towards the loss of oxygen atoms when the battery is being charged. This oxygen loss leads to degradation with cell cycling.
“Our calculations showed how boundaries lead to oxygen release at high voltage and, therefore, performance decline,” Chan said.
Eliminating the boundaries prevents oxygen release and thereby improves the cathode safety and stability with cycling. Oxygen release measurements at APS and the Advanced Light Source at DOE’s Lawrence Berkeley National Laboratory supported this finding.
“We now have guidelines that battery manufacturers can use to prepare cathode material that is boundary free and works at high voltage,” said Khalil Amine, an Argonne Distinguished Fellow. “And the guidelines should apply to other cathode materials besides NMC.”
A paper on this research appeared in Nature Energy. In addition to Xu, Amine, Liu and Chan, Argonne authors include Xiang Liu, Venkata Surya Chaitanya Kolluru, Chen Zhao, Xinwei Zhou, Yuzi Liu, Liang Yin, Amine Daali, Yang Ren, Wenqian Xu, Junjing Deng, Inhui Hwang, Chengjun Sun, Tao Zhou, Ming Du and Zonghai Chen. Also contributing to this project were scientists from Lawrence Berkeley National Laboratory (Wanli Yang, Qingtian Li and Zengqing Zhuo), Xiamen University (Jing-Jing Fan, Ling Huang and Shi-Gang Sun) and Tsinghua University (Dongsheng Ren, Xuning Feng and Minggao Ouyang).
The research was supported by the DOE Vehicle Technologies Office.