Orbital Composites Technology enables Speedy Manufacturing
An Oak Ridge National Laboratory-developed advanced manufacturing technology, AMCM, was recently licensed by Orbital Composites and enables the rapid production of composite-based components, which could accelerate the decarbonization of vehicles, airplanes and drones.
Additive manufacturing compression moulding, or AMCM, uses short-fibre-filled polymer and continuous fibre to print directly onto a mould with precise orientation to make parts such as propeller blades or battery boxes.
Compression moulding then turns the print into an accurate finished piece. ORNL researchers proved AMCM significantly reduces time and cost by producing 100 parts in five hours, with each piece taking less than three minutes to print.
“By combining the fibre control of additive with the low porosity of compression moulding, we can enable the high-volume production of next-generation composites,” ORNL’s Vipin Kumar said. “The mobility and aerospace industries need these lightweight materials to improve the energy efficiency of their applications.”
ORNL collaborated with Orbital to develop AMCM on a robotic system. Additional collaborators included IACMI — The Composites Institute.
UT-Battelle manages ORNL for DOE’s Office of Science, the single largest supporter of basic research in the physical sciences in the United States. DOE’s Office of Science is working to address some of the most pressing challenges of our time. For more information, visit energy.gov/science.
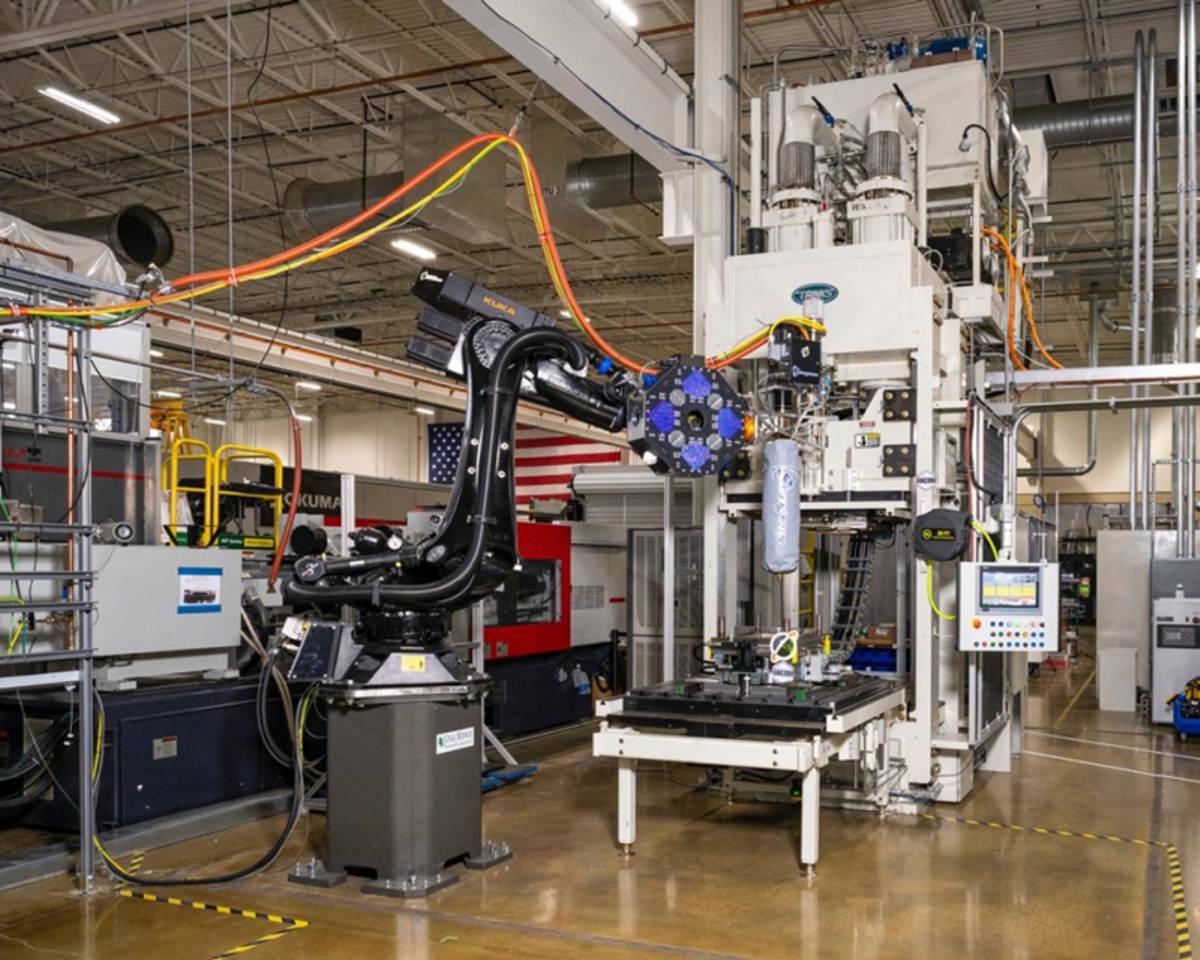