Revamping and widening the winding roads of south-eastern Ohio
Some of the most dangerous roadways in the country include bustling highways, high-speed interstates and tricky intersections. But unexpected danger lies beyond big city distractions and high-traffic roads, where the hazards relate to nature more than other vehicles.
The roads of south-eastern Ohio wind around the hills, resulting in sharp turns and corners. While an average vehicle doesn’t have an issue navigating them, the same cannot be said for large trucks and trailers. The turning radius on oversized, multiple-axle vehicles like oil and gas trucks doesn’t mix well with the curvy roads, causing them to frequently end up with their wheels in the ditch. Over time, this repetition causes dangerous drop-offs on the outside corner of the paved roads.
This is not a new issue for the Ohio Department of Transportation (ODOT). To address it, they constantly seek out new approaches and solutions to increase safety on the state’s roadways, with a goal to virtually eliminate crashes and injuries altogether.
A Temporary Fix
To combat the dangerous situation of the winding roads, ODOT first attempted to stabilize the shoulder with aggregate material. Using a road grader and a dump truck, crews laid the aggregate and pushed it off to the shoulder. From there, they compacted the aggregate, creating what seemed like an effective solution.
However, this approach only worked temporarily and presented a maintenance issue. The lack of moisture in aggregate made it less than ideal for a permanent roadway. Crews found that after a heavy rain, the material washed away and exposed the original dangerous drop-offs. At least once a year, crews had to revisit the eroding berms and repeat the placement process.
After testing several compaction methods, they opted to evolve to a new approach. With a stickier, denser substance, ODOT could create a longer-lasting solution for roadway maintenance.
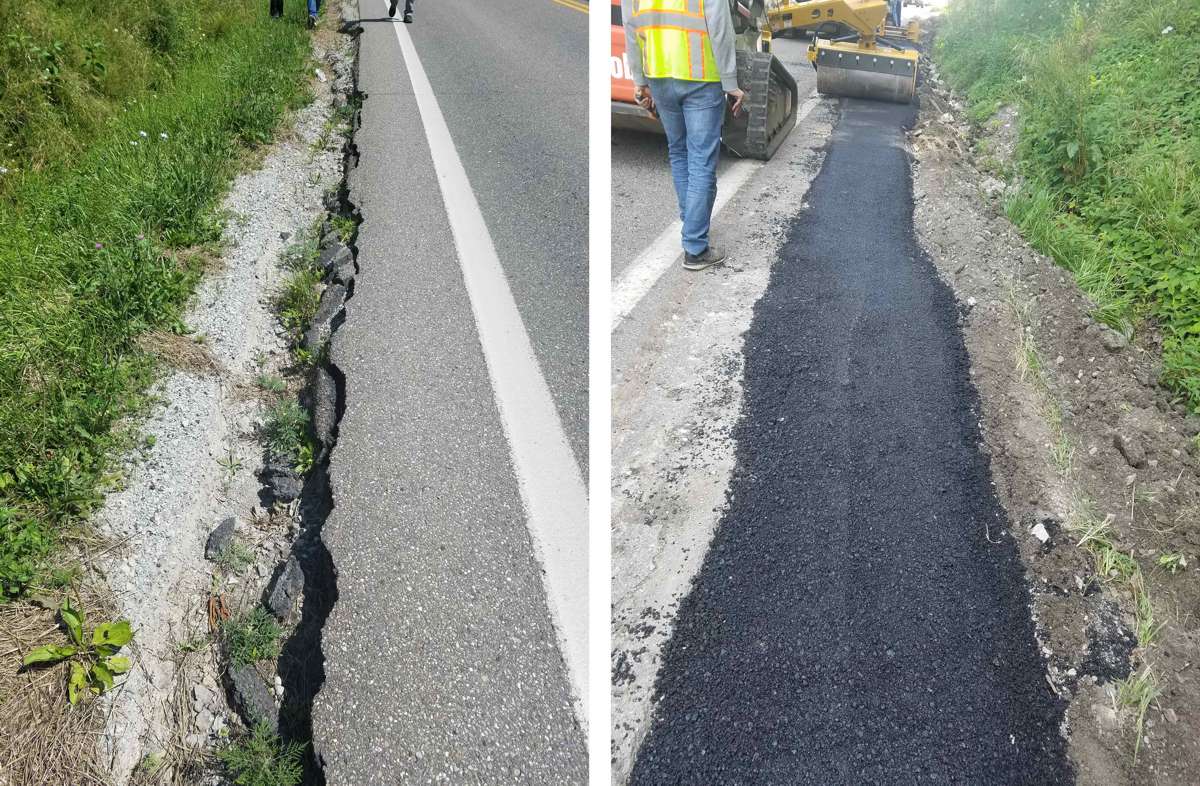
Getting Results with Safe Compaction
Using asphalt might seem like a no-brainer, but the application involves a much more intricate — and expensive — process. Traditionally, widening a road with compacted material involves a four-step process: lay the material, use a blade to move the material into place, compact the material with the tires of a dump truck, and finally broom, sweep and clean up. Though it is a common process, ODOT was interested in limiting the number of steps in their approach. Their solution came from one of its own highway workers.
“One of my highway technicians presented the idea of an offset road widening attachment,” said Rick Venham, transportation administrator of Washington County in Ohio’s District 10. “The guys who work on the projects and actually operate the equipment bring the best ideas and this case was no different.”
Road teams attach the equipment to a host machine, such as a skid steer, compact track loader, loader or grader to disperse gravel, asphalt and topsoil. Using it results in increased efficiency, reduced labour and decreased costs — benefits that stood out to ODOT.
Because the attachment is smaller than traditional road widening products, it is much more cost effective and offers higher efficiency and manoeuvrability. This combination of benefits significantly impacted ODOT’s decision-making process, as they were searching for a solution that offered ease of use with a low cost-per-ton ratio when laying asphalt.
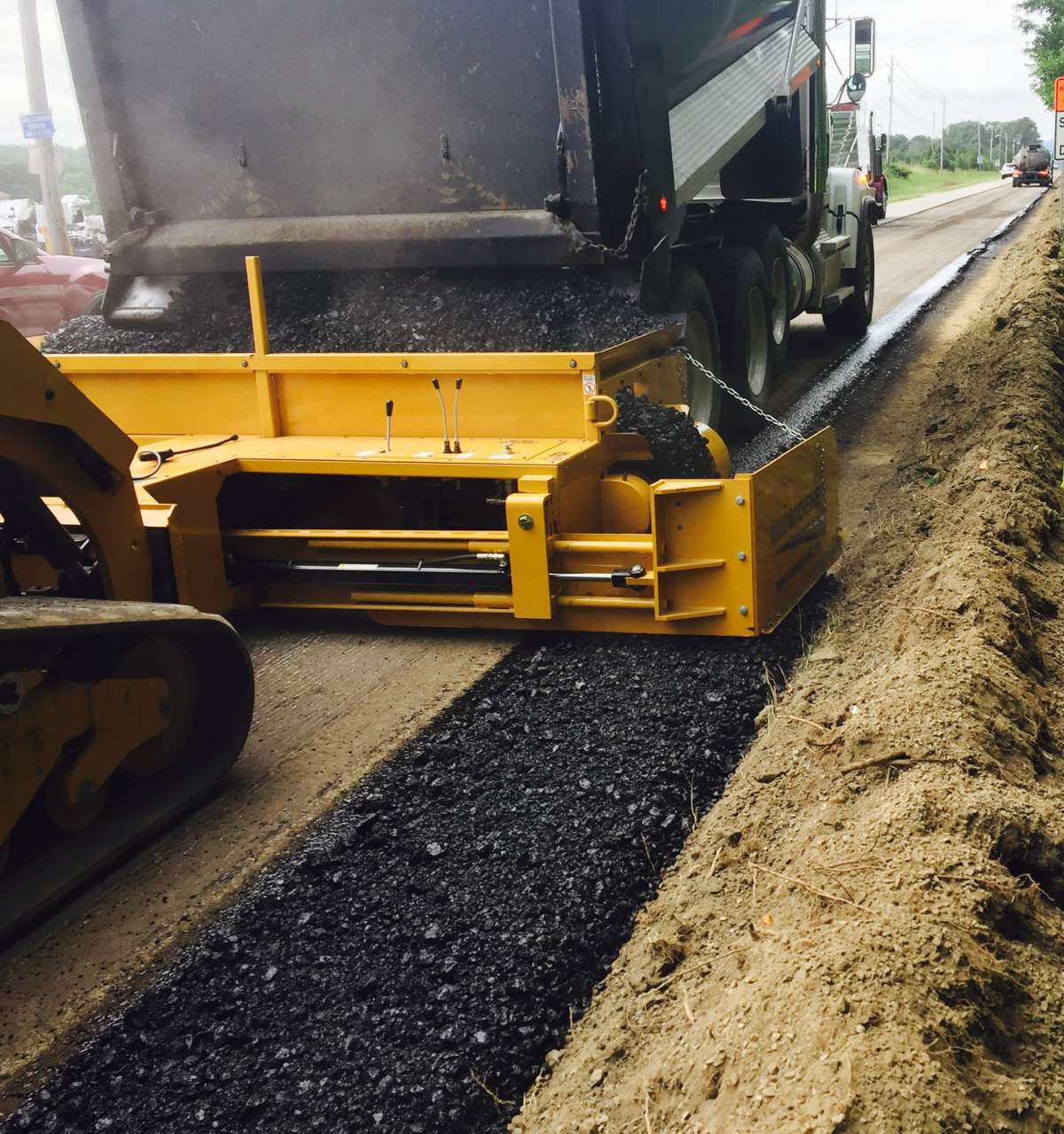
The Ideal Operation
The skid steer attachment works by dispersing material from a dump truck to the material box, and then carefully onto the roadway. The equipment offers a unique dual discharge, enhancing the versatility and making it easy to disperse the material from either side. One or two people can operate it, thanks to the remote-control of the belt speed.
Another benefit of the equipment is its transportability. Because of its compact size, the attachment and host machine can fit on the same common-sized trailer. Larger, more cumbersome alternatives require a flatbed trailer.
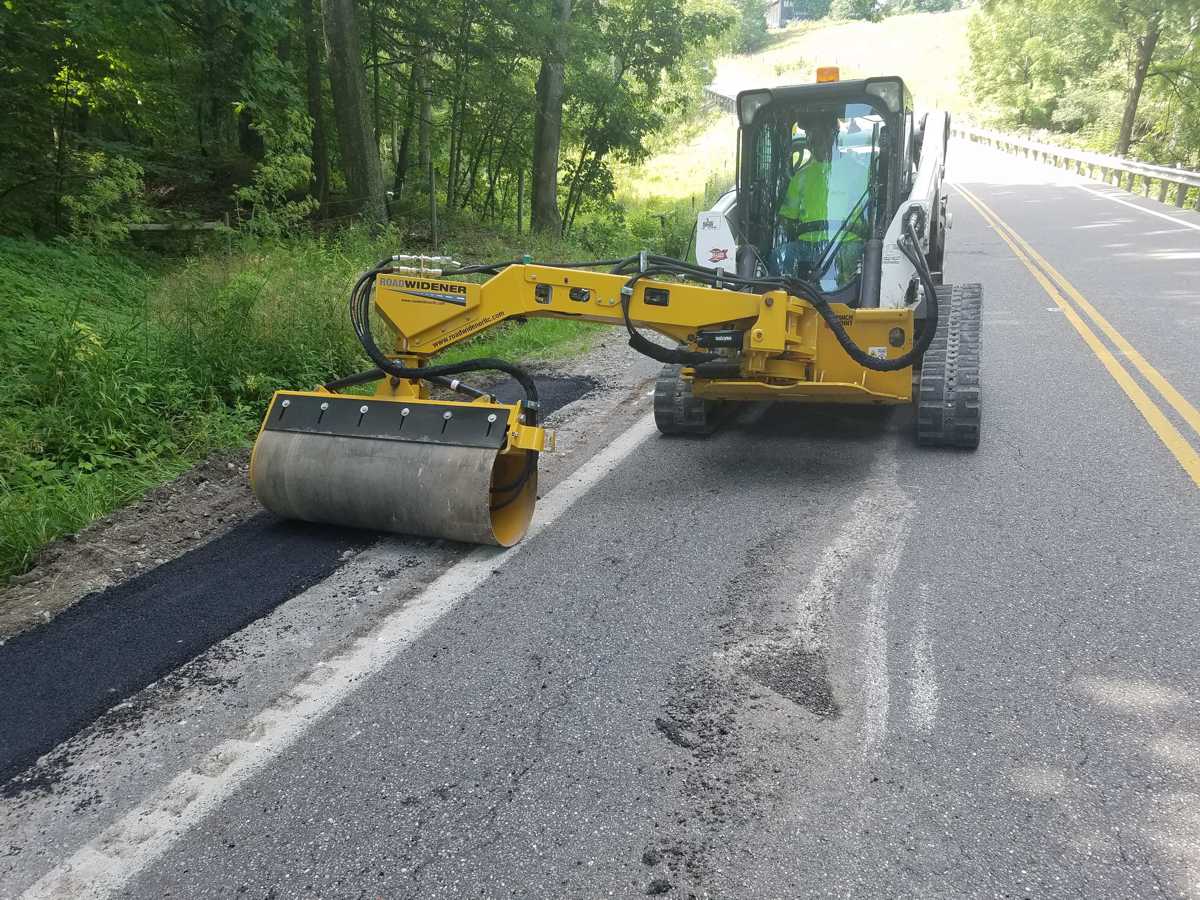
Proof in the Results
The attachment was also used during a recent Federal Highway Association (FHA)-sponsored study. In early 2020, the FHA partnered with Ohio University (OU) on a research project to evaluate ODOT’s berm construction and repair process in Monroe County. Through two phases, OU evaluated and provided recommendations to improve the safety, productivity and cost-effectiveness of the process. They analysed both material and equipment in the study.
Phase 1 confirmed the main cause of the frequent berm repair is the erosion of berm materials due to the high stress applied by oil and gas trucks. Additionally, it identified equipment and materials that could help improve the berm resistance to erosion.
Phase 2 of the study examined the berm performance and service life when using different alternative methods. The results reiterated what ODOT had observed: the best results came from heated reclaimed asphalt pavement (RAP).
The study not only indicated that these materials significantly improved the service life of berms, it also resulted in significantly reducing the annual cost of berms. The highest cost benefits were obtained when heated RAP or emulsified RAP materials were used as shoulder materials. According to the report, the results indicated that the alternative materials and equipment can reduce the average annual cost of repairing routes with heavy truck traffic by up to 60%.
OU took advantage of the road-widening skid steer attachment as one of the application methods for the RAP evaluation. The university also purchased a 4-foot offset vibratory roller to test the compaction process. The offset roller attaches to a skid steer to compact the placed berm materials. The patented design allows the operator’s machine to remain on a flat surface while compacting shoulders and ditches. This provides a safer option than many alternatives, as shoulder compaction rollovers are a significant risk.
According to the study, using a berm box to spread and place berm materials, as well as using a offset vibratory roller to compact the materials, resulted in a slightly higher cost than previous methods, but they helped to significantly improve the safety and efficiency of berm compaction. The combination of the two pieces of equipment also increased the resistance of the berm materials to erosion and rutting.
The study results stated that alternative berm materials and methods can reduce the time that ODOT personnel need to be in the field for repairing berms on state routes by up to 95%.
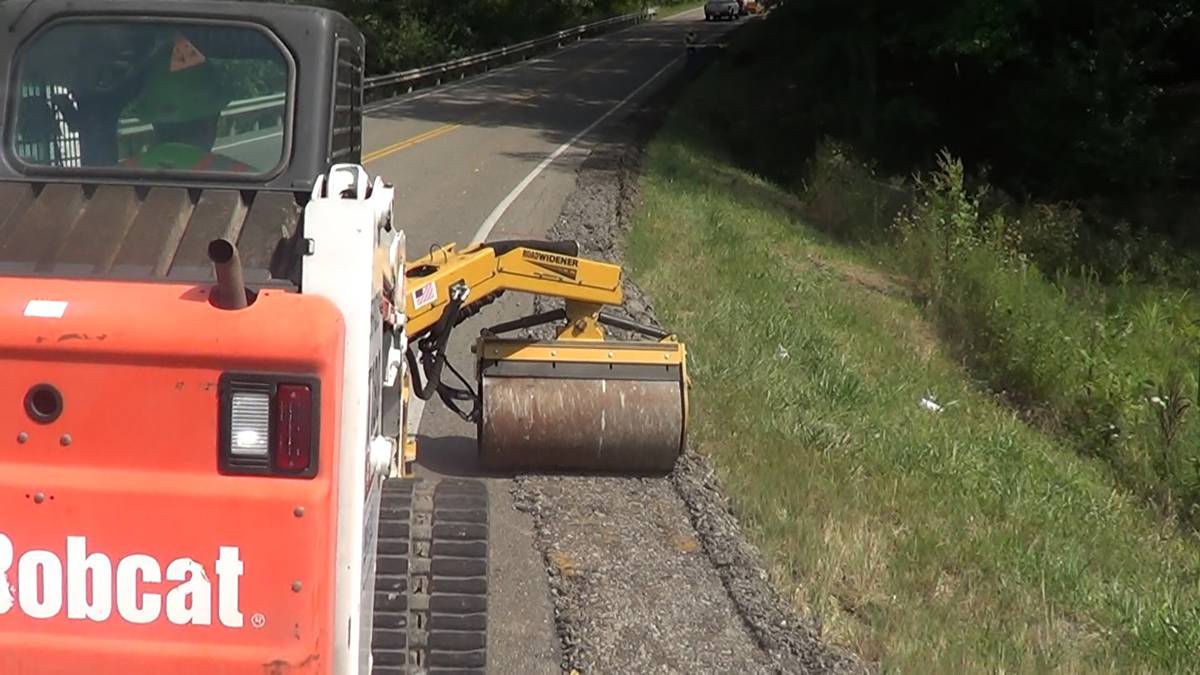
Lasting Success
Efficiently widening roads comes with a series of benefits, the most notable of which is safety. ODOT uses the road-widening skid steer attachment two to three months a year. Their operating costs are low, the labour cost is manageable and the results are substantial. During peak season, they average 500-600 tons of asphalt per day, depending on the route. That equates to about 5-6 miles of roadway getting a safety boost every day. For Monroe County alone, they laid about 6,500 tons of asphalt with this new application method.
“We were stuck using a grader and loaders,” District 10 equipment manager Jim Kemp said. “It was time consuming and, more importantly, it’s inconsistent. Using this two-step application method for road widening allows our teams to put materials exactly where we need them. It also gives us the option to use aggregate or asphalt, so we can use the same equipment for the initial layer of aggregate and follow up with the lasting layer of asphalt.”
Brian Shields, transportation administrator of Monroe County in District 10, agreed. “Once we get a wider road in place, it’s a forever solution,” Shields said. “I’ve done road widening for years and this new method helps to ensure it stays in place. It has held up for at least five years, and I’m sure it will last much longer than that.”
ODOT is making its way through all the dangerous roadways of Ohio. Their ongoing goal is to reduce the number of vehicle injury incidents in accident-prone areas. And while this two-step method saves them money and improves efficiency, the ultimate goal of increased safety has no price tag.