Stratasys unveils High-Precision 3D Printing Solution for Low-Volume Manufacturing
As the manufacturing landscape evolves, companies are increasingly turning to additive manufacturing to meet the demands of low-volume, high-precision production. Stratasys, a leader in 3D printing technology, has introduced a breakthrough solution with the Origin® Two DLP printer and its complementary post-processing system, the Origin Cure™.
This new offering promises to redefine the standards of accuracy, repeatability, and surface finish, rivalling traditional injection-moulding techniques.
Meeting Modern Manufacturing Challenges Head-On
The manufacturing world has been grappling with numerous challenges—from supply chain disruptions to the rising costs of materials. Traditional high-volume manufacturing methods, while efficient for large-scale production, are often not cost-effective for shorter runs or custom parts. The Origin Two seeks to fill this gap, offering manufacturers a flexible, high-precision alternative that doesn’t compromise on quality.
Precision Without the Hassle
The Origin Two and Origin Cure are specifically designed to cater to manufacturers looking for a balance between quality and flexibility. With a stunning accuracy of +/- 50 µm and a surface finish comparable to injection-moulding, this printer sets a new standard for additive manufacturing. Stratasys’ advanced DLP technology ensures that each part meets stringent quality controls, which is critical for industries such as aerospace, automotive, and consumer products.
Rani Hagag, Chief Healthcare and Consumer Business Officer at Stratasys, emphasises the transformative potential of the new system: “Additive manufacturing has grown to be a critical component of production at any scale on the manufacturing floor. With the new Origin® solution, manufacturers in need of low volume, high precision parts now have an alternative to mass production that can meet their most stringent requirements, something which was not possible with additive before.”
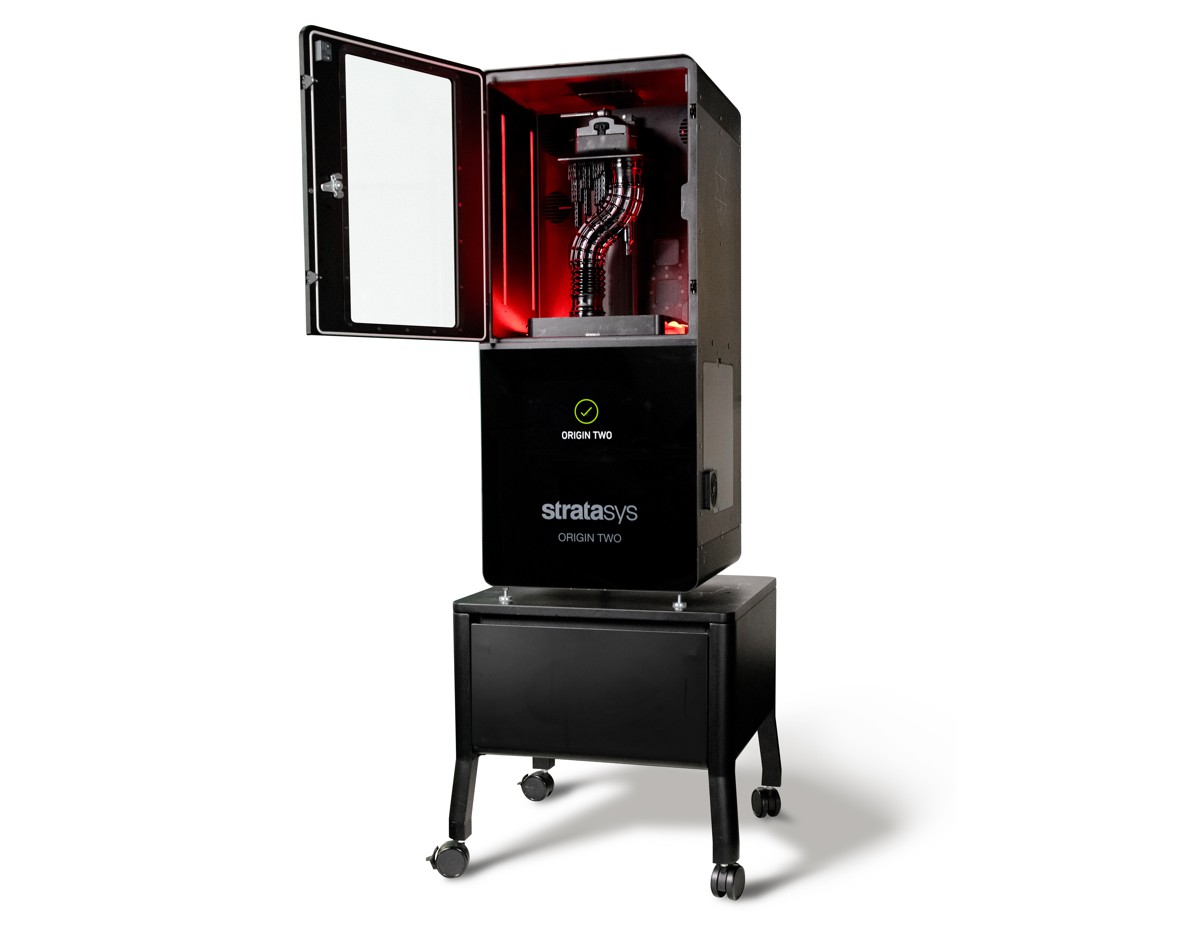
Key Features That Set the Origin Two Apart
The Origin Two printer, when paired with the Origin Cure, provides a comprehensive solution that addresses some of the key pain points in modern manufacturing. It’s not just about printing parts; it’s about enhancing the entire production process. Here’s a closer look at what makes this new system a game-changer:
- Exceptional Accuracy and Repeatability: Achieves a repeatability of more than 93% within +/- 50 µm across multiple printers, maintaining high print speeds up to 20 mm/hour. This ensures consistent quality, even in complex geometries.
- Versatile Material Compatibility: Running on a 385-nanometer wavelength, the printer supports a wide range of high-performance materials, including high-temperature resins and high-viscosity formulations. This makes it suitable for demanding applications such as seals, gaskets, and electronic housings.
- Heated Chamber Technology: The heated chamber of the Origin Two enables reliable printing of materials with a Heat Deflection Temperature (HDT) of up to 300°C, expanding the range of possible applications to include high-performance and heat-resistant components.
- Integrated Quality Control: The system’s design allows manufacturers to bring production in-house, reducing reliance on third-party suppliers and improving inventory management. With on-demand production capabilities, companies can significantly cut down on warehousing costs and lead times.
Bridging the Gap Between Prototyping and Production
Traditional 3D printing has often been confined to the realm of prototyping, but Stratasys is pushing beyond those limits. The Origin Two’s ability to produce parts that match the precision and surface finish of injection-moulded components means it’s perfectly positioned for short-run production, where set-up and tooling costs can be prohibitively high.
Ryan Martin, Senior Research Director at ABI Research, notes the growing value of additive manufacturing in this space: “Additive manufacturing is becoming increasingly valuable for low production volumes in the manufacturing sector. Manufacturers are using 3D printing for low-volume and custom parts, which helps reduce lead times and waste. This allows for greater flexibility and cost efficiency, supporting both prototyping and on-demand production.”
With these capabilities, the Origin Two allows manufacturers to consolidate part manufacturing into a single streamlined process, enhancing consistency and reducing the potential for errors. It’s a shift that not only speeds up production but also lowers costs, making high-quality manufacturing more accessible than ever.
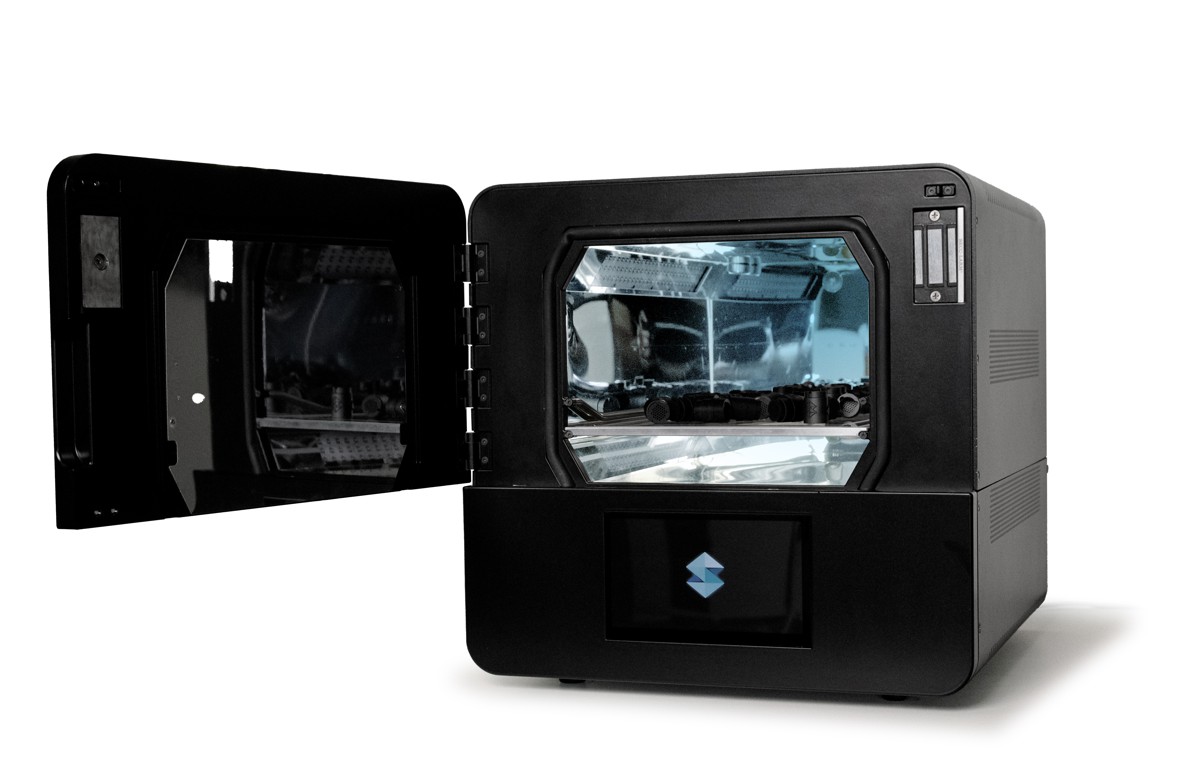
Where to See the Origin Two in Action
For those eager to see the Origin Two and Origin Cure in action, Stratasys will be showcasing this new technology at the International Manufacturing Technology Show (IMTS) in Chicago, from September 9 to 14. The systems are available for purchase from September 5, marking a significant step forward for additive manufacturing in the global market.
Stratasys: Leading the Additive Manufacturing Revolution
Stratasys has long been at the forefront of 3D printing innovation, and the Origin Two is a clear testament to the company’s commitment to pushing the boundaries of what’s possible. With advanced 3D printers, versatile polymer materials, and a comprehensive software ecosystem, Stratasys is equipping manufacturers with the tools they need to transform their production processes.
The Origin Two and Origin Cure are more than just products; they represent a shift towards smarter, more adaptable manufacturing that meets the evolving needs of today’s market. By offering high precision at lower volumes, Stratasys is enabling manufacturers to take control of their production lines, reduce waste, and deliver high-quality products faster than ever before.