Wirtgen SP 154(i) Concrete Slipform Paving Train connects Prague and Brno
During the modernization of the D1 freeway between the Czech Republic’s two largest cities, two slipform pavers and a texture curing machine from Wirtgen rehabilitated a 67 km stretch of freeway in the direction of Prague.
During the process, the paving train paved two layers in one pass and widened the two lanes at the same time.
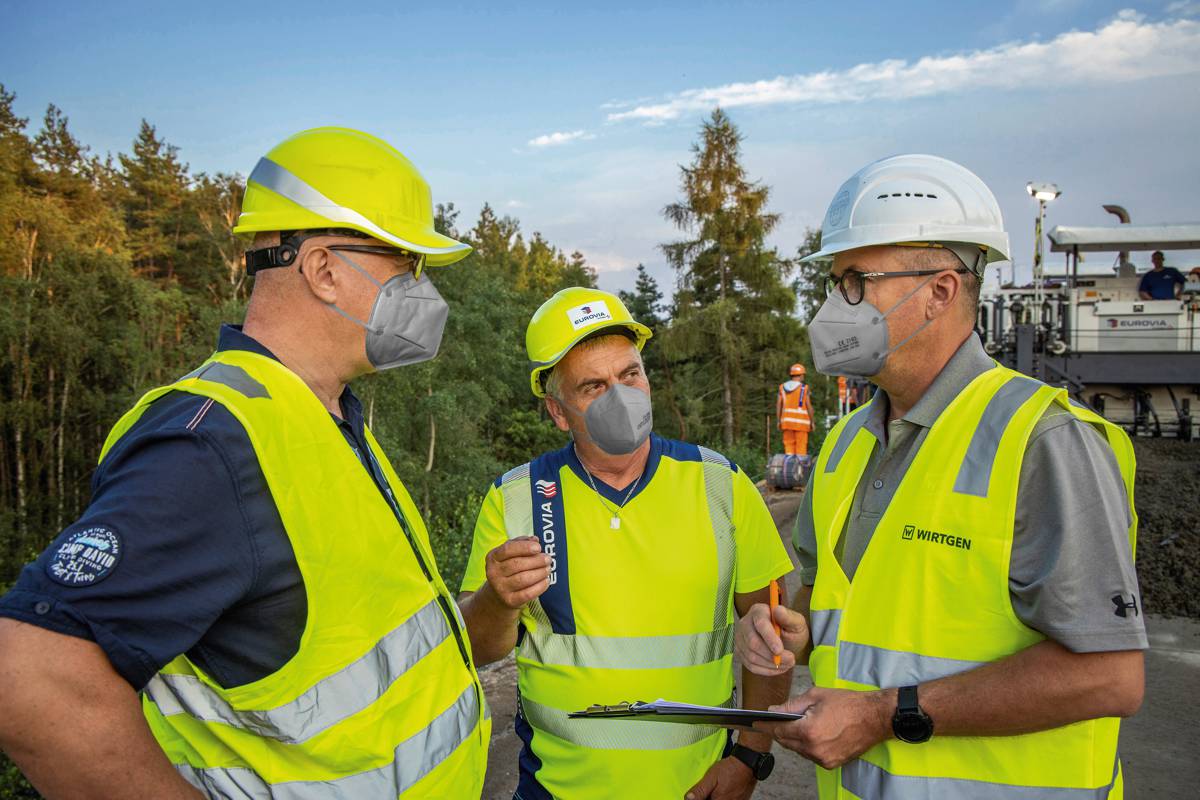
Wirtgen Paving Trains with Large Pavers Guarantee Top Results
For this construction project, which significantly improves the flow of traffic and increases the safety of the Czech infrastructure, more than 60,000 tons of concrete were used over a period of 20 days. This is equivalent to 333 tons per hour. On the D1 freeway, contractor Eurovia CS used the new paving train from Wirtgen to pave the road surfaces with exposed aggregate concrete in optimal quality. With two SP 154(i) slipform pavers as bottom layer and top layer concrete pavers and a TCM 180(i) texture curing machine, Wirtgen was once again able to demonstrate its expertise and performance potential in terms of quality, speed, and cost-effectiveness.
Flexible Control, Easy Loading
The SP 154(i) is equipped with four steerable and slewing crawler units. This allows the machine to be controlled with maximum flexibility in different job site conditions. In addition, the steerable and slewing crawler units make the pavers easy to load. The pavers’ state-of-the-art ECO mode reduces fuel consumption and CO² emissions with only average power requirements.
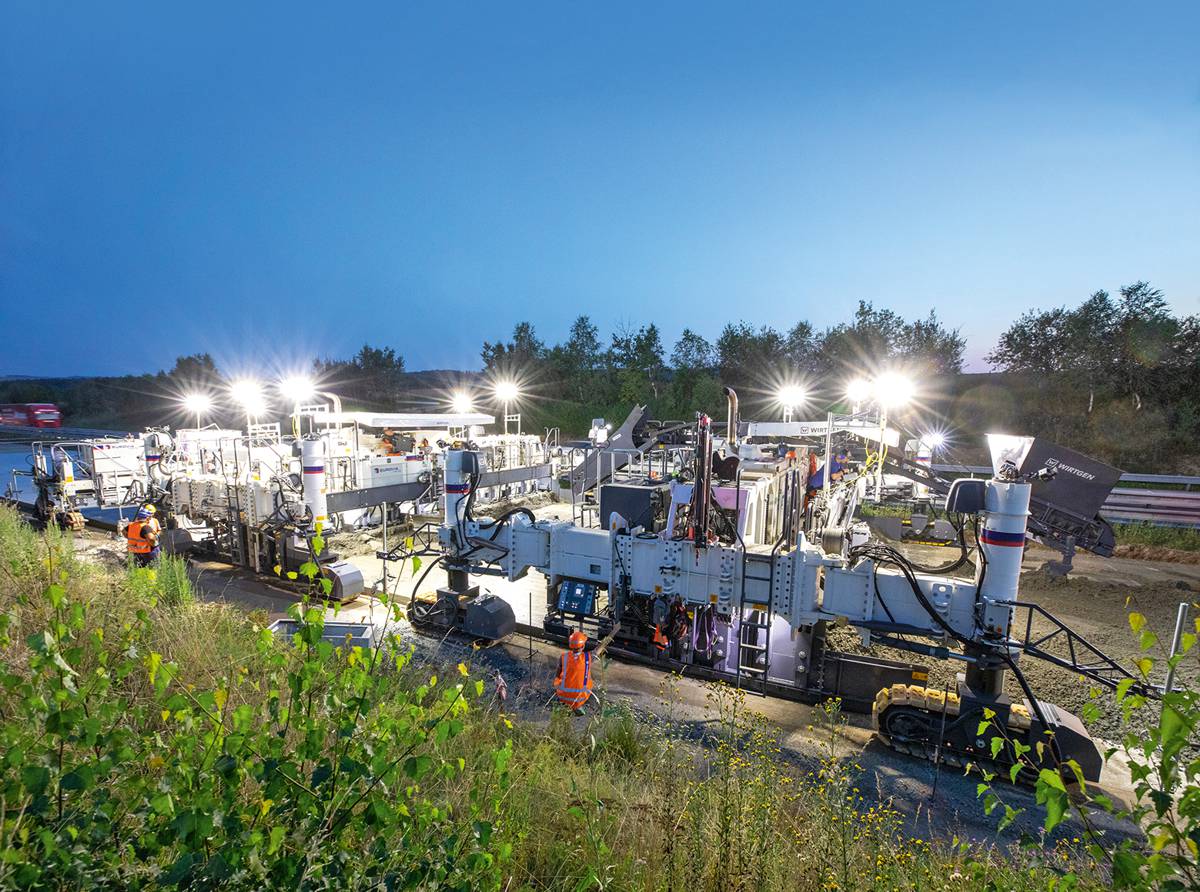
Intuitive, User-Friendly Control
The SP 154(i) features the same control panel design as the other models in Wirtgen’s current fleet of slipform pavers – meaning operators do not have to learn anything new. This guarantees continuous and precise paving without any delays due to training.
Two-Layer Paving with Exposed Aggregate Concrete for Greater Cost Effectiveness
The two-layer paving method, which has been a preferred choice not just for the Czech project, is so cost-effective because only the top layer consists of relatively expensive exposed aggregate concrete. In contrast, a less expensive mix can be used for the road bed. Paving the top concrete layer “wet on wet” produced an excellent bond between the layers on the 11.5 m wide and 27 cm high road surfaces in the direction of Prague. Together, the 22 cm thick bottom layer concrete and the 5 cm thick top layer concrete produce a road surface with an extremely high bearing capacity that is also capable of withstanding the constantly increasing axle weights of trucks transporting heavy loads. As a result, the use of the SP 154(i) also improves safety and makes roads more durable over the long term.
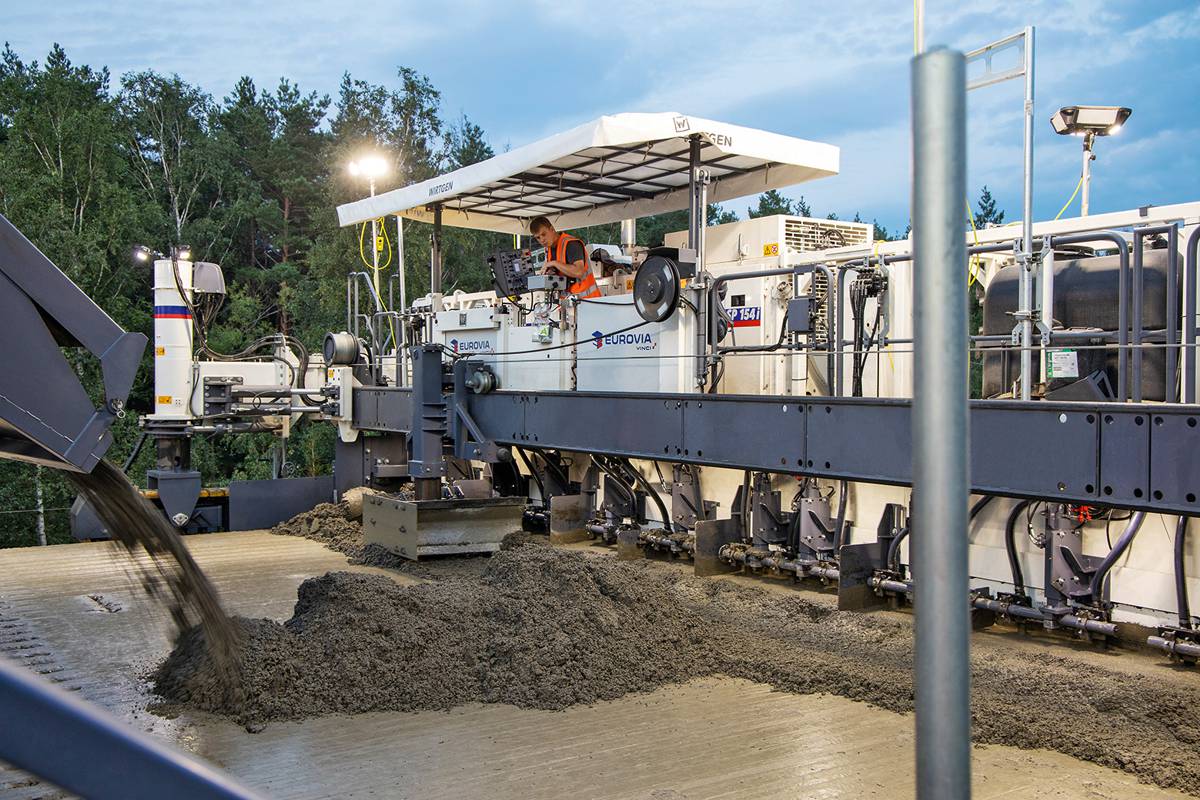
Further Technical Details Regarding Potential Applications
Wirtgen’s concrete paving trains consist of two slipform pavers and one texture curing machine. In general, the SP 154(i) can be set up and used as either a top layer or bottom layer paver. As a bottom layer concrete paver, the SP 154i is equipped with an automatic dowel bar inserter, up to three automatic longitudinal tie bar inserters, and a concrete conveyor to the top layer concrete paver.
When used as a top layer paver, an oscillating beam and super smoother work together to create an ideal concrete surface. Texture curing machines like the TCM 180(i) bring up the rear of the paving train. They can create different surface structures and spray a dispersion on the fresh concrete surfacing to prevent it from drying out prematurely. When paving with exposed aggregate concrete, on the other hand, a surface texture is not created, but instead the distinctive exposed aggregate concrete surface, with a texture depth of approx. 1 mm, is produced by brushing off the top layer of slurry.
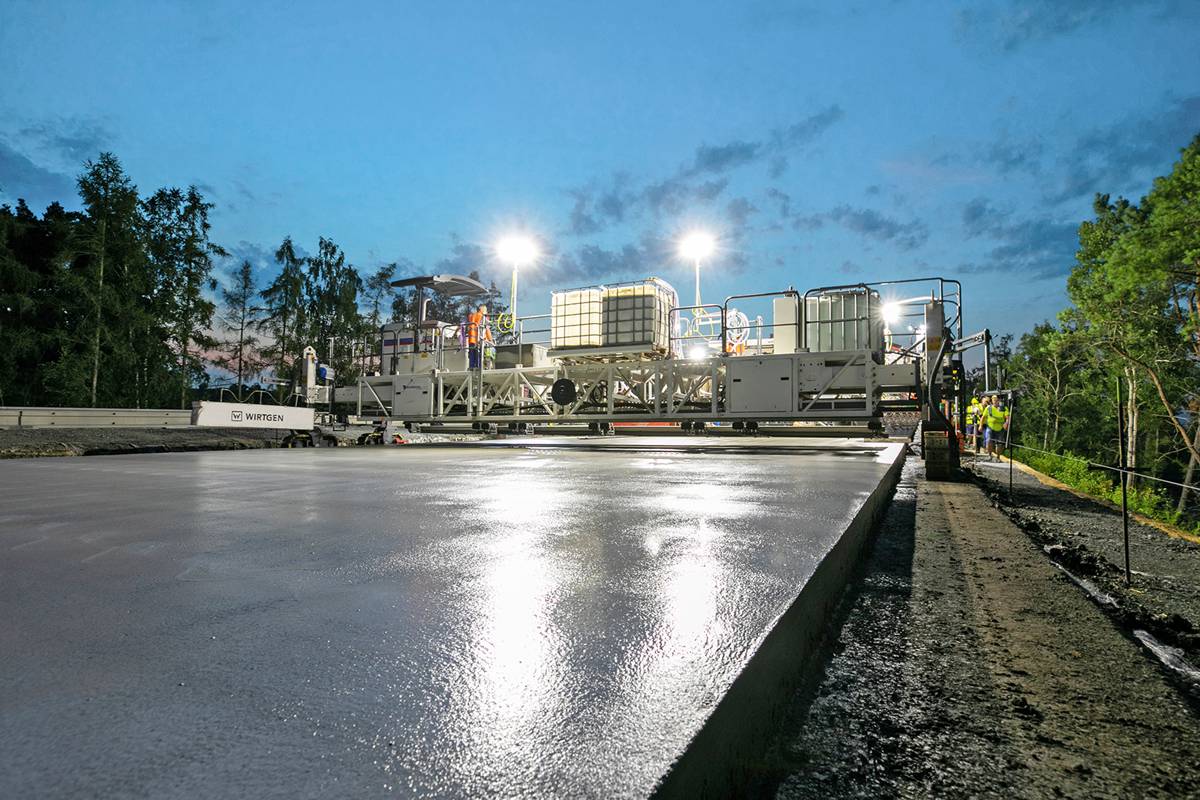