Leveraging Pressure Gradients for a novel Manifold Design Theory
University of Illinois researcher Kyle Smith, along with doctoral students Md Habibur Rahman and Vu Do, master’s student Colby Warden, and recent graduate Irwin Loud IV (MSME 2023), have published their new manifold design theory (patent pending) in Physics of Fluids.
Their paper, “A Compact, Low-Pressure Manifold with Uniform Flow at Low Reynolds Number,” was also selected by the journal’s editors as a featured article.
“I think the really cool thing from a mechanical engineering standpoint is that in this design paradigm that we have introduced, we are leveraging pressure gradients within the manifold to make flow uniform,” said Smith, an associate professor of mechanical science and engineering.
Often categorized according to their purpose (e.g., intake or exhaust), manifolds serve as hollow bodies through which a fluid, such as air or water, passes to transition from one space to another. For example, a car’s intake manifold facilitates the flow of ambient air into the engine’s cylinders.
The group’s theory presents a completely different design strategy than that of longstanding manifold design theories in literature, which prioritize achieving uniform pressure within the manifold. Their theory articulates three design constraints that must be met, the first of which is to strategically taper the cross-section of the manifold’s header, or intake.
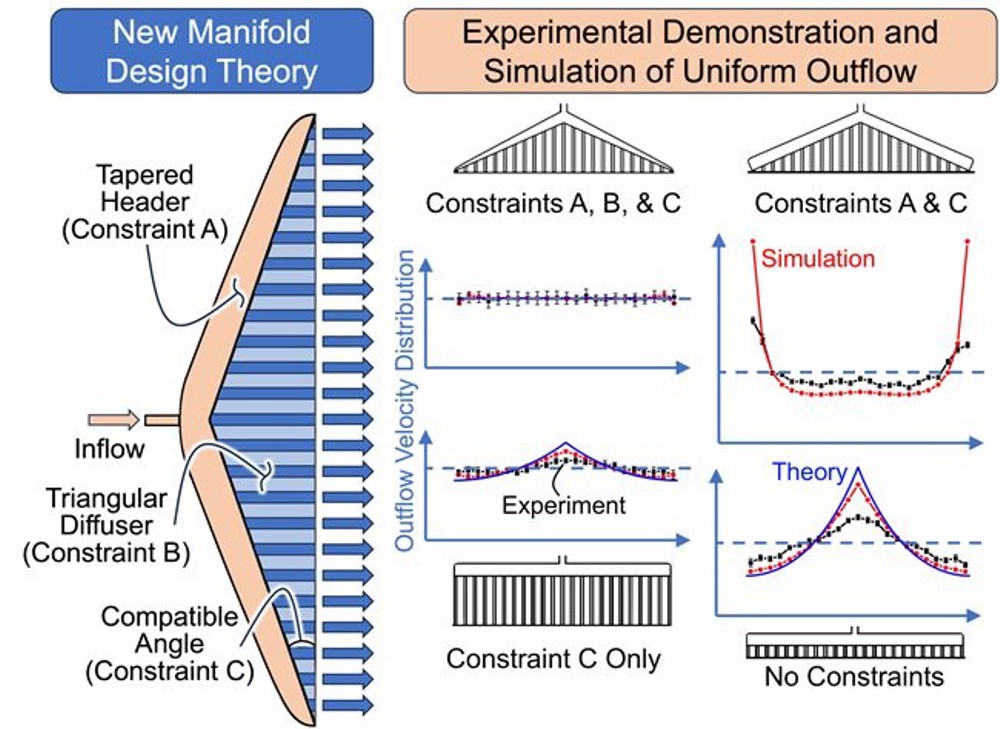
“Depending on what kind of cross section you use, what shape it has in the header channel, the tapering function takes a different form,” Smith said of applying the theory. “These are all physics-based constraints that an engineer can apply to a manifold’s design.”
The second constraint dictates that the diffuser region, or outlet, should have uniformly spaced channels arranged in a triangular configuration. The third constraint accounts for the angle that should be applied to the region.
“Ultimately, we settled on the tapered-header, triangular-diffuser manifold because it was the only one that theoretically produced uniform flow rate to all outlet channels,” Loud said, recalling that they had also explored other configurations such as straight-header, triangular diffuser and straight-header, rectangular-diffuser manifolds.
The paper describes the researchers’ experimental process, for which Loud initially 3D-printed manifold prototypes. The group milled subsequent iterations out of clear acrylic and then collected data from dye-based flow visualization, analysing images of dyed fluid flowing through the manifold into undyed solution.
Rahman said of the experiments that he conducted, “A major challenge was air-bubble entrapment. We ended up overcoming this obstacle by using surfactant. As a new experimentalist, doing these experiments challenged and inspired me.” Their experimental results achieved strong agreement with their theory and computer simulations.