Fibre-reinforced Concrete speeds up Metro Phoenix Light Rail Extension Construction
Using fibre-reinforced concrete instead of rebar-supported slabs for constructing Metro Phoenix light rail extensions is giving new meaning to rapid transit. Months of construction time are being reduced to weeks, adding cost savings, sustainability and worker safety to the mix.
A collaboration between Arizona State University, the Phoenix Valley Metro Regional Transportation Authority and Kiewit-McCarthy, the project’s construction firm, began with a materials upgrade proposal from Barzin Mobasher, an ASU professor of structural engineering in the School of Sustainable Engineering and the Built Environment.
The project, which extended the light rail by 1.5 miles, incorporated the fibre-reinforced concrete design and was completed in early May.
Reinforcing bar, or rebar, is made of steel and embedded in concrete to strengthen structures. According to Mobasher, more than 60% of the volume of concrete used throughout the world has zero tensile efficiency and is unable to carry load. This makes concrete used in load-bearing structures like the light rail susceptible to cracks, which begin very small and grow unhindered until there is a fault in the structure.
Incorporating rebar provides the loadbearing strength required for most concrete-based construction. However, laying rebar is costly, leaves a dramatic carbon footprint, presents worker safety risks and above all, takes a great deal of time. As the inevitable concrete cracking escalates and the rebar corrodes, additional maintenance, repair and rehabilitation are required, further adding to costs and neighbourhood disruption.
Mobasher’s proposal simplified challenges for the light rail extension project and delivered a successful new system “just by making one change in the design criteria – using fibres in the concrete mix instead of reinforcing with rebar,” he said.
Instead of using two layers of rebar in cross directions to support the light rail’s electrified track in the extensions, Mobasher’s design and validation approach considered both steel and polymeric fibres added directly into the concrete, completely eliminating the need for rebar reinforcement. Finally, steel fibres were chosen by Valley Metro for the northwest extension project.
Thin fibres of steel and polypropylene are being used in in the concrete mixture for Phoenix Valley Metro’s light rail extension. Using the fibres instead of rebar cuts costs and construction time as well as decreasing the carbon footprint and increasing sustainability. Photo by Charlie Leight, ASU News
To validate the proposal, a series of serviceability tests were conducted in ASU’s Structural and Materials Lab. Testing involved creating full-size mock-ups for both rebar-reinforced concrete and fibre-reinforced concrete, in the same ratios as full-size sections. Side-by-side testing allowed comparisons of strength and flexibility as well as documentation of concrete cracking and fatigue susceptibility.
The testing process also projected cost and construction time savings. For example, the per mile construction of the extension using rebar was projected at 231 days, while using fiber-reinforced concrete reduced it to 121 days, with a cost savings of more than $12 million.
“The idea of taking several long rebars that are half an inch in diameter, separated by 12 to 18 inches and built into a cage that is 12 inches above ground and replacing them with a fibre material, which is 2 inches long and only 1/32nd of an inch in diameter and mixed in with the concrete, might seem on scale non-competitive,” Mobasher said.
“But if you have thousands of those small fibres distributed in there, they become much more effective in arresting the cracks — working as small Band-Aids to keep the cracks closed and transfer the load. (Fibre-reinforced concrete) can be designed to bear up to an unprecedented 40% of the tensile load capacity of concrete.”
“We did the fatigue tests to simulate conditions for up to 45 years of service at much higher expected loads as proof of concept, and they accepted the proposed approach,” said Mobasher of the approvals from Valley Metro and the city of Phoenix. “It’s been a tremendous experience for them to save the amount of materials used and, at the same time, to be able to meet the project at costs much lower than the original budget and in a much faster time frame.”
The Valley Metro project is expected serve as a prototype for similar light rail upgrades nationally and will be presented at an international Fibre-Reinforced Concrete Workshop hosted by ASU in September.
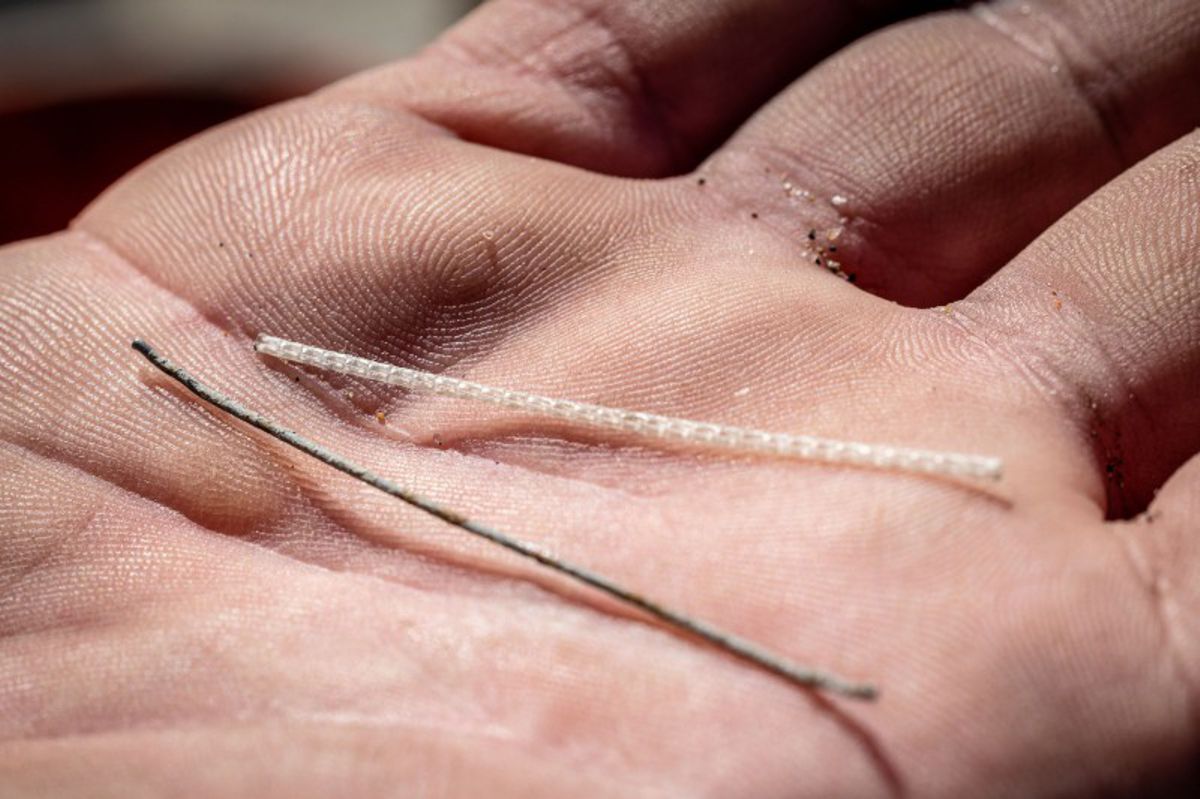
Construction time
A major obstacle for community approval of light rail transit is months of neighbourhood disruption during construction. Using fibre-reinforced concrete instead of rebar-supported designs significantly reduces disruption to weeks or, in some cases, days.
Workers prepare to pour the last section of concrete for the northern spur of the light rail line North of Dunlap Avenue on 25th Avenue on May 5. The fibre-reinforced concrete mixture incorporates polypropylene or steel fibres, which are much less expensive and time-consuming than the traditional rebar reinforcement method. Photo by Charlie Leight/ASU News
Andrew Haines, project manager for Jacobs Engineering in Tempe, attributed the success of the materials change to “challenging the accepted.”
“There’s an accepted way of doing reinforced concrete in the United States, especially with regard to light rail,” Haines said. “I think engineers get into this track of just, ‘We’ve got to do it a certain way, that’s how it’s always been done,’ and it’s been very difficult to change that — to accept something new.
“The placement of the concrete with the fibres has been very simple,” Haines said. “There’s no reinforcement — there’s no bars in the track slab for workers to try to walk on and perhaps slip on. So, it’s just the prepared earth and the rails are in place and the concrete gets placed around it — the reinforcement is integral with the concrete.”
The ability to develop material samples and test them in the ASU labs was a major component of implementing the change, according to Haines.
“We did all the right things to get this implemented in the field,” he said. “And the result seems to be phenomenal.”
According to Mobasher, the fibres are added into the concrete mix at the plant before being transported by the ready-mix trucks to the construction site. The entire mix is then discharged and self-consolidates, leaving a smooth, finished concrete surface.
“The work that used to take weeks to be done is finished in a matter of hours because we don’t need a crew laying up the steel rebars, connecting them, making sure they are all adequately welded together and that the components are all grounded,” Mobasher said.
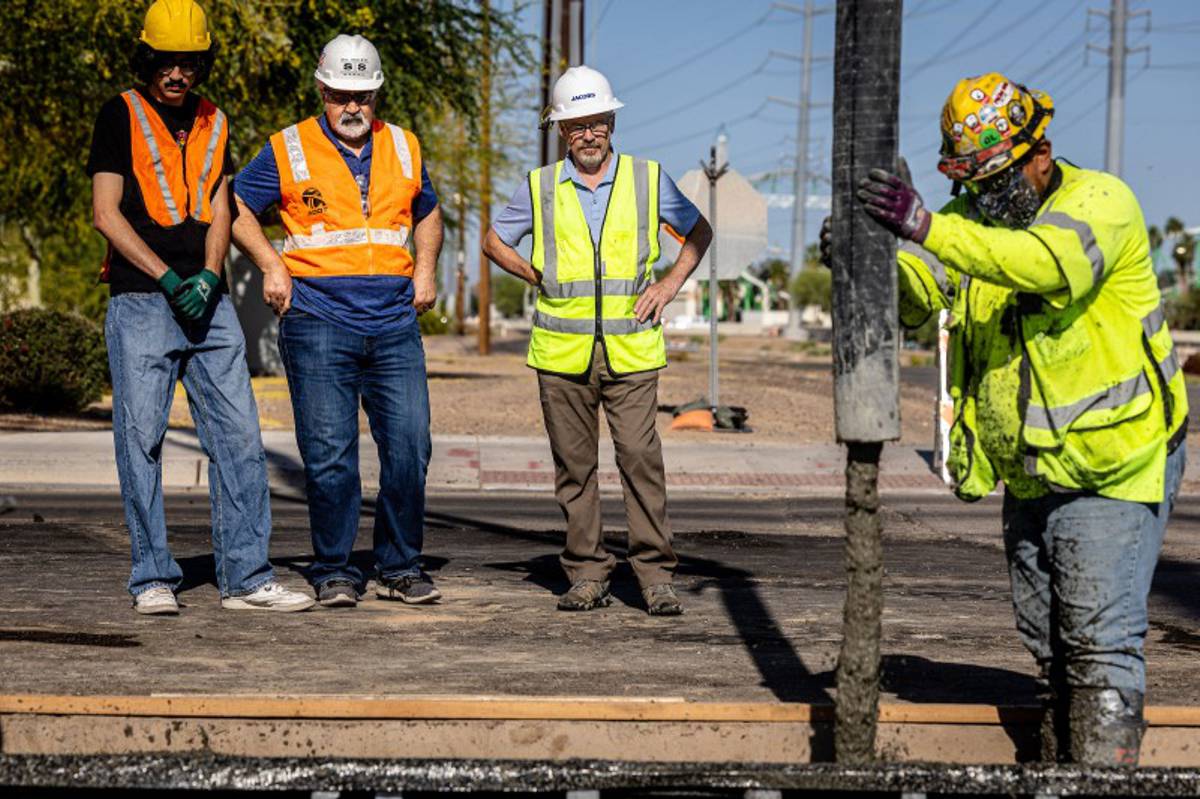
Construction and materials costs
In addition to cutting worker and equipment costs, there are savings associated with shorter security requirements at construction sites and lower shipping and concrete production costs. Also, the traffic delays and lost productivity due to lane closures are significantly reduced.
And while there are significant cost savings due to switching from rebar to steel fibres, additional savings are realized by the different types of fibres as well.
“With steel versus polymetric fibre there’s a tremendous difference in weight,” Haines said.
ASU Professor Barzin Mobasher (second from left), with the Ira A. Fulton Schools of Engineering’s School of Sustainable Engineering and the Built Environment, watches workers pour the last section of the northern spur of the Phoenix Valley Metro light rail extension. Photo by Charlie Leight/ASU News
With rebar, “we’re using 65 pounds of steel,” Haines said. “The production of steel produces a lot of greenhouse gasses — and a lot of energy to produce steel. There’s a lot less energy in using polymeric and synthetic fibers. We’re only using 12 pounds of polypropylene fibers vs. 65 pounds of steel, so there’s a savings there.”
The project also uses thinner sections of concrete than required to support and protect rebar.
“We’re using about 20% less concrete, which means we’re using 20% less cement,” Haines said.
A not-insignificant side benefit of eliminating rebar is a reduction of associated potential corrosion from the stray currents in an electrified transit system.
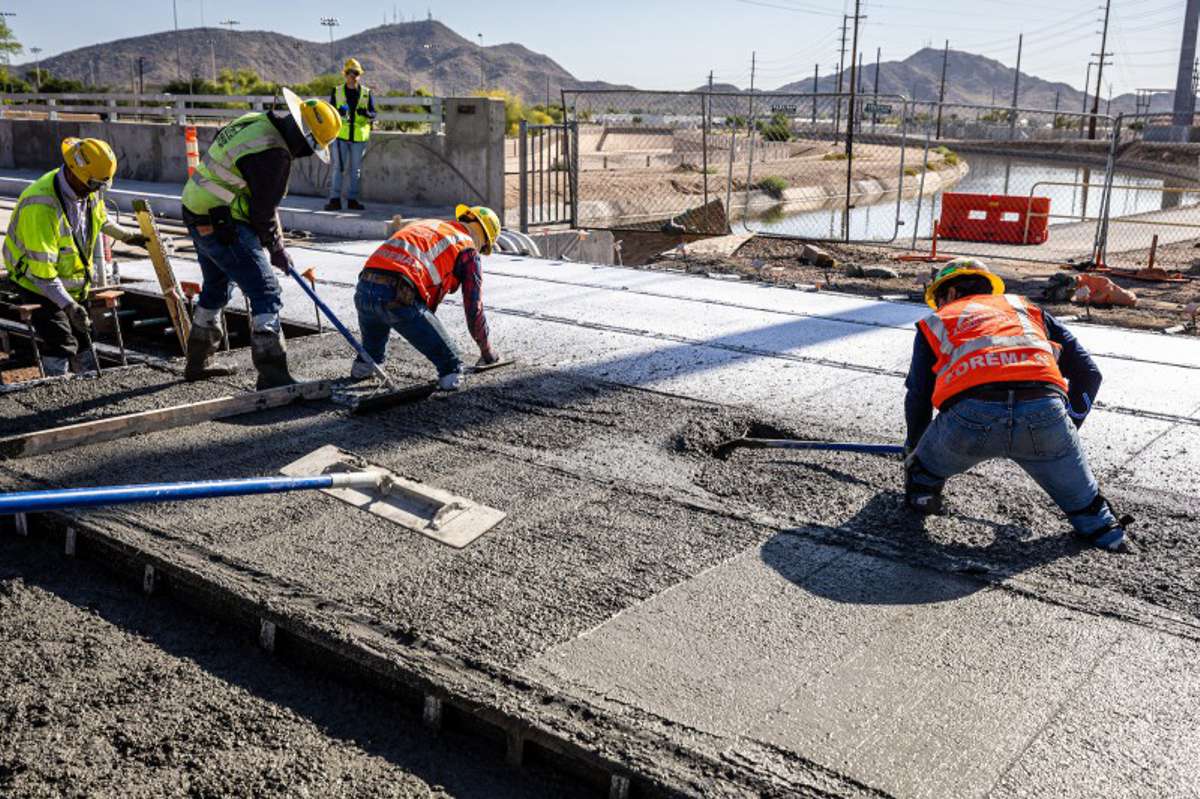
Worker safety
Walking on unstable rebars buried in fresh concrete is a challenging task.
“Imagine walking on shredded glass in a dark room while shovelling wet mud that weighs about 80 pounds. That is how the previous 25 miles or so was built,” Mobasher said.
“All we did was take out the rebar cage out so workers are finishing the slab without tripping as they navigate rebar in a 12-inch layer that can’t support their weight. Now, they are standing on solid ground as they pour the concrete around the rails.”
“The type of concrete we are using here is fibre-reinforced concrete,” said Farhad Rahimi, quality assurance manager for the city of Phoenix. “There is no rebar in this. It’s fiber inside the concrete, which makes the constructability much easier than rebar, and much faster. As for the quality, we get the same quality as we get from (standard) concrete. And, we got the tensile strength we need.”
Laying the concrete is “still very hard, labour-intensive work,” Mobasher said, “but definitely more humane. I have so much respect for these construction workers.
“The mission of sustainable engineering is to focus on long-lasting improvements of the human conditions, which includes both worker and environmental safety,” he said.
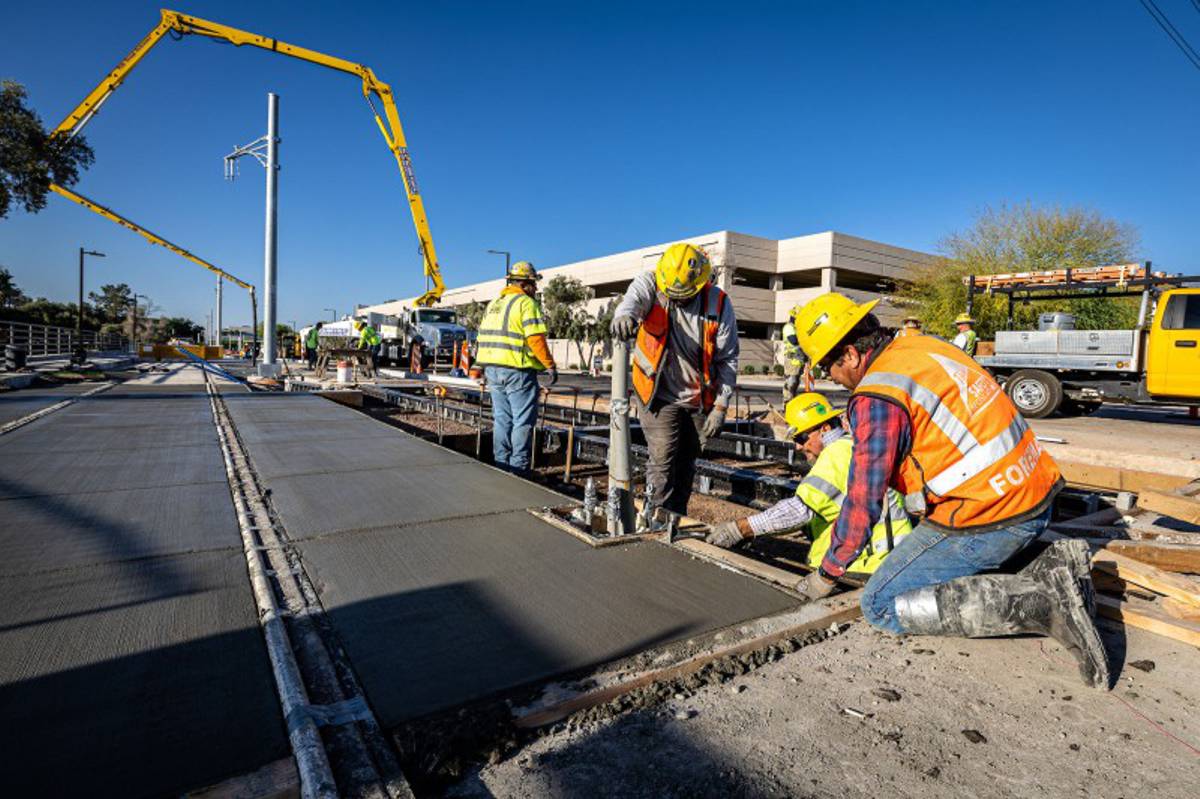
Sustainability benefits
“What we have learned in the last 50 years in materials science is that the closer we look at a microstructure, the better we can understand materials at a macro level,” Mobasher said.
The whole purpose of sustainable engineering is to design the material at a different level that may not sound intuitive, but that has load-bearing qualities that enhance longevity while reducing the carbon footprint.
“When we look at the carbon footprint of the construction materials, when we consider concrete and steel, we realize that we use about 30 billion tons of concrete every year throughout the world. We also use about 500 million tons of rebar for reinforcing that concrete to carry the load.
“That is a significant amount of carbon footprint because of just these two ingredients, because you cannot use concrete without providing reinforcement for it.”
Additionally, the testing validates stability for more than 45 years, with a likely service life under Phoenix climate conditions of more than 100 years, according to Mobasher.
One of Mobasher’s missions is to make these sustainable concrete technologies available to other cities and communities. Similar concrete formulas have been employed around the world, but they often come with proprietary constraints.
“In our laboratory, we provide a scientific basis for the design validation of structural components by combining the design codes, analytical and computer simulation design tools,” Mobasher said.
“Then we go a step further to verify the results with full-scale tests under the same loads the designers are concerned about. This approach gives us the ability to dial in the level of over-strength and conservativeness the engineers are comfortable with for the service life.”
ASU structural research labs have been involved with many such challenges – dealing with mining applications, environmental structures, canals, bridge design and steel structures – and have been an ongoing resource for testing new technologies in for both industry and communities.
“We want to show that the (fibre-reinforced concrete) construction process can be a do-it-yourself project for local communities working with local construction companies,” Mobasher said. “We can show that collaboration between municipalities, industry, government agencies and universities can come together to share resources, cut costs and increase sustainability.”
Read the original ASU News Article.