Stress in 3D Printed parts measured with Neutrons
Using neutrons to see the additive manufacturing process at the atomic level, scientists have shown that they can measure strain in a material as it evolves and track how atoms move in response to stress.
“The automotive, aerospace, clean energy and tool-and-die industries — any industry that needs complex and high-performance parts — could use additive manufacturing,” said Alex Plotkowski, materials scientist in ORNL’s Materials Science and Technology Division and the lead scientist of the experiment. Plotkowski and his colleagues reported their findings in Nature Communications.
ORNL scientists have developed OpeN-AM, a 3D printing platform that can measure evolving residual stress during manufacturing using the VULCAN beamline at ORNL’s Spallation Neutron Source, or SNS, a Department of Energy Office of Science user facility. When combined with infrared imaging and computer modelling, this system enables unprecedented insight into material behavior during manufacturing.
In this case, they used low-temperature transformation, or LTT, steel, physically measuring how atoms move in response to stress, whether it’s temperature or load, using the OpeN-Am platform.
Residual stresses are stresses that remain even after a load or the cause of the stress is removed; they can deform a material or, worse, cause it to fail prematurely. Such stresses are a major challenge for fabricating accurate components with desirable properties and performance.
The scientists conceived and, over the course of two years, produced this experiment that can measure strain in the material as it evolves, which determines how stresses will be distributed.
“Manufacturers will be able to tailor residual stress in their components, increasing their strength, making them lighter and in more complex shapes. The technology can be applied to anything you want to manufacture,” Plotkowski said.
“We have successfully shown that there is a way to do that,” he said. “We are demonstrating we understand connections in one case to anticipate other cases.”
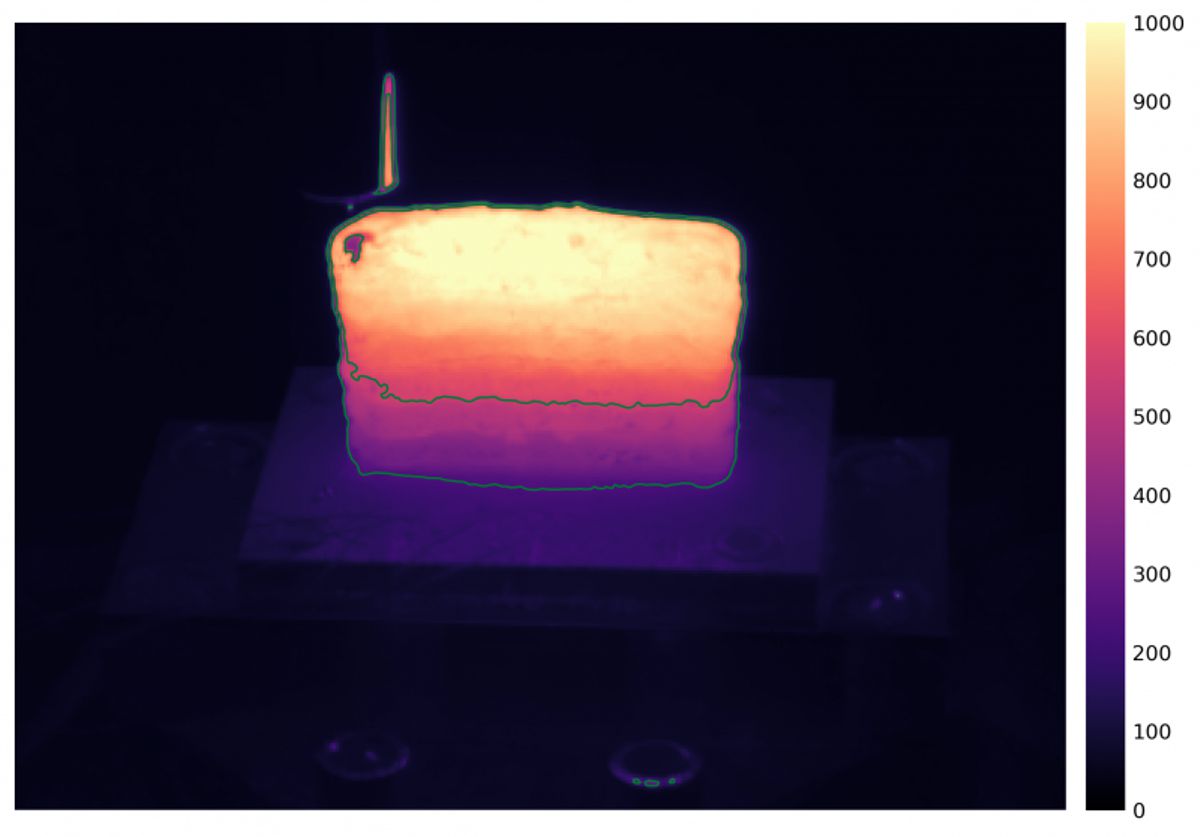
The scientists recently earned a 2023 R&D 100 Award for this technology. R&D World magazine announced the winners in August. Plotkowski and other winners will be recognized at the organization’s award ceremony Nov. 16 in San Diego.
The scientists used a custom wire-arc additive manufacturing platform to perform what’s called operando neutron diffraction of an LTT metal at SNS. Using SNS’s VULCAN beamline, they processed the steel and recorded data at various stages during manufacturing and after cooling to room temperature. They combined diffraction data with infrared imaging to confirm results. The system was designed and built at the Manufacturing Demonstration Facility, or MDF, a DOE Advanced Materials and Manufacturing Technologies Office user consortium, where a replicate system of the platform was also constructed to plan and test experiments before executing at the beamline.
SNS operates a linear particle accelerator that produces beams of neutrons to study and analyse materials at the atomic scale. The research tool they developed allows scientists to peer inside a material as it’s being produced, literally observing the mechanisms at work in real time.
The LTT steel was melted and deposited in layers. As the metal solidified and cooled, its structure transformed in what is called a phase transformation. When that happens, atoms rearrange and take up different space, and the material behaves differently.
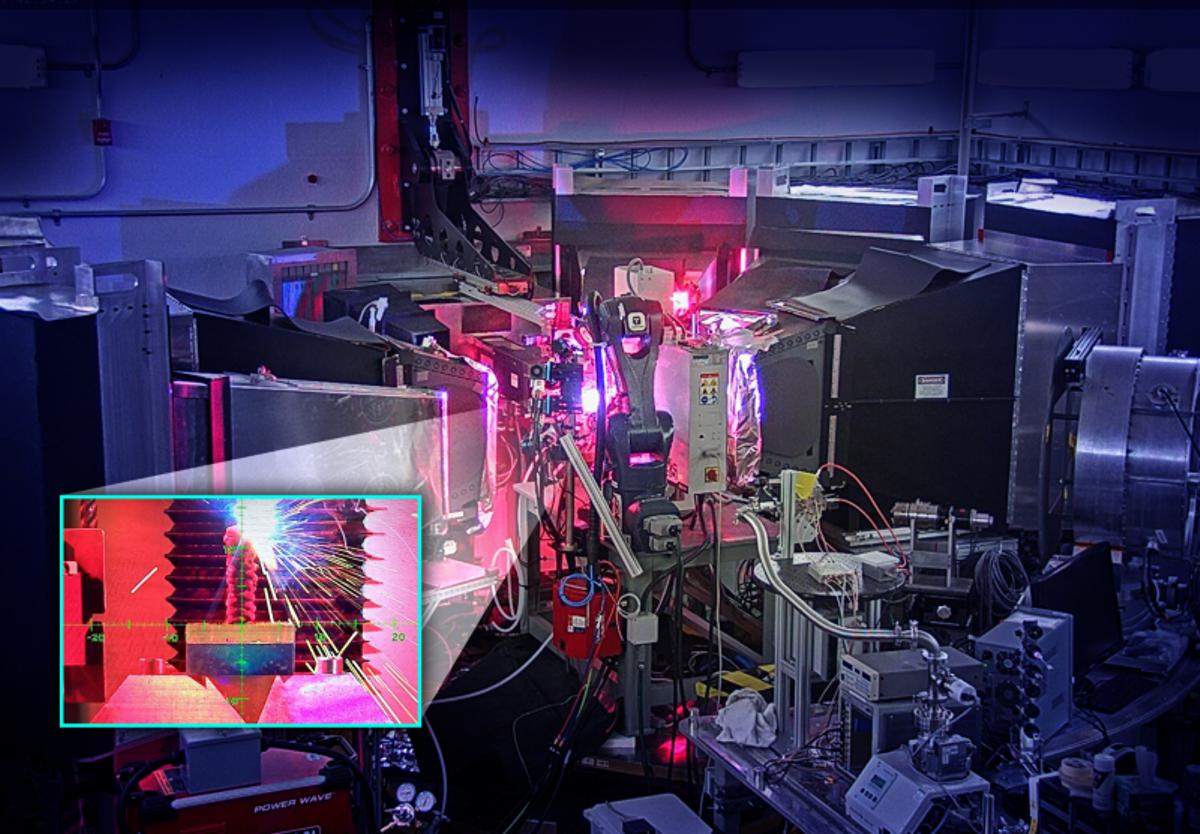
Normally, transformations that happen at high temperatures are hard to understand when looking at a material only after processing. By observing the LTT steel during processing, the scientists’ experiment shows that they can understand and manipulate the phase transformation.
“We want to understand what these stresses are, explain how they got there, and figure out how to control them,” Plotkowski said.
“These results provide a new pathway to design desirable residual stress states and property distributions within additive manufacturing components by using process controls to improve nonuniform spatial and temporal variations of thermal gradients around key phase transformation temperatures,” the authors write.
Plotkowski hopes scientists from around the world come to ORNL to do similar experiments on metals they would like to use in manufacturing.
This research was funded by ORNL’s Laboratory Directed Research and Development program, which supports high-risk research and development in areas of potential high value to national programs.
Co-authors include ORNL’s Chris Fancher, James Haley, Ke An, Rangasayee Kannan, Thomas Feldhausen, Yousub Lee, Dunji Yu and Joshua Vaughan; University of Tennessee-ORNL Governor’s Chair Suresh Babu; and former ORNL researchers Kyle Saleeby, Guru Madireddy and C. Leach.
UT-Battelle manages ORNL for DOE’s Office of Science, the single largest supporter of basic research in the physical sciences in the United States. DOE’s Office of Science is working to address some of the most pressing challenges of our time. For more information, visit energy.gov/science. — Lawrence Bernard with additional reporting by Dawn Levy.