Techmer PM and Purdue CMSC set to revolutionize Additive Manufacturing
When the Director of Additive Manufacturing Dr. Eduardo Barocio joined Purdue close to a decade ago, he wanted to make a meaningful impact on the industry, and understood that the emerging technology had its own unique set of challenges.
On October 19th, at CAMX in Anaheim, CA, Eduardo, alongside Techmer PM’s Anthony Fiorini, will be discussing a revolutionary simulation workflow designed to help companies reduce development time/cycles, reduce wasted material, and improve the physical properties of their finished products.
The presentation titled “Validated Simulation for Large Scale Additive Manufacturing” will explore the inherent challenges when 3D printing massive parts. “Without the Additive3D simulation workflow, companies run the risk that their designs will not print successfully,” said Dr. Barocio. “But now, users can accelerate the development process and production of their printed parts while reducing the design costs and waste material.”
“We are excited to continue partnering with Purdue’s CMSC team and now have three of our key material technologies characterized within their simulation software,” said Fiorini, Techmer PM’s Business Development Manager for Additive Manufacturing.
During their presentation, the duo will share case studies detailing real-life successes and examples of projects that could have avoided costly failures had they used this innovative simulation tool.
“Incorporating this sustainable technology is expected to save our customers hundreds of hours of development time,” said Kara Noack, Techmer PM’s Director of Engineered Compounds.
“There’s no doubt it will accelerate the design and production of tooling and other parts while reducing costs, benefiting new technology users, equipment manufacturers, and materials suppliers,” she added.
The software, titled ADDITIVE3D, is available for members of the Purdue CAMS Consortium, who will also gain access to a library of Techmer materials already characterized for use in the ADDITIVE3D simulation workflow.
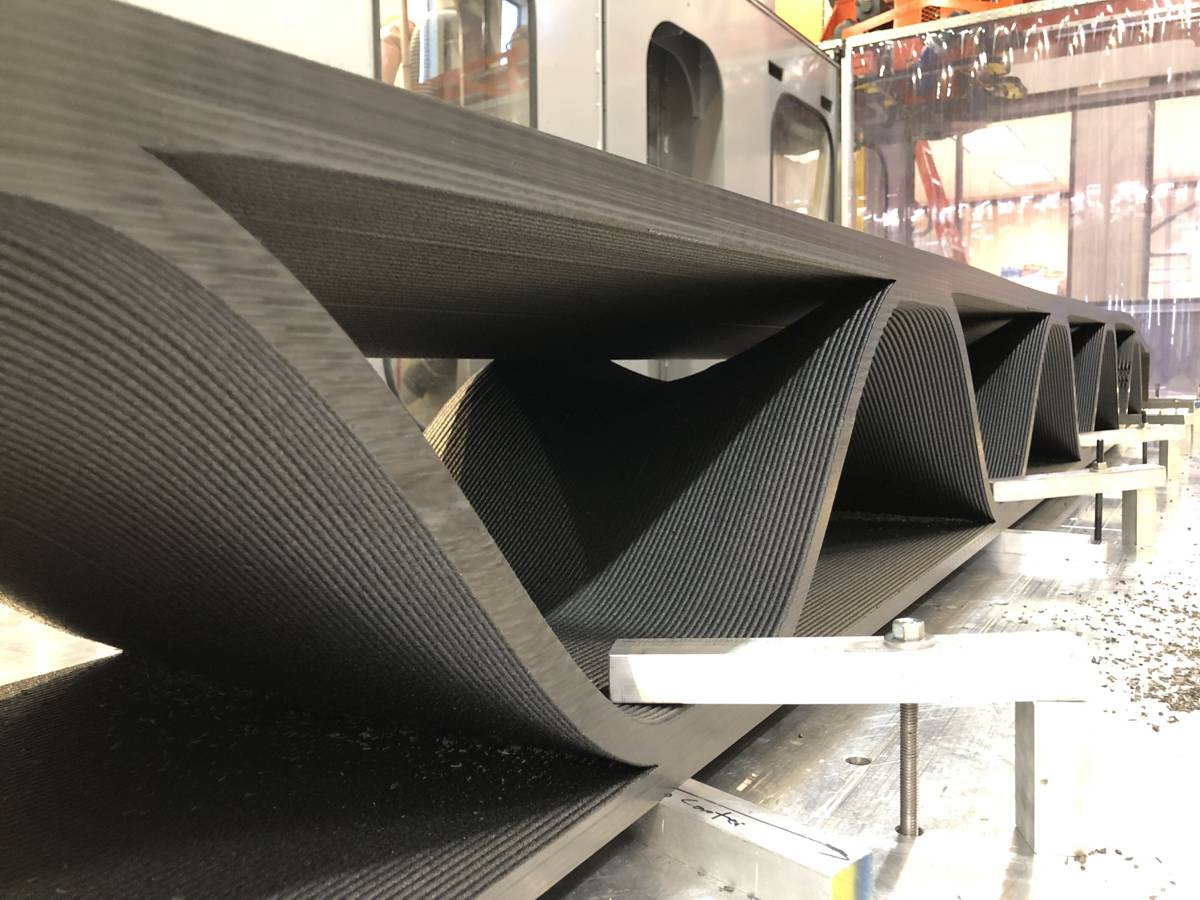