Balancing Railroad Level Crossing Safety and Performance
Today, the rail industry has multiple digital capabilities for the most precise asset monitoring and efficient railroad maintenance. The fact that the situation with accidents at level crossings in the US has remained virtually unchanged over the past 15 years raises questions.
It’s surprising that even active level crossings, which should have shown the effectiveness of digital countermeasures, haven’t improved incident statistics. The level crossing collision and injuries chart even show spikes and the crossing fatalities chart only slightly fluctuates (Figure 1). This raises doubts about the effectiveness of the countermeasures being taken. Why is this happening?
Firstly, road traffic is growing every year. We are witnessing an increase in the flow of cars on highways, which subsequently increases the potential amount of incidents at level crossings. The demand for railway transportation is also growing, which leads to the train flow boost, increasing the load on the level crossing equipment. So it turns out that the strengthening of countermeasures is comparable to the traffic surge, which allows the railroad industry to achieve only keeping the incident rate at the current level.
Secondly, let’s take a closer look at the maintenance procedure and the situation that precedes it. When a level crossing fails, it often remains in a state of failure until the public reports it. The incident is recorded, and railroad maintenance personnel are sent to the location without understanding the reasons for the failure, which may require additional research and time to fix the issue. The level crossing is under special control and may be closed until the issue is solved.
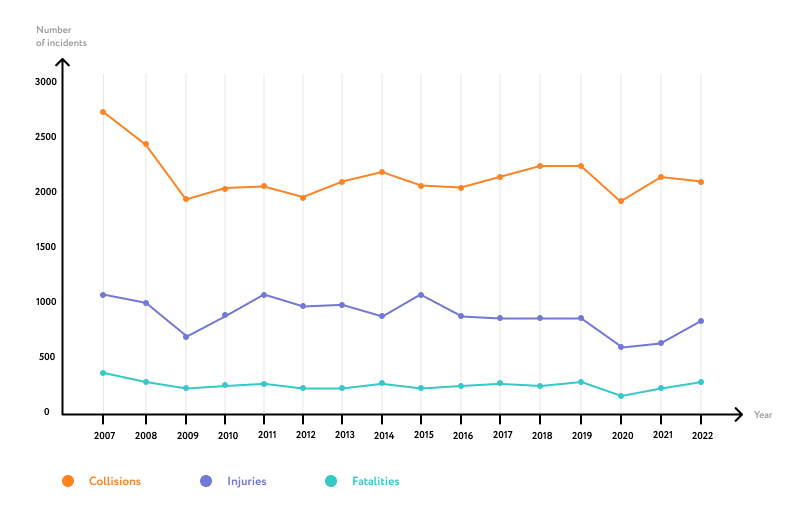
Thus, digital technologies now face a multi-vector task – to enhance safety at level crossings without affecting the traffic flow. There are opportunities available today, and ways to utilize them correctly.
Why to Focus on Railroad Maintenance at Level Crossings
Refining the railroad maintenance approach for level crossings involves minimizing the incident response time or, better yet, preventing failures, allowing crossings to operate as usual. This approach involves more flexible digital measures to avoid the billions of dollars in damage that could result from traffic delays, as FHWA estimates.
Although the human factor remains the primary cause of collisions, its crucial to pay attention to equipment’s failures. These failures can often lead to violations by drivers. Firstly, the failure of the level crossing misinforms drivers, when the gate gets stuck in the open or closed state, or remaining half-open. Secondly, level crossing equipment may operate incorrectly, open or close too early or too late, which also provokes drivers to commit violations, such as driving while the gate is closing or driving around a closed gate. Moreover, the likelihood of violations increases as congestion develops at the level crossing.
By ensuring the smooth operation of level crossings, we can significantly reduce incidents by changing how we maintain assets.
As we can see, level crossings are very sensitive assets. Therefore, digital measures need to be managed carefully, involving the most flexible and modular solutions for performing maintenance. The timely identification and prediction of equipment failures, as well as the competent organization of the railroad maintenance process, are critical for keeping crossings functioning. Thus, digital solutions should contribute to effective time and resource management, and be cost-effective and drastic enough to comply with strict industry standards.
How to Approach IoT for Railroad Maintenance at Level Crossings
The most comprehensive and balanced solutions to address the level crossing challenges relate to the Internet of Things (IoT). All the components of the IoT ecosystem work successfully separately, but together they bring perceived economic value to the crossing maintenance. This essentially modular system allows for creating end-to-end solutions that link all assets, and maintenance operations, providing tracking of the status of equipment and relationships between operations in real time. Configured for use in a specific rail area, IoT-based solutions involve the following features vital to reduce incident response time:
- Instant reporting of incidents
- Providing necessary information to all responsible participants
- Detailed incident analytics and prevention strategy
- Service automation
These key features are expected to form the near future of railroad maintenance addressing the challenges described above.
IoT-based Real-Time Monitoring
Smart sensors are installed into the crossing gate mechanism to continuously monitor various parameters related to the equipment performance and quickly transmit data to a central server. By monitoring current, voltage, gate position, and type-specific parameters, such as hydraulic characteristics, the solution instantly reports when the indicators deviate from the normal, that is, a failure occurs. By ensuring compatibility with various types of gates, service companies and rail authorities are able to provide real-time monitoring of the entire responsible area. This component alone already provides critical information for effective railroad maintenance, and the next key is to leverage this information in an optimal way.
Thanks to cloud deployment, information on crossing status can be accessed from anywhere and transmitted instantly to the respective personnel. Cloud-based IoT platforms provide an opportunity to consider the scale of the solution at the first stage of application deployment. That is, as more level crossings are equipped with real-time monitoring devices, they can easily be connected to the application, and be seamlessly included in the permanent monitoring process.
Automation of Task Assignment
Automatic task assignment functionality reduces operation time and the number of actions required to perform railroad maintenance. A cloud-based IoT solution allows for real-time notification and distribution of the necessary information to the right place – to the control room and to the maintainer’s device.
To achieve a truly visible effect, the rail industry will have to deviate from its usual conservatism and introduce a fairly high level of task automation. For example, to trust the system sending messages to designated maintainers and provide them with access to all necessary information online before going on site. This allows them to study the issue in advance and be fully equipped for repair, which also considerably reduces time.
Predictive Сapabilities for Railroad Maintenance
With such a huge amount of data that IoT solutions generate every moment, it is natural to start tracking patterns that lead to equipment failure. For example, changes in the position of the gate detect an approaching malfunction. By knowing this, rail companies can plan railroad maintenance in advance according to the needs of a specific asset, and always have a spare detail on hand. This is how neural networks containing predictive analytics algorithms influence a whole range of maintenance-related procedures, significantly reducing the time and resources required for it. With an IoT-based solution in place, creating a predictive model is not a big deal, since it generates a vast amount of highly accurate data for modeling purposes. Once trained, the model serves the maintenance needs faithfully, only cultivating itself over time.
Although predictive maintenance is gaining momentum in rail now, it still cannot be called a widespread and especially prevailing practice. However, time works in the favor of railways, since as IoT and neural networks develop, becoming more and more affordable. For example, we can already talk about the substantial financial benefits of the implementation of AI in the field of visual inspection. As for rail, If we compare the costs associated with transport delays with the cost of implementation of a smart solution, then even the primary calculations show the value of the latter.
Multi-level Access for Service Firms and Rail Authorities
A crucial benefit unlocked by IoT-based solutions that neither maintenance organizations nor railway authorities should miss is transparency. We are talking about complete real-time and historical information about the state of assets and activities performed. Multi-level access for dispatchers, supervisors, maintainers, and authority representatives allows them to be fully informed about the level crossing condition and respond promptly according to their job description. This approach also significantly increases safety and eliminates controversial issues during incident investigations.
Sum up: IoT-enabled Railroad Maintenance as a Guarantor of Safety & Performance of Level Crossings
- To prevent crossings from becoming the bottleneck of the transport network of the future, it would be worthwhile to take care of improving their railroad maintenance strategy for now.
- IoT-enabled level crossing monitoring solution provides the highest result for enhancing safety and performance at level crossings thanks to real-time failure detection, cloud deployment, and predictive capabilities.
- Incident response time is reduced through prompt informing on failures detected by smart sensors and provision of all the critical data to responsible staff in real-time.
- Neural networks trained on IoT data collected from level crossings ensure the detection of 90%+ upcoming failures, which allows for planning only required maintenance in advance.
This is not far but a tangible future for rail – safe, accurate, and efficient.
Article by Julia Seredovich, Business Operations Manager at Professional Software Associates Inc. (PSA). Thriving at the junction of railway signalling and the Industrial Internet of Things (IIoT) inside PSA, Julia specializes in building client solutions that bring together signalling technologies and overall business objectives. A liaison to PSA’s invaluable technical engineering team, she provides companies with expertise in the signal design of electrical interlocking, microprocessors and relay-processor systems.