Chalk quarry in France puts Wirtgen 220 SMi 3.8 Surface Miner to the test
On behalf of the Heidelberg Cement Group, Wirtgen conducted a performance test with the 220 SMi 3.8 surface miner at a chalk quarry in Couvrot. The goal was to increase production output compared to the current mining method using a crawler dozer while simultaneously reducing operating costs.
During the demo, several tests were conducted to convince the customer that the smallest Wirtgen surface miner is a viable and more efficient alternative. To do so, the surface miner’s cutting performance, turning time, and fuel consumption were recorded, among other parameters.
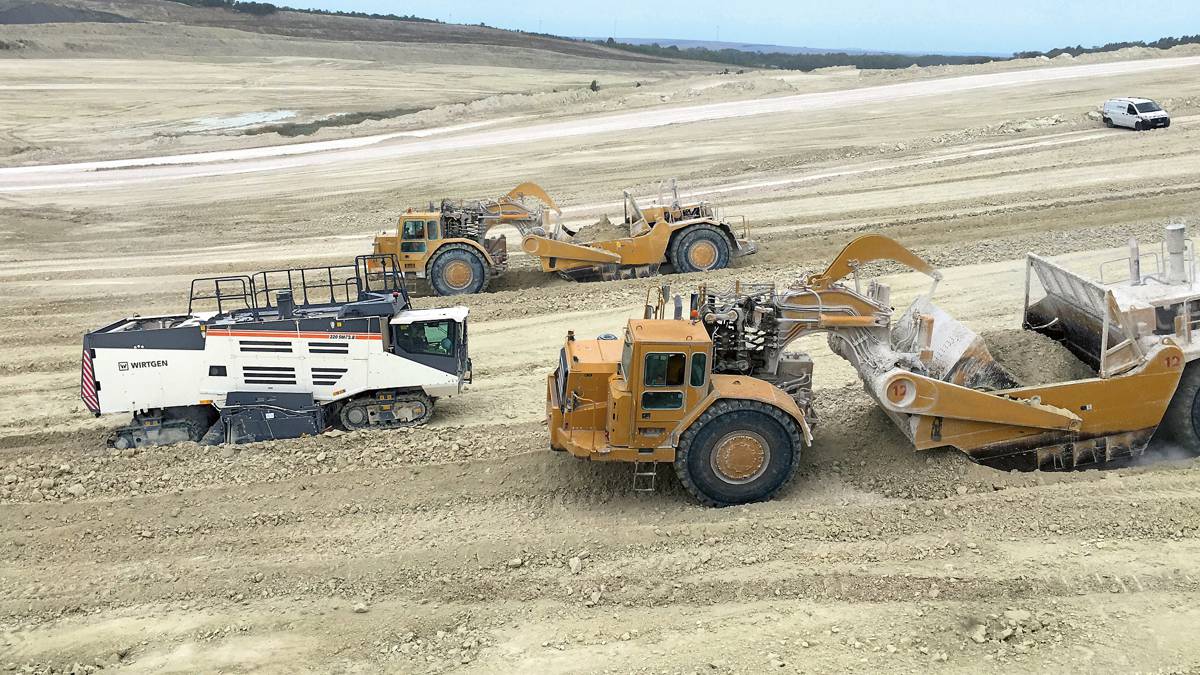
Wirtgen’s 220 SMi 3.8 Validates High Expectations
Up until now, the company has used a bulldozer to break up the chalk in Couvrot, before a scraper loads the material into the hopper (also known as the bowl) and transports it to a temporary storage facility. From there the chalk is transported to the adjacent cement factory, where it is immediately processed.
Since the pieces of rock mined by the dozer are relatively large, with a grain size of up to 80 cm, this mining method causes several problems at once. On the one hand, it creates an uneven surface that must first be levelled by the dozer so that the scrapers can be used to load the material in the first place – an additional, extremely time-consuming task. On the other hand, the coarse grain means that the scrapers require considerable energy and force to load the mined material.
This primarily causes considerable traction issues for the scraper, which results, among other negative effects, in an extremely high level of wear and tear to the machine’s tires. As a result, two to three dozers are currently required per shift to level the excavated area and push the scrapers. In addition to the customer’s expected output of at least 500 m³ per hour, the objective was to eliminate the aforementioned problems with the help of the surface miner.
The 220 SMi 3.8 surface miner is capable of selectively mining raw materials at cutting depths of up to 350 mm and a uniaxial compressive strength of up to 35 MPa. Thanks to its 3.8 m wide cutting drum designed specifically for soft-rock mining, the surface miner achieves maximum productivity at low operating costs, making the compact 220 SMi 3.8 perfect for use in small to large mining operations – a fact that it impressively demonstrated in France.
During the performance test in Couvrot, cutting zones with a length of 150 m and 300 m as well as a width of around 40 m were first mined using the 3.8 m wide cutting drum. The drum was then replaced with a 2.2 m wide drum and tested for one more day.
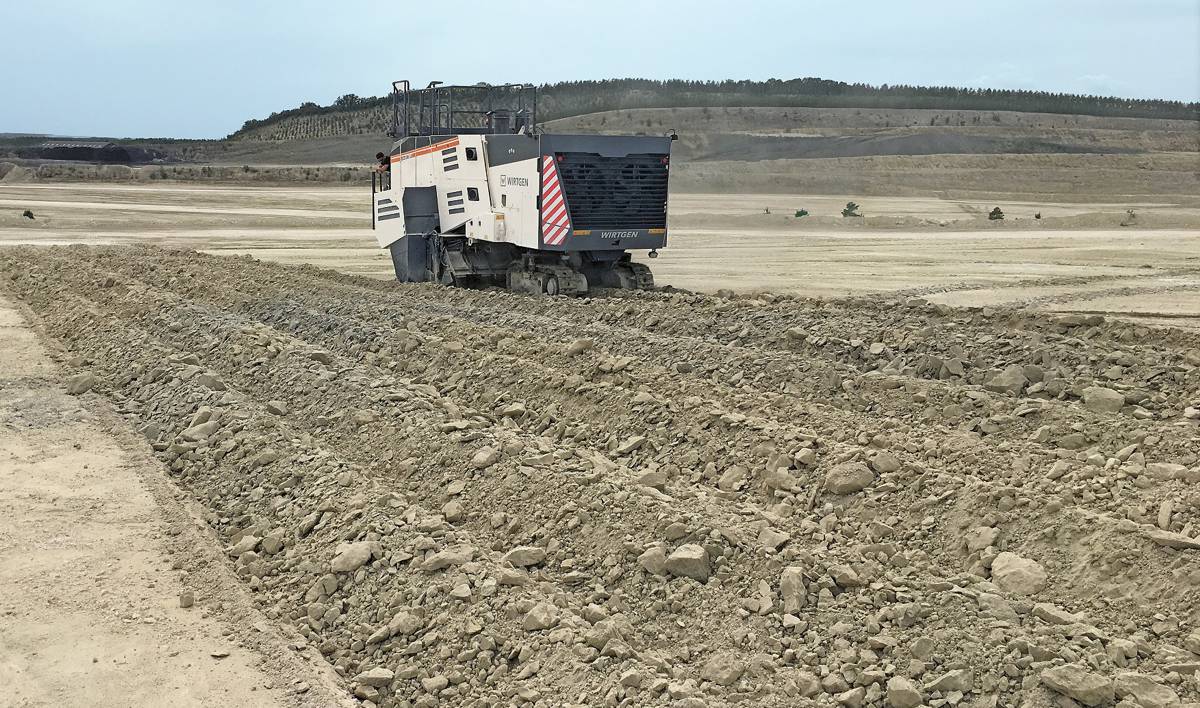
220 SMi 3.8 Surface Miner Proves Its Superiority under Difficult Conditions
According to the customer, the Couvrot region receives significantly more rainfall between October and April than in the summer months. Huge puddles make it difficult to mine the chalk and the moist material has a negative effect on further processing. These conditions were simulated at the beginning of the tests.
The 220 SMi 3.8 had to perform a variety of cutting tasks in muddy and wet terrain. Needless to say, the machine also mastered this challenge without any loss in performance. All of Wirtgen’s surface miner models feature adjustable longitudinal and cross slopes, which ensures that rainwater drains off and keeps the working surface dry.
Even when cutting on slopes with a gradient of up to 16%, the production output of the 220 SMi 3.8 remained high. The machine achieved a peak cutting performance of 1400 m3 per hour. This represents an outstanding result for the customer, since most of the quarry’s mining areas are located on such steep slopes.
The fact that Wirtgen’s surface miner can easily handle the average rock hardness of 20 – 30 MPa was clear even before the tests began. After all, it is designed for rock with a compressive strength of up to 35 MPa. But how would the machine perform under even harder rock conditions?
Some areas of the quarry contain deposits of blue marl with a hardness of up to approximately 40 MPa. Another challenge for Wirtgen’s miner that the 220 SMi 3.8 mastered with an advance rate of 5 – 10 m/min.
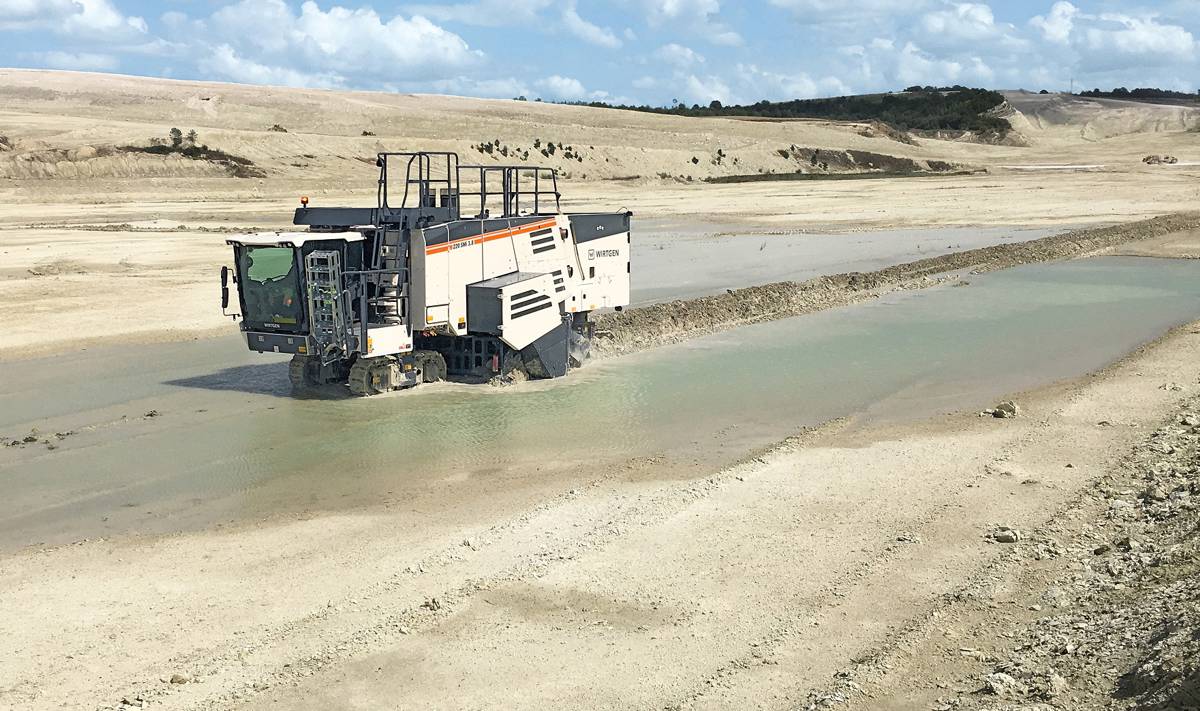
Wirtgen Surface Miners Increase Production Output
In the final and probably most important test, the surface miner was used for an entire shift at the quarry. As part of a fleet with three scrapers and one dozer, the 220 SMi 3.8 cut at two cutting depths of 20 cm and 30 cm.
Thanks to its powerful cutting drum and an engine output of 963 PS at a weight of 59,000 kg, the miner was able to produce significantly smaller and more uniform grain sizes than the dozer. The advantage of this is that the material cut smaller is easier to load than the large pieces of rock, so the scraper and dozer need less power to load the scraper hopper.
In addition, the milled material lies flat on the surface, which means it no longer needs to be levelled with the dozer, saving additional time and therefore cutting costs. In addition, the surface miner produces level surfaces that make it easier to load the scraper and provide stable road surfaces for fast material transport. Thanks to the level haul roads, tire wear can also be reduced.
After completing the test, the quarry operator was more than satisfied with the results achieved by the 220 SMi 3.8. The surface miner far surpassed the target output rate of 500 m³ per hour. In fact, at times the machine was able to extract almost three times the specified amount of chalk per hour.
Due to its outstanding cutting performance and its production of fine grain sizes and flat surfaces, the operator no longer needs to use a dozer, which increases output and reduces costs at the quarry. In addition, the flat surfaces reduce traction problems and scraper tire wear.
Since the chalk is pre-crushed by the 220 SMi 3.8 at the quarry, further costs resulting from the use of crushers can be saved during further processing at the cement factory. In other words, the smallest surface miner delivers what it promises: “maximum performance and cost-effectiveness.”
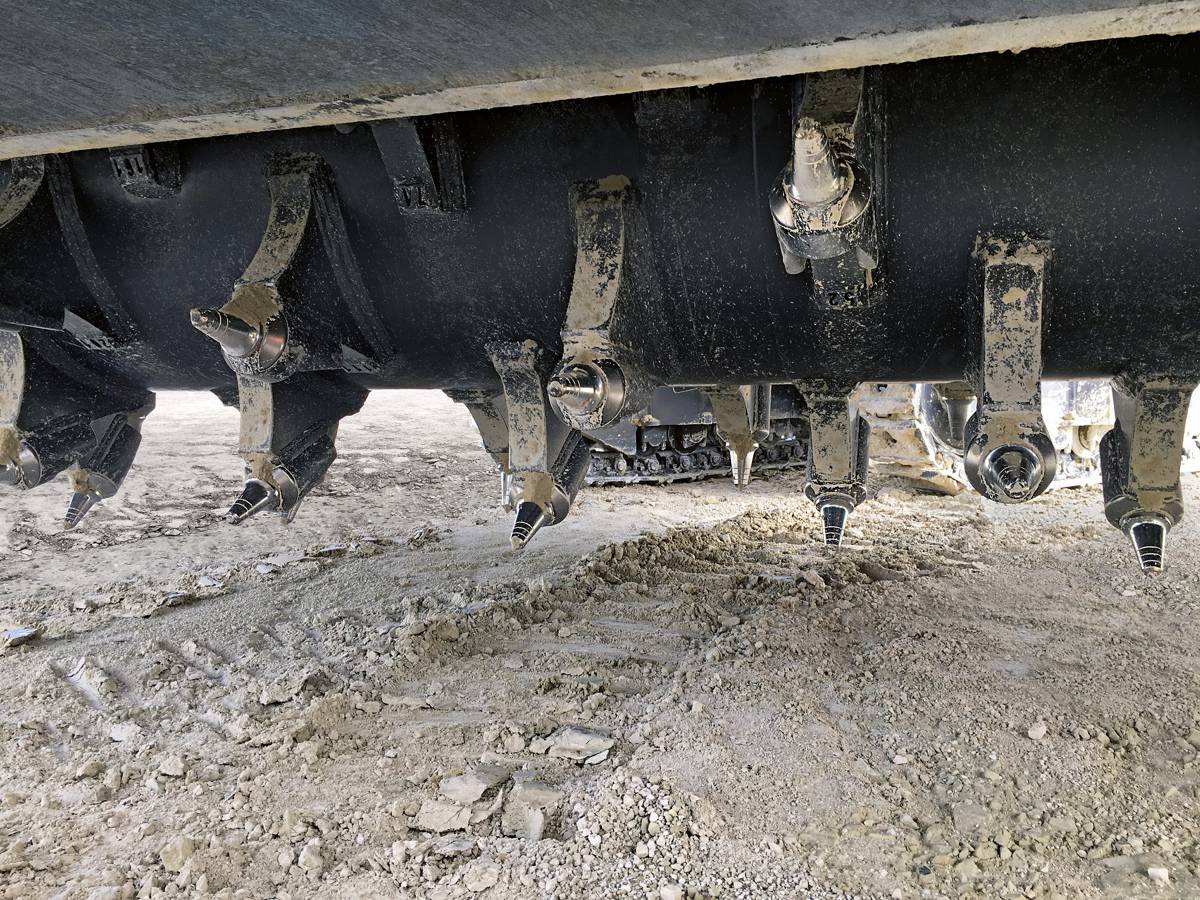