Breakthrough in Real-Time Multimodal Tactile Technology
A tactile perception system capable of providing human-like multimodal tactile information to objects like robots and wearable devices that require tactile data in real time has been developed.
The research team led by Research Director Hyuneui Lim of the Nano-Convergence Manufacturing Systems Research Division and Principle Researcher Youngdo Jung of the Department of Nature-Inspired System and Application of the Korea Institute of Machinery and Materials (Chairman Seog-hyeon Ryu, hereinafter referred to as the “KIMM”), an institute under the jurisdiction of the Ministry of Science and ICT, developed a real-time and multimodal tactile perception system capable of providing multi-tactile information in real time inspired by human tactile perception, and announced the outcome of the research in the renowned journal “Soft Robotics.” (IF: 7.9)
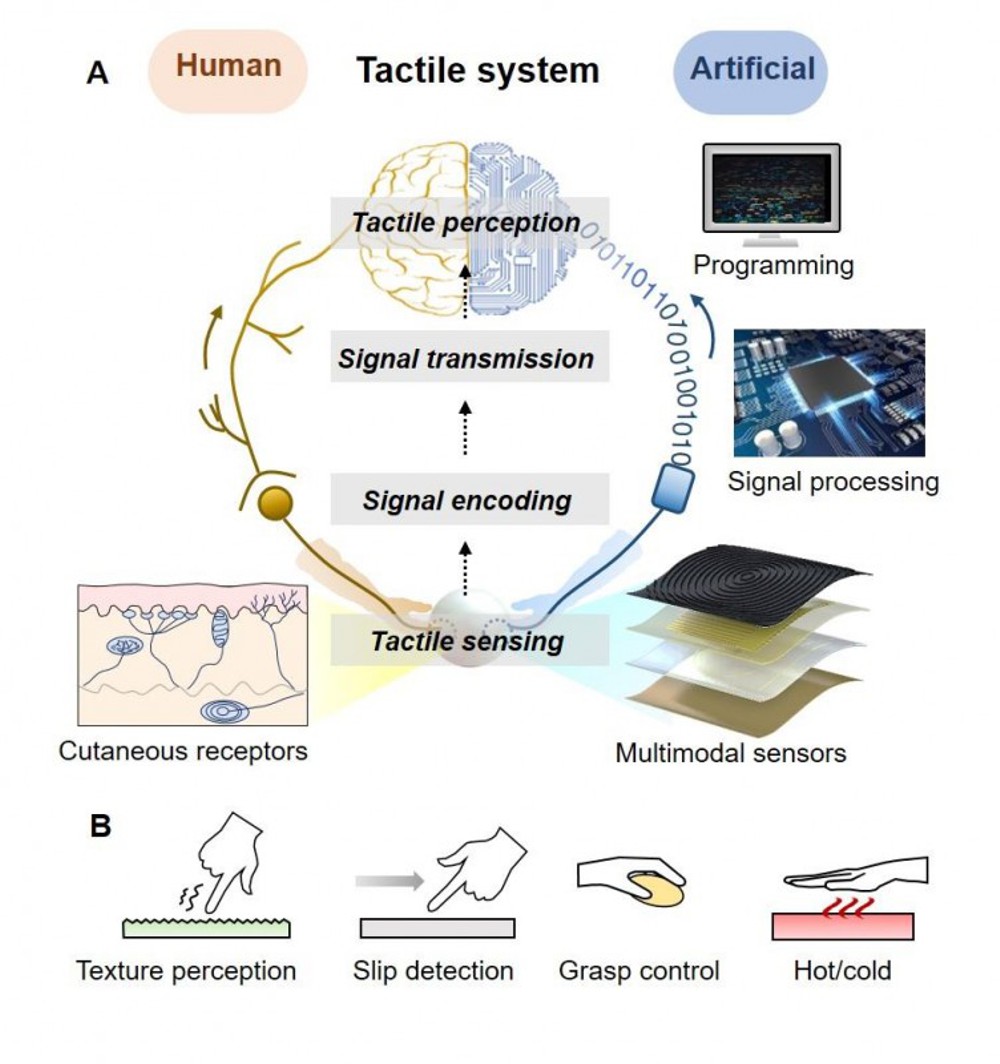
The research team developed a real-time and multimodal tactile detection system, by mimicking the principle by which various types of tactile information is perceived by a variety of sensory receptors in the human skin and is transmitted to the brain in real time. This system consists of four three-dimensionally stacked tactile sensors, a signal processing/transmission module, and an analysis module. The system has successfully distinguished various types of tactile stimuli and surface textures and furthermore differentiated complex motion in real time.
Four types of tactile sensors, each of which detects temperature, vibration, shear force, and vertical pressure, are laminated in a three-dimensional structure based on three-dimensional (3D) flexible electrode printing process technology. At the same time, these sensors are connected to the FPCB (Flexible Printed Circuit Board) of the electronic module for signal processing and transmission, thereby easily transmitting signal-processed tactile information through the corresponding FPCB connection terminal.
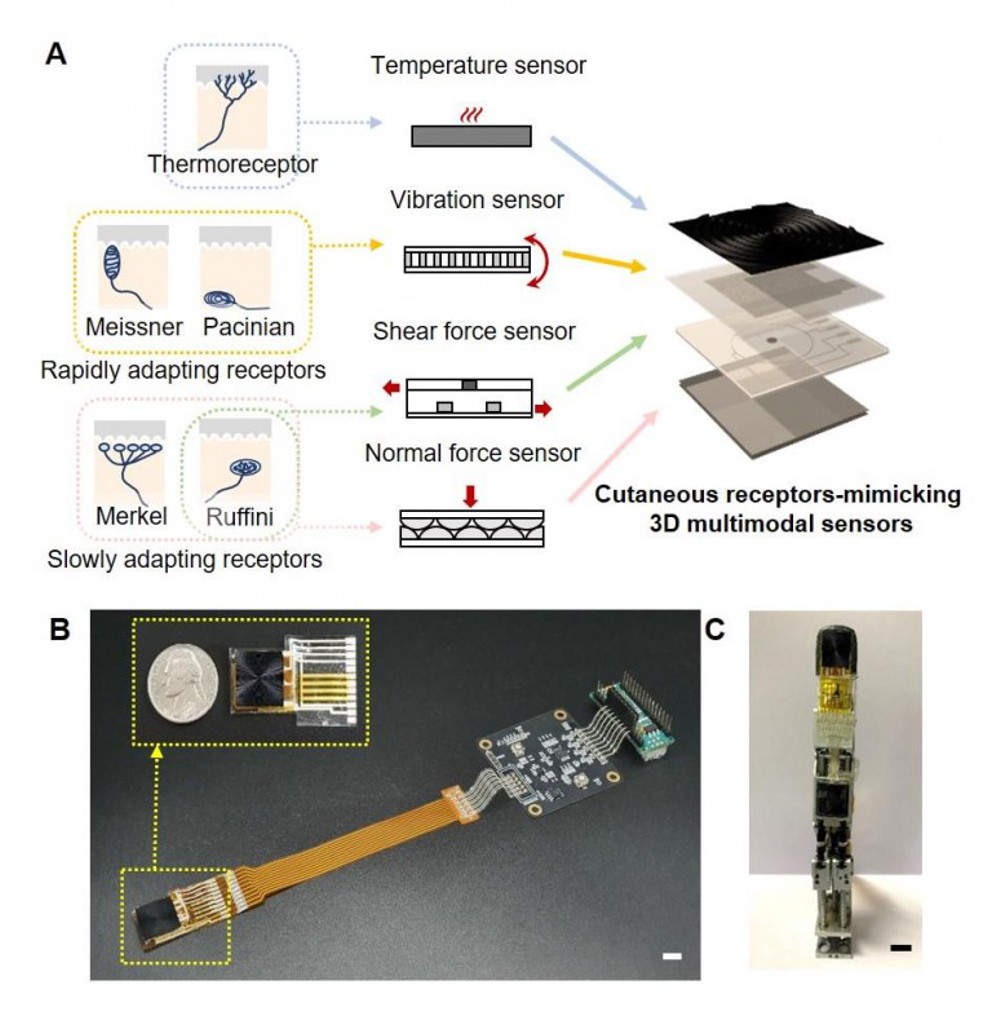
In previous studies, complex external measuring devices and analysis equipment were needed in order to detect the signals generated from the corresponding device so that various forms of tactile stimuli could be detected. Therefore, it was difficult to apply these devices to wearable devices or robots in the form of a simple stand-alone system.
On the other hand, in the newly developed multimodal tactile perception system, multiple types of tactile sensors are arranged vertically in a three-dimensional structure. Additionally, a module capable of converting, transmitting, and analysing the signals has also been developed, which allows for the system to be implemented in a compact and simple form and makes it applicable to actual robots and wearable devices.
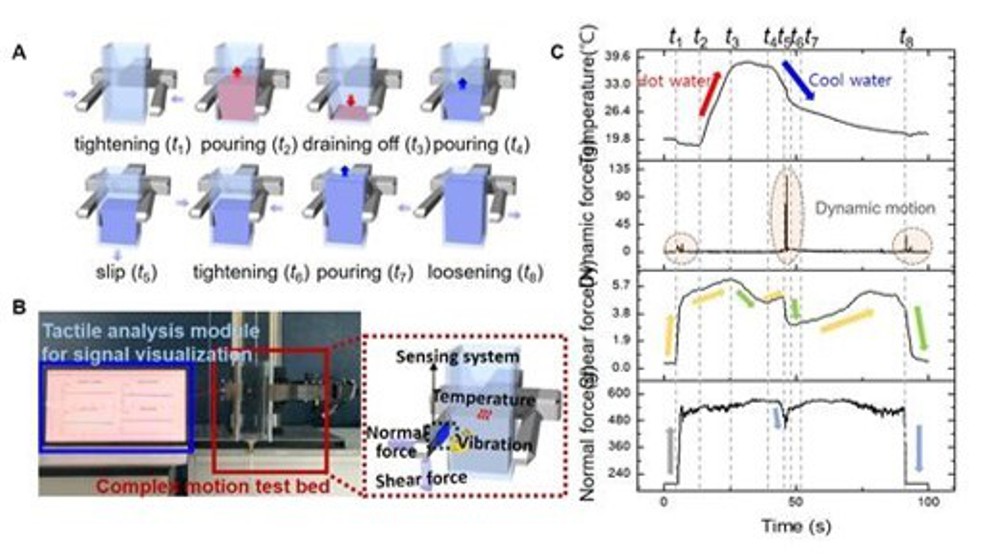
Research Director Hyuneui Lim of the KIMM was quoted as saying: “By mimicking the sensory system of humans, the real-time multimodal tactile perception system is capable of perceiving multiple senses simultaneously. Moreover, it is a technology that has solved the problems that may be caused by complex and large signal processing and detection systems when using conventional sensors.” She added: “By applying this system to robots or wearable devices, we will be able to obtain a large volume of diverse and complex tactile signal information, which will hopefully contribute to the improvement of public welfare and security.”
Meanwhile, this research was supported by the Convergence Technology Development Program for Bionic Arm through the National Research Foundation(NRF) of Korea funded by the Ministry of Science &ICT(2014M3C1B2048177), and the Basic Research Program of KIMM (No. NK242C), Republic of Korea.
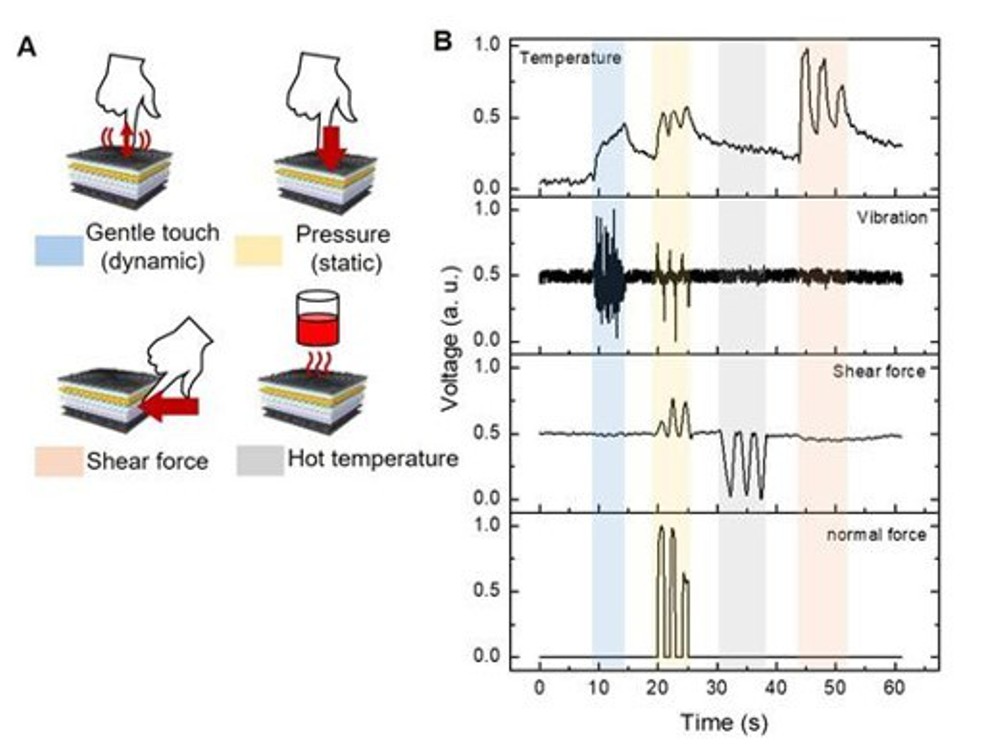