Common equipment operating errors and how to avoid them
Operator behaviour not only affects machine health but also the productivity and profitability of the entire site operations. Here are five of the most common operating errors to watch out for.
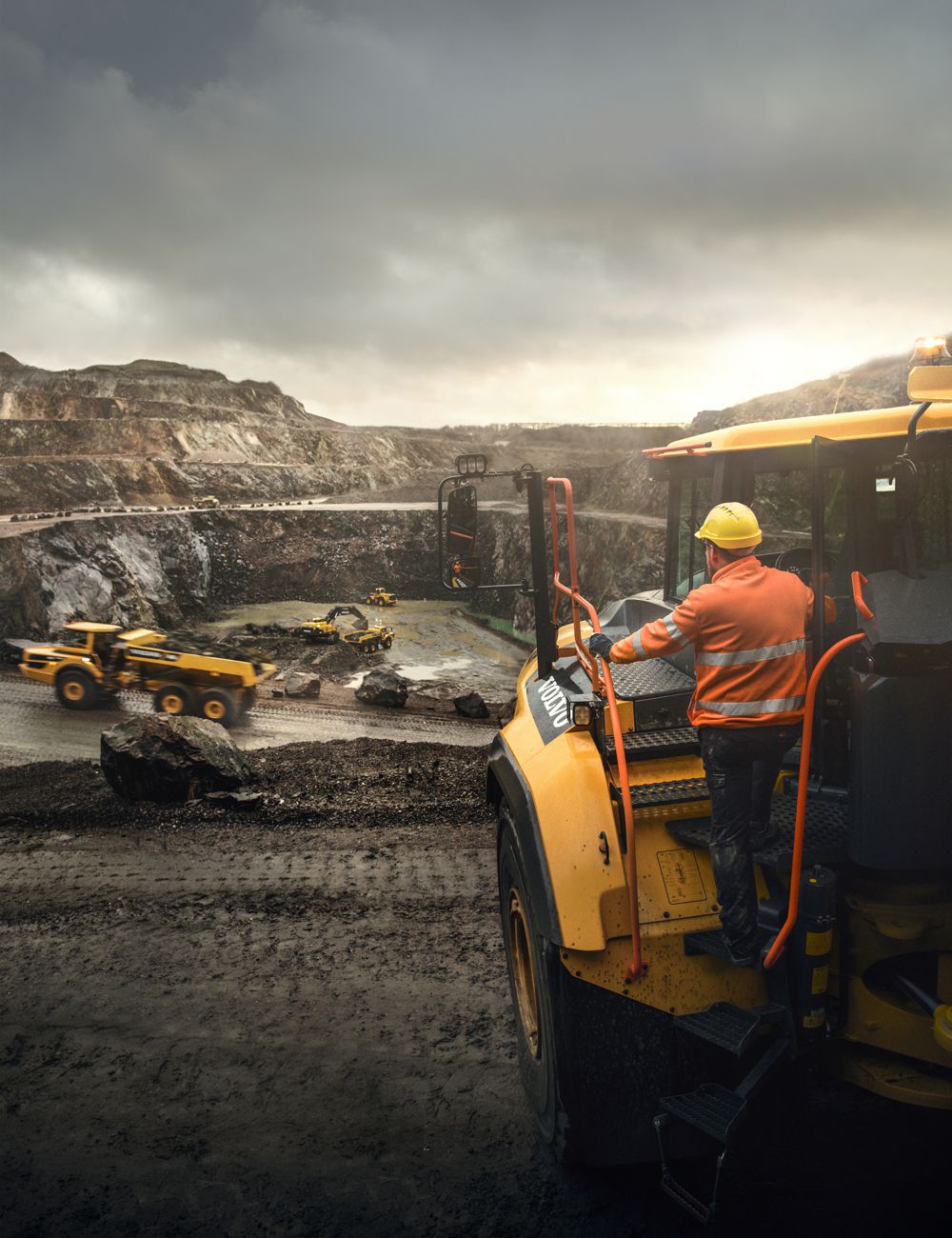
Not leaving a machine to idle for a few minutes before shutting it down
If an operator consistently shuts down their machine without letting the engine idle for a few minutes first, eventually it will lead to damage or even failure of the turbo charger, which can be very expensive operating error to repair.
Volvo CE recommends operators always leave the machine to idle for two to three minutes before completely switching off the engine.
Going from forwards to reverse (or vice versa) at high speed
Another common operating error occurs when regularly shifting the travel direction of a wheel loader at high speed, which can lead to driveline failure.
Considering transmission replacements can cost huge sums, this is one operating error every machine owner should avoid.
Volvo CE recommends operators always bring the machine to a complete standstill before going from forwards to reverse or vice versa.

Using the wrong excavator work mode
Some excavator operators may think that using the highest work mode – Heavy (H) – will help them achieve the highest productivity.
However, they could achieve the same level of productivity in a lower work mode, burning half the fuel.

Applying the brakes too often and not using the retarder
Another of the big operating errors is with articulated hauler operators who have a habit of ‘riding the brakes’. Resting a foot on the brake pedal, however lightly, means the hauler has to work harder to maintain speed and the brakes wear faster.
Using the brakes to maintain a steady speed while travelling downhill, instead of the retarder, has a similar effect.
Unnecessary wear to the brakes leads to unnecessary brake replacement costs.
Overusing the 6×6-wheel drive combination on an articulated hauler
Volvo articulated haulers feature differential locks that allow the operator to choose between 4×6 and 6×6-wheel drive combinations, depending on how much traction they need.
The 6×6 combination delivers excellent control and stability on difficult terrain but if operators use it when they don’t need to, they can waste a lot of fuel and cause unnecessary wear to the tyres.
Take back control
Connecting machines via Volvo CE’s CareTrack telematics system makes it possible to track operating behaviour and errors and implement an operator training programme.
This will result in reduced wear, lower maintenance costs, greater fuel efficiency, increased productivity – and higher profits.
Volvo CE dealers have all the tools at their disposal to help customers take control of their costs for a successful and profitable business.