Mercedes-Benz Leads the Charge with New Battery Recycling Facility in Germany
Mercedes-Benz has just taken a giant leap towards a greener future. In a bold move, the automotive giant has opened Europe’s first battery recycling facility in Kuppenheim, Germany, setting the pace for an environmentally conscious circular economy.
This revolutionary plant, designed with a unique mechanical-hydrometallurgical process, marks a pivotal moment in the electric vehicle (EV) industry. As the demand for electric cars surges, ensuring the sustainability of their battery production is critical. Mercedes-Benz is addressing this head-on, establishing a self-sustaining loop that not only recycles but also reuses critical raw materials for future batteries.
A Game-Changer for Electric Mobility
Mercedes-Benz’s new plant is the first of its kind in Europe, offering a fully integrated recycling process. This innovation enables the recovery of over 96% of valuable battery materials such as lithium, cobalt, and nickel. This milestone ensures that these materials can be reintegrated into the production of new battery modules, reinforcing the sustainability of Mercedes-Benz’s electric vehicles.
“We’ve set our sights on building the most desirable cars in a sustainable way,” said Ola Källenius, Chairman of the Board of Management of Mercedes-Benz Group AG. “This recycling plant is a testament to our commitment to enhancing raw-materials sustainability and electric mobility in Europe.”
Indeed, the Kuppenheim facility is not just a feather in the cap for Mercedes-Benz but also a significant stride toward addressing the broader environmental concerns surrounding battery production. Traditional recycling methods, such as pyrometallurgy, are energy-intensive and less efficient. By contrast, the mechanical-hydrometallurgical process used at this plant consumes far less energy, operating at lower temperatures and resulting in minimal waste.
Investment in Sustainability
Mercedes-Benz has invested tens of millions of euros into the development of this state-of-the-art facility, solidifying Germany’s position as a leader in innovative technology for the electric vehicle industry. The factory will generate enough recycled materials to produce over 50,000 battery modules per year. These efforts underline the company’s holistic approach to battery circularity and its strong commitment to reducing reliance on primary resources.
Federal Chancellor Olaf Scholz, present at the plant’s grand opening, lauded Mercedes-Benz’s forward-thinking investment. “The future of the automobile is electric, and recycling is key to producing batteries in a sustainable manner. This facility not only fosters resource conservation but also boosts our nation’s technological leadership in green innovation,” Scholz commented.
This sentiment is echoed by Thekla Walker, Baden-Württemberg’s Environment Minister, who highlighted the importance of closing the value chain loop. “Mercedes-Benz’s approach to battery recycling helps reduce dependency on raw material imports and contributes to a resilient economy.”
Collaboration for Cutting-Edge Technology
Mercedes-Benz didn’t go it alone in this groundbreaking venture. The company partnered with Primobius, a joint venture between German engineering firm SMS Group and Australian process technology developer Neometals. This partnership brought together some of the best minds in battery technology to develop a recycling process that is not only efficient but scalable for future industry demands.
Moreover, the German Federal Ministry for Economic Affairs and Climate Action played a key role, funding research and development. This collaboration extends to several German universities, ensuring that the entire recycling process chain is examined, from logistics to reintegration concepts. The research aims to scale up the battery recycling industry across Germany and Europe, making it a crucial part of the green economy.
Integrated Recycling Process: A Technological Marvel
At the heart of Mercedes-Benz’s new facility is a process that breaks the mould. The recycling begins with shredding battery modules and then drying and processing the active materials found in the battery cells. From here, the hydrometallurgical process kicks in, where valuable metals like cobalt, nickel, and lithium are extracted through a multi-stage chemical process.
This is a far cry from traditional methods. Pyrometallurgy, still widely used in Europe, involves high-temperature smelting, which consumes vast amounts of energy. By contrast, Mercedes-Benz’s method operates at temperatures as low as 80°C, using 100% green electricity to power the plant. With solar panels installed on the roof of the 6,800-square-metre facility, the plant is also a shining example of carbon-neutral operations.
Scaling for the Future
With an initial capacity to recycle 2,500 tonnes of batteries annually, the Kuppenheim plant is set to provide critical insights for scaling battery recycling globally. Mercedes-Benz’s focus on “Design for Circularity” ensures that battery production for its electric vehicles is a closed-loop system, significantly reducing the need for new raw materials.
Jörg Burzer, Member of the Board of Management for Production, Quality & Supply Chain Management at Mercedes-Benz, sees the plant as a cornerstone of the company’s sustainability strategy. “This facility allows us to recover raw materials with the highest purity levels, essentially turning used batteries into a sustainable mine. It’s a monumental step for our production network in Europe,” Burzer noted.
Second Life for Batteries: Beyond the Car
Mercedes-Benz isn’t just thinking about recycling. They’re thinking long-term about how to extend the life of every battery produced. Through its subsidiary Mercedes-Benz Energy, the company is developing large-scale stationary energy storage systems. These systems give used vehicle batteries a second lease on life, offering a sustainable solution to energy storage demands.
This holistic approach is integral to the company’s long-term sustainability goals. Reconditioned batteries, available as spare parts for electric vehicles, further extend the use of these critical components. Additionally, local battery production across three continents ensures that the carbon footprint of manufacturing is as small as possible.
A Blueprint for the Future
Mercedes-Benz’s trailblazing efforts in battery recycling set a new benchmark for the automotive industry. Their investment in Kuppenheim is a clear signal to the world that sustainability and innovation go hand-in-hand. By partnering with industry experts, universities, and government bodies, Mercedes-Benz is positioning itself as a leader in sustainable electric mobility.
For the rest of the industry, the Kuppenheim facility is a shining example of what’s possible when companies commit to closing the materials loop. As the world moves further towards electrification, ensuring the sustainability of battery production is no longer a nice-to-have—it’s a necessity.
Paving the Way for Sustainable Innovation
The opening of Mercedes-Benz’s Kuppenheim plant is more than just an industry milestone; it’s a bold statement about the future of mobility. By embracing cutting-edge recycling technology, Mercedes-Benz is proving that luxury, sustainability, and innovation can coexist.
In the years to come, this facility will not only help meet the growing demand for electric vehicles but also reduce the environmental impact of their production—one battery at a time.
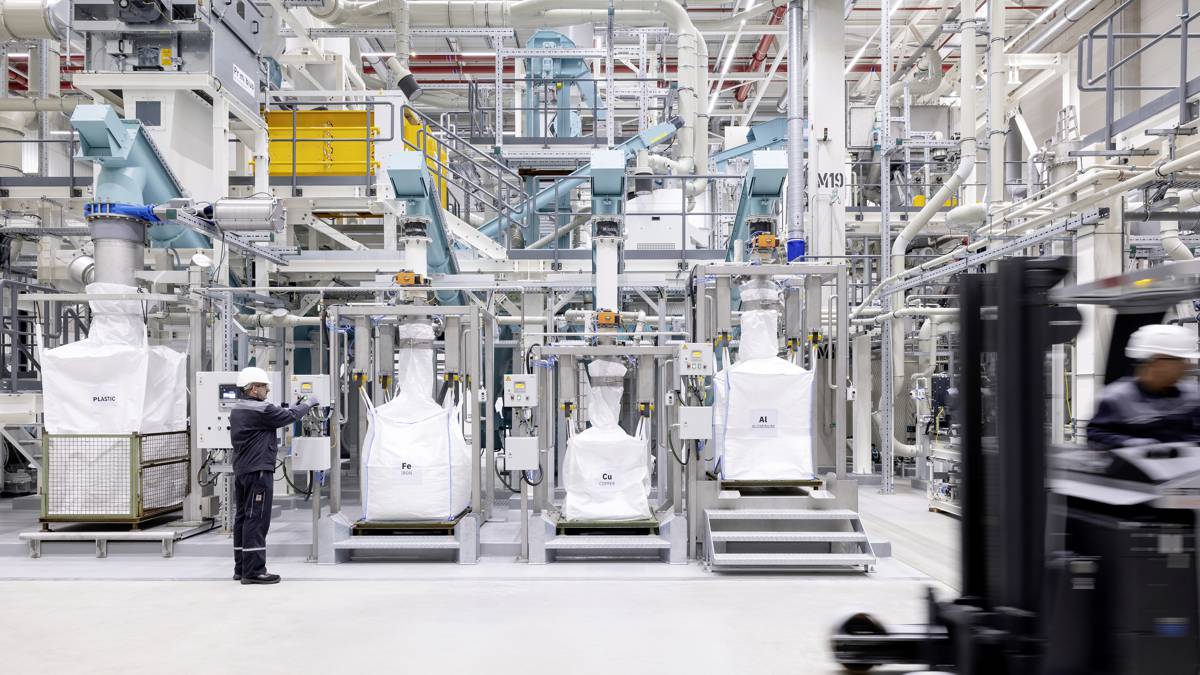