Rejuvenating Heavy Machinery for a Sustainable Construction Industry
In an era where sustainability isn’t just a buzzword but a necessity, industries are facing the challenge of balancing productivity with environmental responsibility.
Heidelberg Materials UK, a major supplier in the construction sector, is pioneering this shift by embracing innovative solutions that bridge the gap between existing diesel machinery and a zero-emissions future.
Through a collaborative partnership with Volvo dealer SMT, the company recently completed an ambitious equipment rebuild of a 14-year-old Volvo L350F wheeled loader. This project sheds light on how the construction industry can adopt sustainable practices by extending machinery lifespans and supporting a circular economy model.
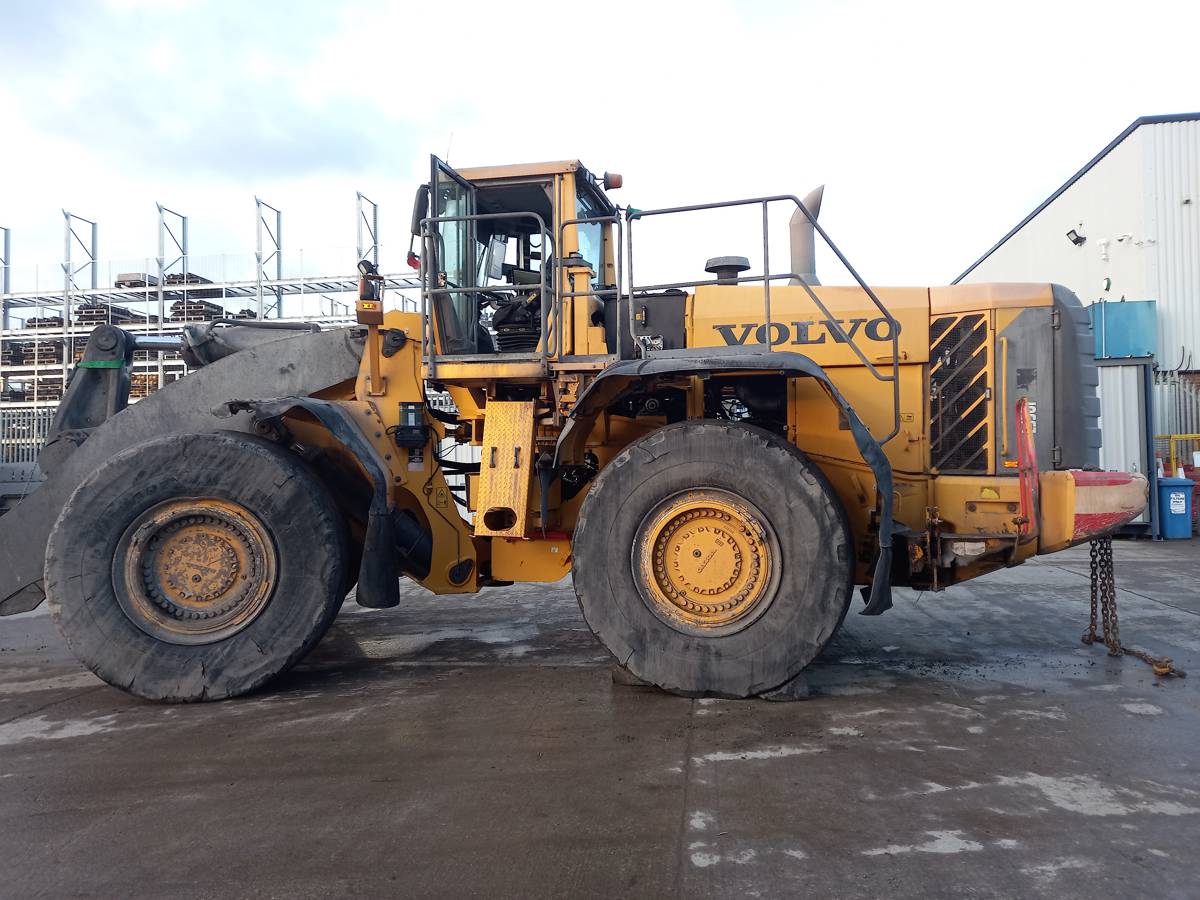
Why Rebuild Rather Than Replace?
Heidelberg Materials UK is no stranger to the environmental impact of its operations. As one of the largest suppliers of building materials, including cement—a significant contributor to global CO₂ emissions—the company has set ambitious targets to cut emissions by 15% by 2030 from a 2019 baseline. This goal, though primarily focused on cement production, also encompasses the heavy equipment used in their quarries.
To achieve these objectives, the company realised that rebuilding existing machinery, rather than purchasing new units, could be a strategic step. With years of useful life still left in their diesel-powered equipment, Heidelberg Materials saw an opportunity to refurbish these machines, thereby reducing the need for new manufacturing and its associated emissions.
- Lower Emissions: Refurbishing a machine’s engine can save up to 56% of CO₂ emissions, while rebuilding a transmission can cut emissions by around 60%.
- Material Efficiency: Rebuilding avoids the consumption of raw materials needed to produce new machinery.
Dominie Carver, strategic account manager at SMT, remarks: “Rebuilding existing machines is a sustainable practice. It not only extends machine life but also recycles major components, which significantly reduces carbon emissions.”
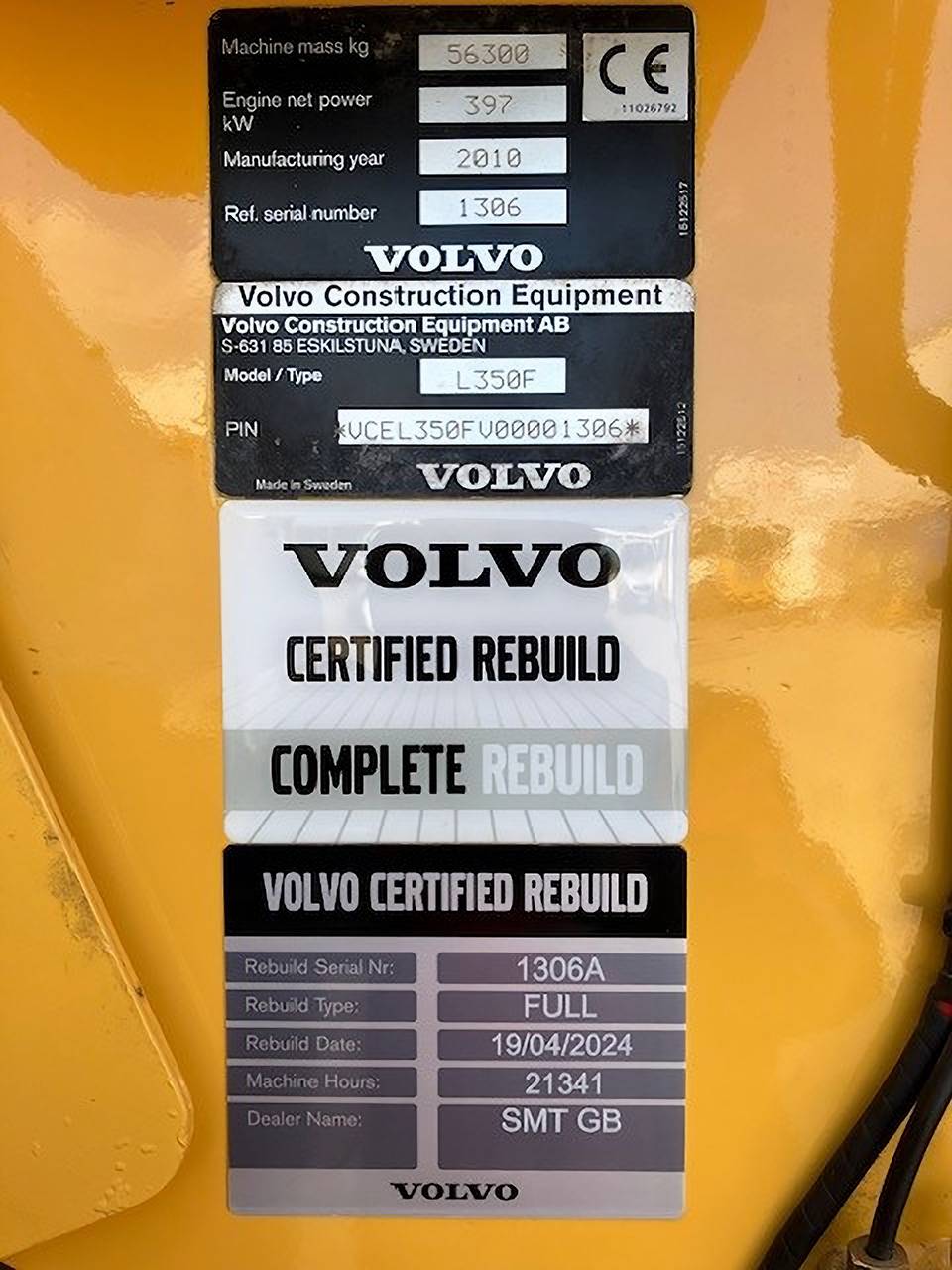
Rebuilding a Volvo L350F from the Ground Up
The centrepiece of this initiative is a 14-year-old Volvo L350F wheeled loader, clocking over 21,000 hours in service. Stationed at the Ribblesdale cement works in Clitheroe, this machine plays a critical role in loading limestone into crushers. Given its condition, Heidelberg Materials UK identified it as an ideal candidate for refurbishment.
The rebuild project, carried out at SMT’s Newcastle depot, was spearheaded by lead engineer Michael Christer and skilled welder Rhys Nixon. The process was meticulous, with the L350F dismantled down to its chassis to assess each component for wear and tear.
- Key Upgrades: New hydraulic pumps, hoses, and a complete steering system were fitted. The driveline components, including front and rear axles, transmission, and prop shafts, were also replaced.
- Structural Reinforcements: Full line boring was done, along with repairs to the load frame and bucket, which was outfitted with a strengthened cutting edge and wear plates to extend durability.
Beyond the technical upgrades, operator comfort wasn’t overlooked. The cab was given a facelift with a new seat, updated switchgear, and the installation of the Comfort Drive Control system, which reduces operator strain. As Andrew Graham, the loader operator, states: “Despite the sheer size and power of the L350F, it’s so easy to operate. It’s just like being in an armchair at home.”
Advantages of Refurbishing Over Buying New
Rebuilding a piece of heavy machinery offers several distinct advantages beyond environmental benefits.
Unlike purchasing new equipment, which often involves long lead times and adjustments to new machinery, rebuilding provides a faster solution. With a machine’s operational history on hand, companies can expect smoother transitions post-refurbishment.
- Consistency: The rebuilt machine retains its familiar controls and quirks, helping operators maintain productivity.
- Warranty Assurance: Using genuine Volvo parts, SMT ensures that each rebuild is backed by a 24-month warranty on major components, minimising downtime from unforeseen issues.
Luke Morgan, fleet manager at Heidelberg Materials UK, appreciates SMT’s structured approach, saying: “Our confidence in the success of the rebuild was due to SMT’s expertise and way of working. This partnership allows us to achieve our sustainability goals without compromising our operational needs.”
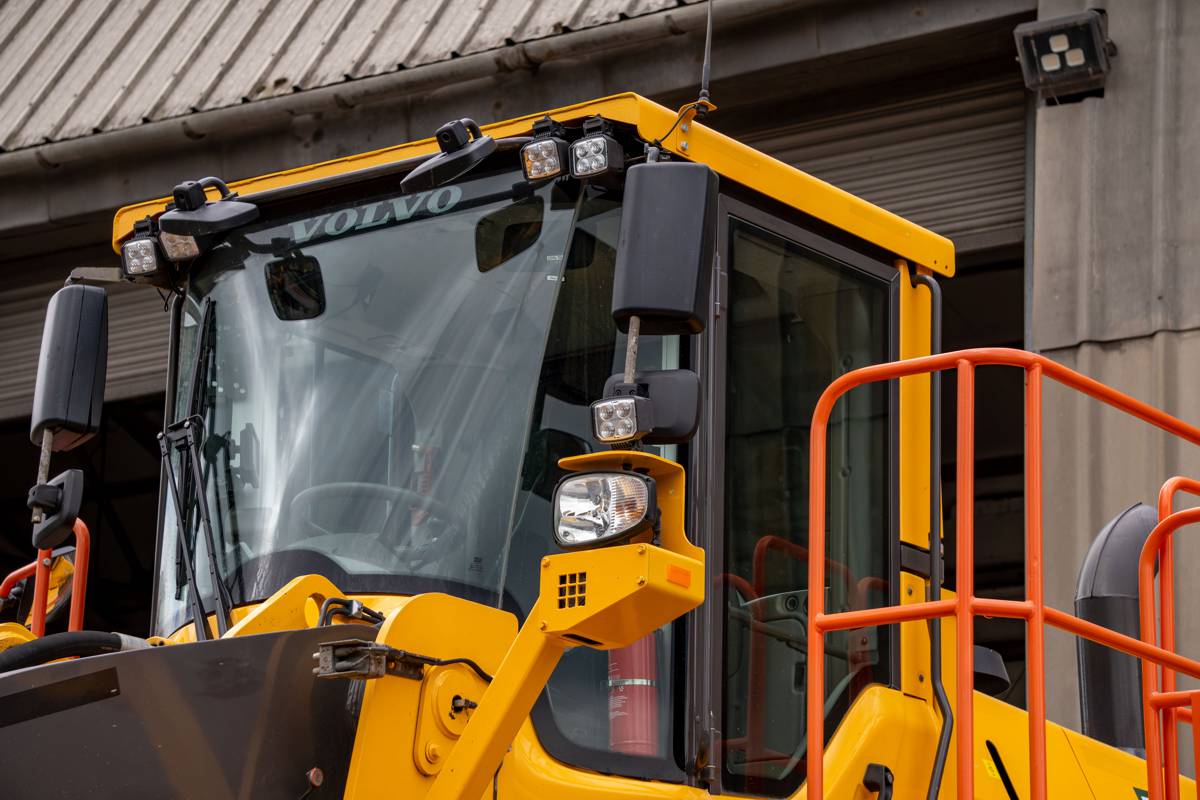
Paving the Way for Zero-Emission Fleets
While refurbishing diesel machines serves as an interim solution, Heidelberg Materials UK envisions a future fleet of zero-emission equipment powered by electricity or hydrogen. Achieving this goal, however, demands substantial infrastructure for renewable energy. Until then, the company sees rebuilding as a viable means to transition sustainably.
Elliot Wellbelove, carbon innovation manager at Heidelberg Materials UK, highlights the importance of partnerships in sustainability, explaining, “Collaboration with suppliers such as SMT is crucial for achieving Heidelberg Materials UK’s sustainability goals. We can rely on SMT to provide emissions reduction data, which is essential for calculating environmental benefits.”
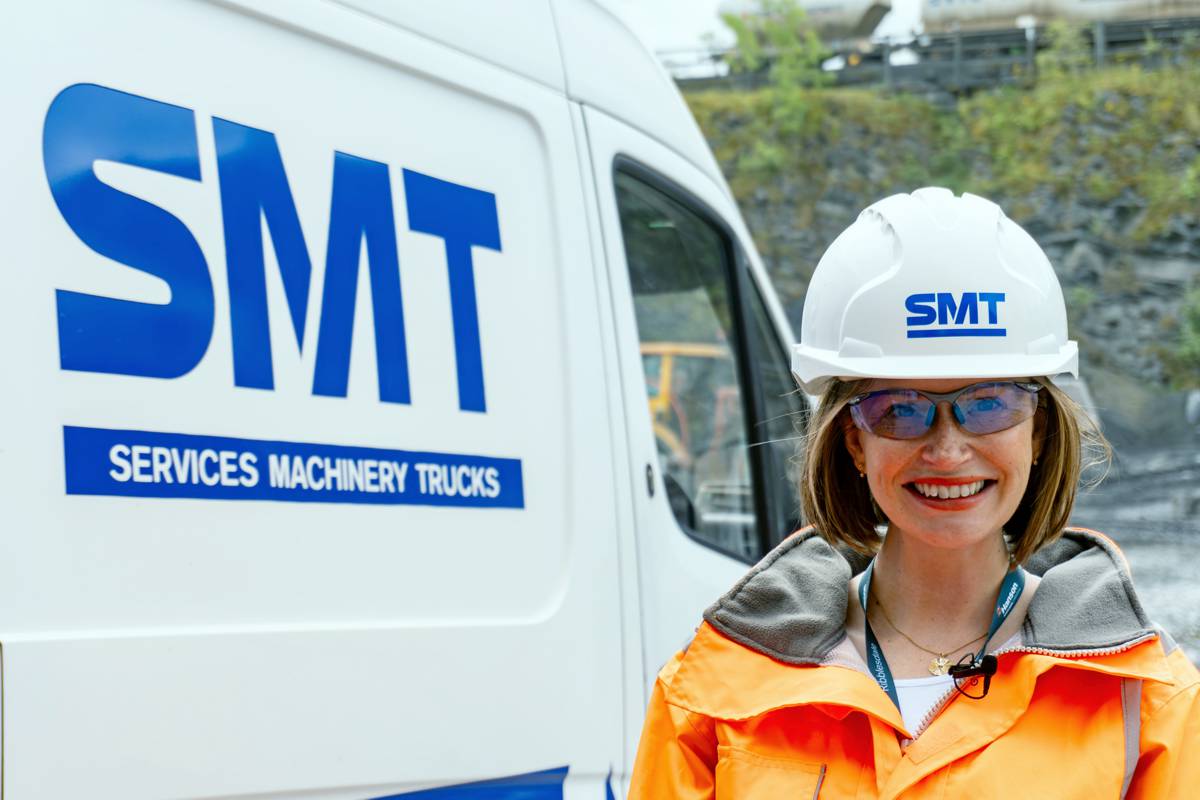
Scaling Rebuild Efforts and Embracing Innovation
The success of the L350F rebuild has prompted Heidelberg Materials UK to consider expanding the programme to additional sites. With SMT’s ongoing support, the company also aims to explore emerging technologies in machine electrification and hydrogen power.
As the construction industry moves toward decarbonisation, collaborations like the one between Heidelberg Materials and SMT demonstrate how equipment rebuilds can contribute meaningfully to a circular economy. By optimising their existing assets, Heidelberg Materials UK is actively reducing its carbon footprint without compromising productivity.
This project serves as a model for the construction sector, proving that sustainable practices can go hand-in-hand with operational efficiency. In the words of Luke Morgan, “Our partnership with SMT represents more than just a service agreement—it’s a shared commitment to sustainability.”
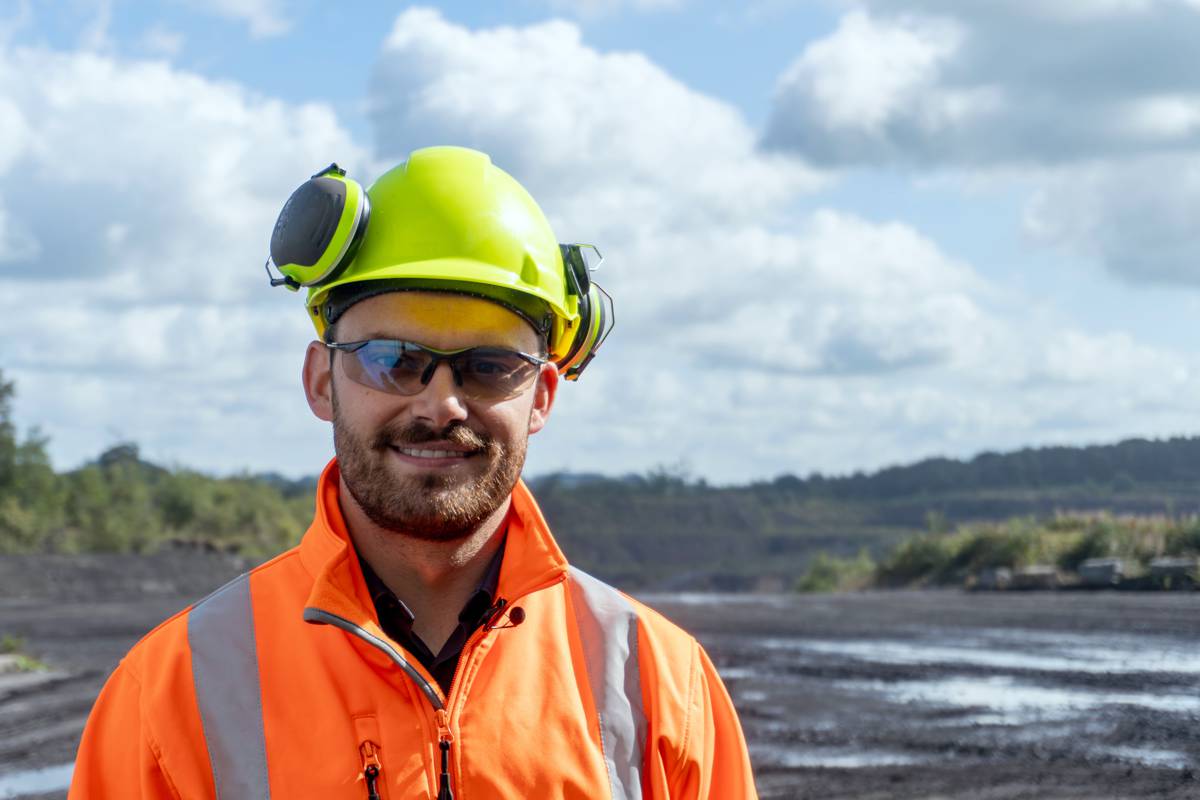
Blueprint for a Sustainable Future
The Heidelberg Materials UK and SMT collaboration exemplifies how companies in heavy industries can adopt sustainable practices.
By focusing on refurbishing, companies can cut down on emissions, reduce waste, and foster a circular economy—all while preparing for a zero-emission future.
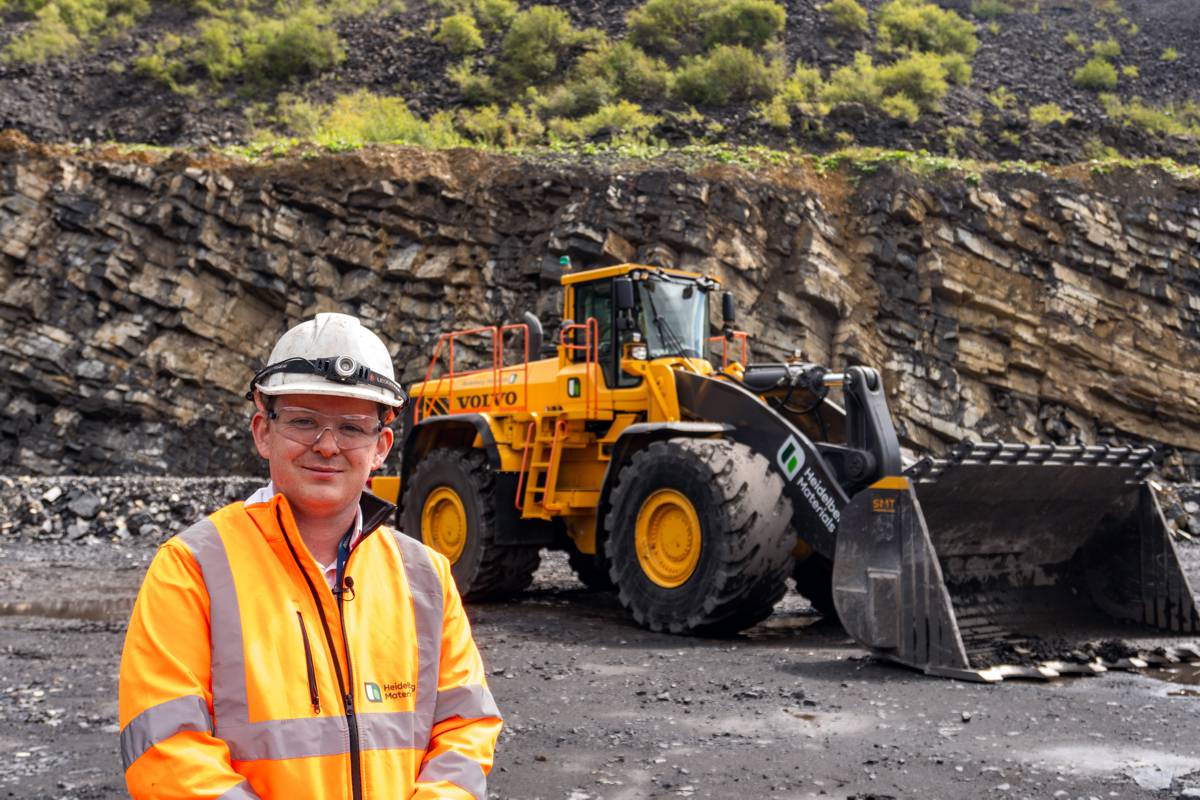