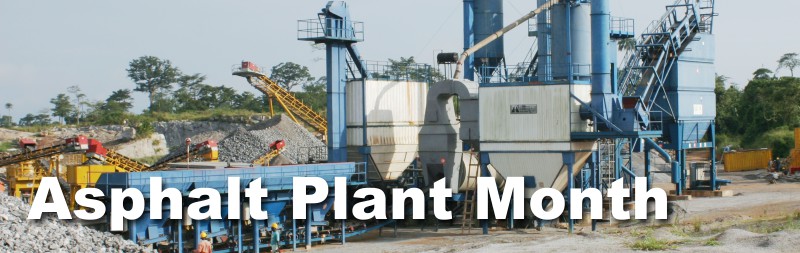
May is Asphalt Plant Month
Asphalt Plant Month at Highways.Today turns the spotlight on the backbone of road construction and infrastructure: the asphalt plant. Throughout May, we’ll be celebrating the marvels of modern asphalt production, from the towering silos to the intricate conveyor systems that keep our roads rolling.
It’s a month dedicated to the innovations that streamline production, the environmental strategies that are paving the way to greener horizons, and the people behind the scenes who ensure the industry’s robust growth. Expect a journey through state-of-the-art facilities, insights into cutting-edge research, and a salute to the sustainable practices that are reshaping the landscape of asphalt production.
Join us in honouring these industrial stalwarts that blend technology and efficiency to connect communities and drive progress.
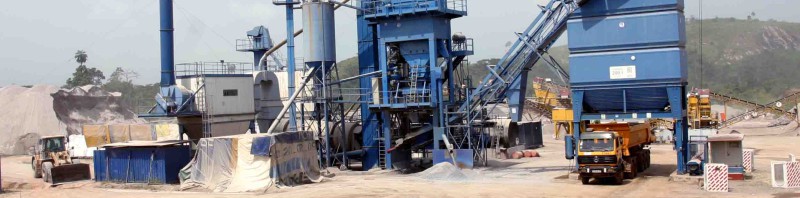
Types of Asphalt Plant
An asphalt plant is a facility that manufactures asphalt, also known as macadam, coated roadstone, blacktop or asphalt concrete.
Asphalt is widely recognized for its durability, weather resistance, and excellent adhesion to the road surface. It’s used in road construction and maintenance to create surfaces that can endure the stresses of traffic and the environment.
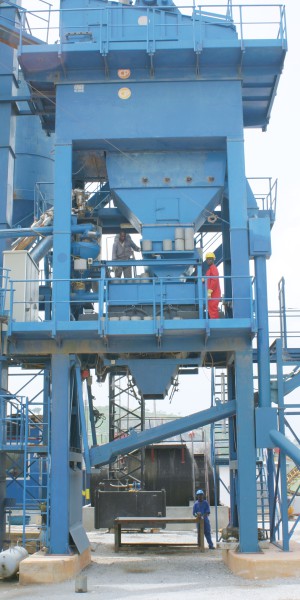
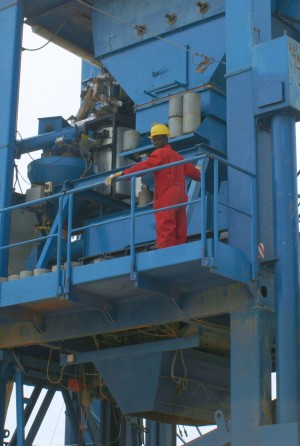
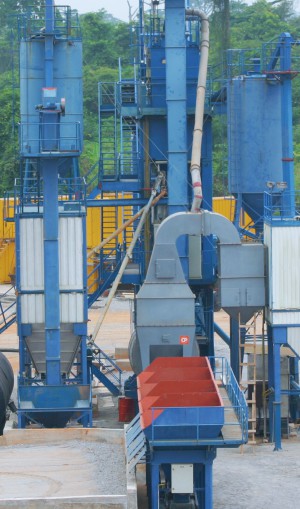
Batch Mix Plants
Batch mix plants offer the highest level of flexibility in asphalt production, allowing precise control over the production process. They work by sequentially adding and processing controlled amounts of raw materials to produce asphalt in batches, each of which can have a different composition. This is particularly beneficial when projects require varying mix designs or the incorporation of recycled asphalt. In a batch plant, the aggregate is dried and heated before being mixed with binder in a separate mixer, which means the plant can easily switch between mix designs. Batch plants are often the preferred choice for high-grade roads and other projects where quality takes precedence over quantity.
Drum Mix Plants
Drum mix plants are valued for their simplicity and efficiency. They produce asphalt continuously, which leads to higher production rates and lower operation costs compared to batch mix plants. All the ingredients are fed into the drum, where they are dried, heated, and mixed in a single process. This continuous flow method means less start-up and shut-down time and less waste. Drum mix plants are typically used for large-scale construction projects where the same mix is used over an extended period, making them ideal for constructing highways and other major infrastructure.
Continuous Mix Plants
Continuous mix plants are similar to drum mix plants, but with the ability to alter the mix without stopping production. This flexibility makes them suitable for projects that require a constant supply of asphalt but might need adjustments to the mix properties during production. These plants maintain a constant flow of materials through the drum, and adjustments to the composition are managed by varying the feed rates of the aggregate, filler, and binder.
Mobile Asphalt Plants
Mobile asphalt plants are designed for projects that require the asphalt production plant to be moved. These plants are ideal for remote locations or projects that move geographically, such as road or airport runway constructions. They can be dismantled, transported, and set up quickly, offering high levels of mobility and flexibility. Despite their portability, they can still match the production rates of stationary plants and can produce a variety of asphalt mixes.
Stationary Asphalt Plants
Stationary asphalt plants are intended for permanent locations and offer the highest production rates. They are often found near city centers or large road construction projects where they serve a fixed geographic region. These plants are typically larger and more productive than mobile or batch mix plants, with the ability to run 24/7 if needed. Stationary plants are designed to offer a long service life with consistent output and are capable of producing various asphalt mix types in large volumes.
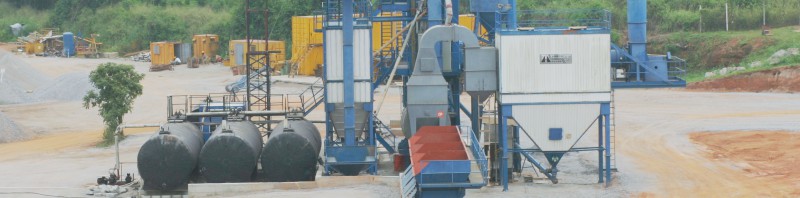
Asphalt Plant Components
Cold Feed Bins: Cold feed bins are essential storage units within asphalt plants that manage and supply the raw aggregates needed for asphalt production. Each bin holds a different size or type of aggregate, allowing for precise customization of the asphalt mix. These bins release aggregates in controlled amounts to ensure a consistent flow into the drying system, which is crucial for maintaining the quality and uniformity of the asphalt produced.
Conveyor Belts: Conveyor belts play a pivotal role in transporting aggregates from the cold feed bins to the dryer drum. They ensure a continuous and efficient flow of materials within the plant, thus maintaining a steady production pace. These belts need to be durable and capable of handling high loads to prevent breakdowns and maintain operational efficiency.
Dryer Drum: The dryer drum is a cylindrical vessel that serves to dry and heat the aggregates. It is equipped with a rotating mechanism that ensures even heating and removal of moisture, which is critical for the optimal bonding of the asphalt mixture. The drum includes a burner at one end that provides the necessary heat, typically fueled by gas, oil, or coal.
Burner: The burner is a key component that generates heat necessary to dry and heat the aggregates in the dryer drum. By burning fuel efficiently, it creates a controlled flame whose intensity can be adjusted to affect the temperature within the drum, thereby influencing the quality of the final asphalt mix.
Dust Collection System: A dust collection system is vital for capturing and filtering out the fine particles (dust) produced during the drying process. This system not only helps in maintaining air quality but also ensures compliance with environmental regulations. Effective dust collection prevents dust emissions, which can be harmful to plant personnel and the surrounding environment.
Hot Aggregate Elevator: The hot aggregate elevator is responsible for moving the heated aggregates from the dryer drum to the vibrating screens. This elevator must handle high temperatures and provide reliable transport to ensure a steady flow for the screening process.
Vibrating Screens: Vibrating screens classify the heated aggregates into various sizes by shaking them through progressively smaller meshes. These screens are crucial for quality control, ensuring that aggregates are properly sized before they are moved to the hot bins for temporary storage.
Hot Bins: Hot bins are compartments that store the hot aggregates after they have been sorted by the vibrating screens. They allow for the precise measurement and proportioning of aggregate sizes in the asphalt mix, which is critical for achieving the desired paving properties.
Weighing System: The weighing system accurately measures the hot aggregates, bitumen, and filler materials before they are mixed. This system is fundamental to achieving the correct formulation of asphalt, as it ensures that each component is added in the proper ratio.
Mixer Unit: The mixer unit is where the hot aggregates are blended with bitumen and filler materials to produce the final asphalt mix. This component is crucial for ensuring that the asphalt is homogeneous and meets the specified criteria for paving.
Asphalt Storage Tanks: Asphalt storage tanks hold the bitumen used in the asphalt mix. They maintain the bitumen at a controlled temperature to keep it fluid and workable until it is needed in the mixing process, thereby ensuring smooth and efficient operations.
Filler Silos: Filler silos store the mineral filler materials used in the asphalt mix. These materials, such as lime or cement dust, are critical for enhancing the properties of the asphalt, such as durability and resistance to deformation.
Control Room: The control room is the operational heart of the asphalt plant. It houses the control systems and panels that operators use to manage and monitor the entire production process, ensuring that the plant operates smoothly and efficiently.
Loading Area: The loading area is where the finished asphalt mix is loaded onto trucks for transport to construction sites. This area needs to be efficiently organized to handle the high throughput of material and to maintain the quality of the asphalt during the loading process.
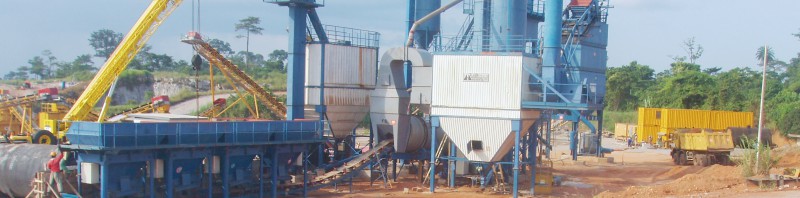
Bitumen Storage and Handling
Effective bitumen storage and handling are pivotal for maintaining the quality of asphalt, which begins with ensuring the binder used has uniform properties such as consistency and temperature.
Proper management of these elements involves precise heating to keep the bitumen fluid, the use of high-quality tanks designed to maintain temperature without degradation, and safe, efficient transport mechanisms to move the bitumen from production to application sites.
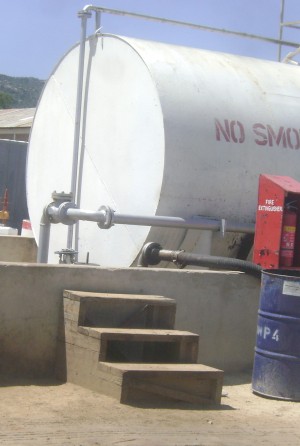
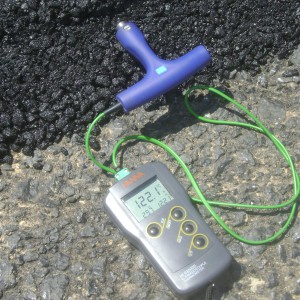
Heating: Maintaining an optimal temperature is crucial as it affects the viscosity and performance of the asphalt. Advanced heating systems, such as hot oil and steam transfer fluid systems, have replaced direct-fired heaters for efficiency and safety.
Permitting and Safety: Navigating local regulations and safety codes, such as those from the NFPA and NEC, is essential for operational compliance. Safety measures must address high-temperature operations and potential hazards from steam systems.
Transporting: Bitumen is typically transported by rail or barge and then piped to storage tanks. Modern facilities utilize finned tubes for more efficient heat transfer during this process.
Tank Construction and Management: Tanks must be carefully constructed with attention to insulation and heating mechanisms. Management practices should prevent overflows and maintain bitumen levels above heating coils to prevent coking.
Environmental and Quality Control: Managing fumes and emissions is critical for safety and environmental protection. Quality control measures include segregating different types of bitumen and thorough testing to ensure product integrity.
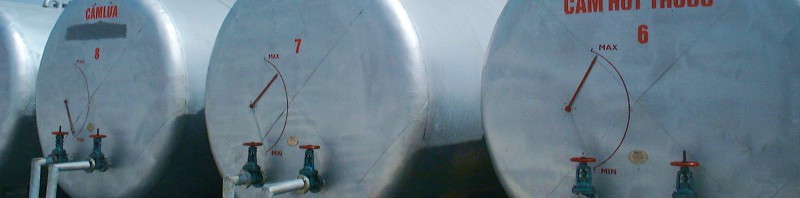
Asphalt Plants Trends
Currently, the asphalt plant market is undergoing transformative changes, propelled by increasing urbanization, heightened sustainability goals, and technological advancements.
Here are the top trends that are defining the evolution of the asphalt plant industry:
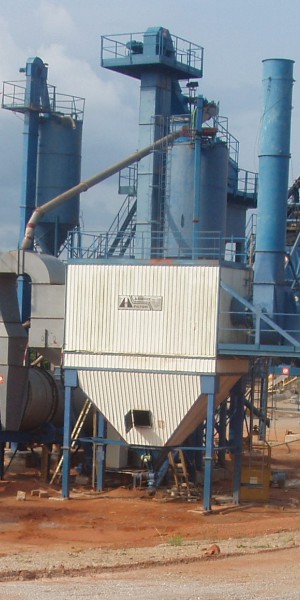
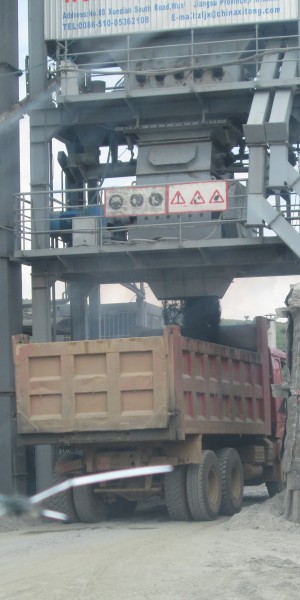
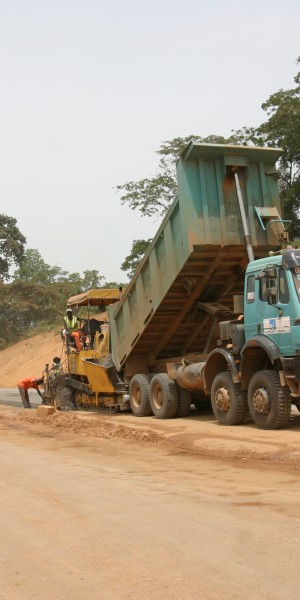
Increased Infrastructure Development and Urbanization
There is a notable boom in global infrastructure development, including new road constructions, expansions, and maintenance of existing roadways. This rise in construction activities has led to a robust demand for asphalt, and by extension, for asphalt plants. Urbanization further compounds this demand, as expanding cities require more complex and robust road networks. The asphalt plant market stands to gain substantially from these ongoing developments.
Sustainability Practices
Environmental considerations are increasingly shaping the asphalt plant market. Manufacturers are innovating to introduce technologies that curb emissions and integrate sustainable practices within their operations. This includes enhanced burner designs that decrease air pollution, recycling methods that reintroduce reclaimed asphalt pavement (RAP) into new mixes, and the adoption of bio-based binders. These sustainable technologies are not only environmentally beneficial but are also cost-effective over the long term.
Automation, Process Control
Automation is becoming a cornerstone in the operation of modern asphalt plants. These facilities are now equipped with advanced computer systems that automate key production steps, from aggregate and binder input to temperature regulation during the mixing process, alongside automated quality checks. This shift not only streamlines production but also ensures a consistent quality of asphalt, crucial for the longevity of pavement.
Data Analytics, Telematics and Predictive Maintenance
Asphalt plants are increasingly incorporating data-driven technologies. Sensors throughout the plant monitor everything from material flows to energy use, providing a wealth of data that can be analysed to fine-tune operations, predict maintenance needs, and enhance overall efficiency. Asphalt plants can be remotely operated by the manufacturer, who can also run diagnostic tests and use predictive maintenance to avoid unexpected downtime and prolonging plant life.
Cold/Warm Mix Asphalt Technologies
Cold and warm mix asphalts represent a shift towards more energy-efficient asphalt production methods. Unlike traditional hot mix asphalt, these are produced at lower temperatures, reducing the energy required for heating and thus decreasing the environmental footprint. While it is not suitable for all types of projects, its use is expanding, particularly in applications where environmental impact is a significant concern.
Regulatory Compliance and Emission Controls
As regulatory frameworks around air pollution tighten, asphalt plant operators are compelled to adopt advanced emission control technologies. This includes the implementation of dust collection systems, low-NOx burners, and other mechanisms designed to meet stringent environmental standards and maintain operational licenses.
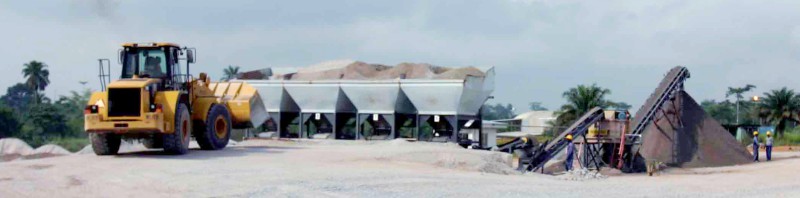
The Road Ahead

Looking to the future, the asphalt plant market is set to expand significantly. Demand driven by infrastructure needs will continue to grow; sustainability will guide technological and operational decisions; and advancements in automation and data analytics will refine production efficiencies.
Cold and warm mix technologies will provide necessary alternatives, while stringent environmental regulations will push for cleaner, more sustainable operations. These trends collectively forecast a dynamic path forward for the asphalt plants industry, ensuring it remains at the forefront of building the foundations for global transportation infrastructure.
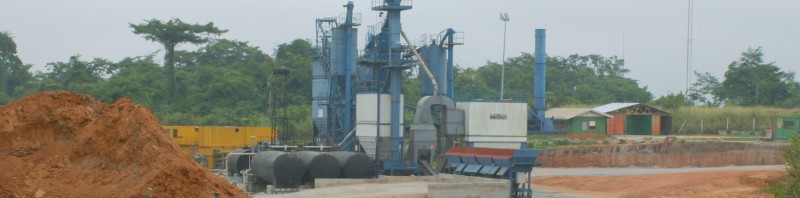
Evolution of Asphalt Mixing Plants
The journey of asphalt mixing plants from simple, manually-operated setups to today’s high-tech operations illustrates a profound transformation driven by innovation and efficiency. This evolution reflects the industry’s response to increasing demands for durable and high-quality roads.
Origins and Early Developments
Asphalt’s use as a paving material surged in the late 19th century, prompting the development of basic asphalt mixing techniques. Early asphalt plants were rudimentary, involving manual mixing of aggregates and bitumen.
This process was not only labour-intensive but also inconsistent, affecting the quality of the asphalt produced. The introduction of mechanical mixers in the early 20th century was a significant improvement, mechanizing the blending process and increasing efficiency.
Advancements Through the 20th Century
The 20th century saw rapid technological advances in asphalt mixing. Rotary drum mixers and batch plants were introduced, revolutionizing asphalt production by enhancing both the rate and precision of mixing.
The adoption of continuous mixing processes further optimized efficiency, ideal for large-scale projects requiring substantial asphalt quantities.
Modern Innovations and Sustainability
The development of drum mix asphalt plants marked a major milestone, offering increased mobility and faster production rates. These plants support on-site asphalt production, which is especially beneficial for remote or difficult terrain projects.
Despite the benefits of drum mix plants, batch plants remain popular for their ability to produce precisely tailored asphalt mixes.
Environmental Considerations
Modern asphalt plants incorporate significant environmental safeguards, such as advanced pollution control systems and recycling technologies. The use of reclaimed asphalt pavement (RAP) in new mixes exemplifies sustainable practices that conserve resources and reduce costs.
Furthermore, modern facilities focus on reducing emissions and have embraced warm mix asphalt (WMA) technologies, which lower the temperatures required for mixing, thereby saving energy and reducing greenhouse gases.
The Digital Transformation
The latest evolution in asphalt plants involves automation and digitalization, enhancing efficiency and quality control. Smart plants utilize sensors and real-time data analytics to optimize production processes, adjust to changing conditions, and ensure consistent output.
These advancements allow for remote monitoring and management, boosting productivity and operational uptime.
Adaptability and Innovation
The evolution of asphalt mixing plants from basic to advanced exemplifies the industry’s adaptability and commitment to improvement.
Looking ahead, the focus on innovation, environmental sustainability, and smart technologies will continue to shape the future of asphalt production, ensuring it meets the modern demands of road construction.
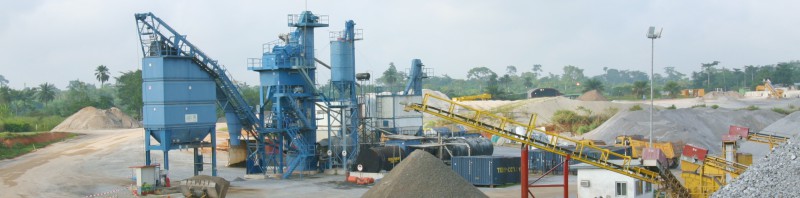
Top 5 Asphalt Plant Articles
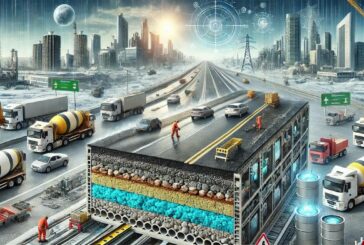
Enhancing Bituminous Pavement Durability
Enhancing Bituminous Pavement Durability The durability of asphalt mixtures is significantly influen...
Read more Asphalt Plant News and Asphalt and Bitumen News.
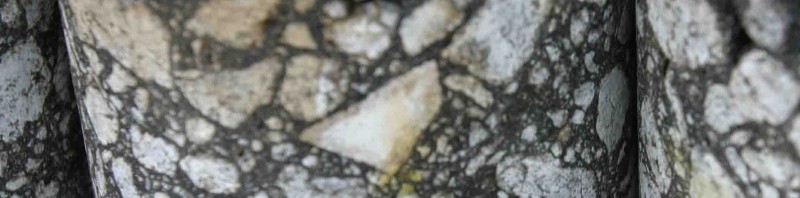
Asphalt Plant Manufacturers
This list represents a sample of the top Asphalt Plant Manufacturers:
- ADM Asphalt Plant: Known for robust and reliable asphalt equipment, ADM Asphalt Plant provides a variety of durable asphalt mixing solutions tailored to meet specific customer needs.
- ALmix – Asphalt Equipment Company: Known for its robust and innovative asphalt equipment, ALmix excels in producing high-quality, durable machinery tailored to specific customer needs.
- Ammann: This Swiss company boasts over 150 years of expertise and is celebrated for its durable and comprehensive asphalt mixing plant offerings.
- Ardent: Emerging from India, Ardent is making a mark with its efficient and technologically advanced asphalt plants, contributing to the country’s road construction and infrastructure development.
- Astec Industries: Based in the USA, Astec Industries has been a leader in manufacturing a broad array of asphalt plants since 1972, known for their efficiency and longevity.
- Benninghoven: Part of the Wirtgen Group, German-based Benninghoven is recognized for its innovative technology in asphalt mixing plants, offering both mobile and stationary solutions.
- CMI Roadbuilding Limited: A prominent name in the industry, CMI Roadbuilding Limited offers a complete range of asphalt plants and has been innovating roadbuilding solutions for decades.
- Eagle (G.E.T.) Fabrications LTD: Eagle specializes in fabricating asphalt equipment that stands out for its reliability and performance, supporting road infrastructure projects globally.
- Ermont: Originating from France, Ermont is renowned for designing and manufacturing continuous asphalt plants, a staple in the industry since 1924.
- e-mak: Notable for its environmentally friendly asphalt plants, e-mak focuses on energy efficiency and recyclability in its designs.
- Intrame: Intrame designs and manufactures a wide range of asphalt plants known for their adaptability and capability to meet varied client needs.
- Kaushik Engineering Works: This company specializes in cost-effective and efficient asphalt mixing plants, with a strong focus on the Indian market.
- Lintec: Lintec provides innovative asphalt mixing plants characterized by their quality and flexibility, earning a respected status in the industry.
- Luton group: Luton group offers comprehensive solutions with their state-of-the-art asphalt mixing plants, known for precision and adaptability.
- Lyroad: Lyroad manufactures cutting-edge asphalt mixing plants with a focus on sustainability and advanced engineering techniques.
- Marini: As a part of the Fayat Group, Marini from Italy is renowned for its production of high-quality hot mix asphalt plants with global reach.
- Parker Plant: With over 100 years of experience, UK-based Parker Plant delivers reliable solutions for quarrying, construction, road infrastructure, and recycling projects.
- Polygonmach: Polygonmach stands out for its engineering precision and innovative designs in asphalt mixing technology.
- Sany: As one of the largest construction machinery manufacturers globally, Sany from China is known for its advanced asphalt batching plants.
- Stansteel: Stansteel is recognized for its high-quality, durable asphalt plant solutions tailored to professional asphalt producers.
- Tarmac International Inc.: Specializing in thermal rotary dryers, Tarmac International Inc. provides effective solutions for asphalt production.
- Tietuo: Renowned for its mobile asphalt mixing plants, Tietuo offers equipment that is easy to transport and set up, providing flexible solutions to the industry.
- XCMG: Xuzhou Construction Machinery Group, known as XCMG, is a leading manufacturer of construction equipment, including highly efficient asphalt mixing plants.
- Zoomline: Zoomline is a significant player with robust asphalt mixing plants that cater to complex and large-scale infrastructure projects.
This comprehensive list showcases companies at the forefront of asphalt plant manufacturing, each contributing with specific expertise and innovative solutions to meet the growing demands of the road construction industry.
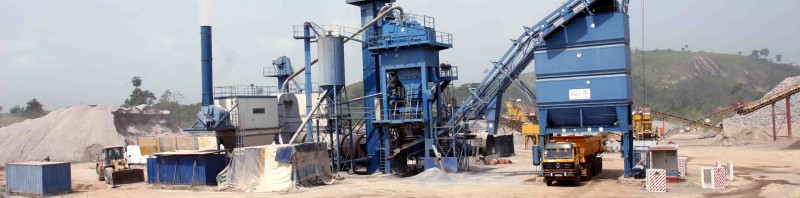
Asphalt & Bitumen Courses
The education section of our exploration into asphalt plants focuses on the foundational knowledge and technical skills required to operate and manage these complex systems effectively. Understanding the mechanics of asphalt production, from the initial aggregate handling to the final asphalt output, is crucial for anyone in the field.
By empowering industry professionals with the right information and skills, we aim to enhance the efficiency, safety, and quality of asphalt production globally, ensuring that workers are not only proficient in current technologies but also prepared for future innovations in the field.
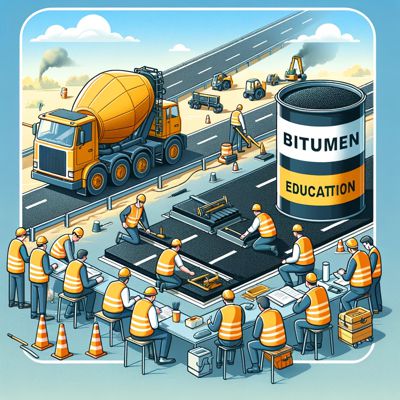
Mastering bitumen for better roads and innovative applications
École des Ponts ParisTech
During four weeks, best experts in bitumen bring you their knowledge and experience to build a strong understanding of today’s realities and new perspectives on the future of bitumen.
Total is the European leader on bitumen markets. Innovation has always been the key to sustainability and durability in the products they develop. Their main objective here is to share technical knowledge and experience to insure bitumen are being used in the most effective and efficient ways for their different applications in road works.
Ecole des Ponts, France oldest engineering school, remains very much in the present, as it has always been, in training engineers in order to meet the needs of our society and citizens in key areas such as transport housing and urban services, but also in fields like energy, environment, climate sciences, land-use planning and sustainable development.
The course will teach you:
- Bitumen market, generalities, the manufacture of bitumen, transport, uses of bitumen, main developments and alternatives.
- Constitution, structure and characterization of bitumen – specifications – rheology.
- Modifications of bitumen and applications (road and roofing).
- Health, Safety, Environment & Quality concerns regarding bitumen, and examples of research & innovation actions.
Nineteen world recognized experts on bitumen are contributing to this online course.
The idea is to provide the broadest prism on this topic area with speakers coming from research, industry and end users.
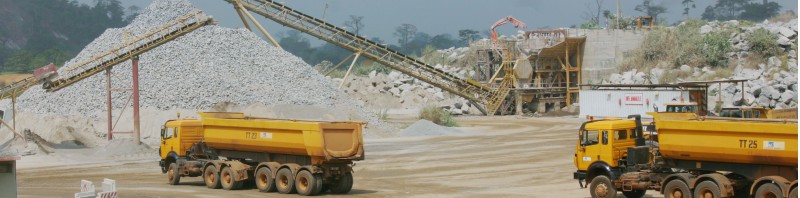
As we conclude our exploration of the evolution of asphalt mixing plants, it’s clear that this journey has been one of constant advancement and adaptation. The shift from manual processes to automated, environmentally conscious production methods underscores the industry’s commitment to innovation and sustainable practices.
As the demand for more durable, cost-effective, and environmentally friendly roads continues to grow, the role of advanced asphalt mixing plants becomes ever more critical. Moving forward, the asphalt industry is set to continue its trajectory of innovation, using cutting-edge technology to pave the way for the future of road construction and maintenance.
This commitment ensures that our roads not only meet today’s needs but are also built to withstand the challenges of tomorrow.