Virtual planning using BIM proved successful on Gelbe Haide formwork project
The experts at Doka created a virtual model based on building information modelling (BIM) for the construction of a reservoir in Vienna’s 23rd district so that wall formwork and cycle times could be planned precisely using Virtual planning. This reduced the on-site work and resources required by construction company HABAU. Each worker’s formwork productivity doubled, with one casting section completed every three days.
The “Gelbe Haide” project is the first BIM project that HABAU Hoch- und Tiefbaugesellschaft has undertaken with Doka. The construction company was commissioned by the City of Vienna to construct a reservoir, an overflow basin and a feed channel. The reservoir is designed as a flood defence measure to protect residents living along the Liesing, the river that runs right through Vienna. Following its completion at the end of 2020, the reservoir will be able to hold 10 million litres of rainwater and will prevent the pollution of the River Liesing and routes that run along it.
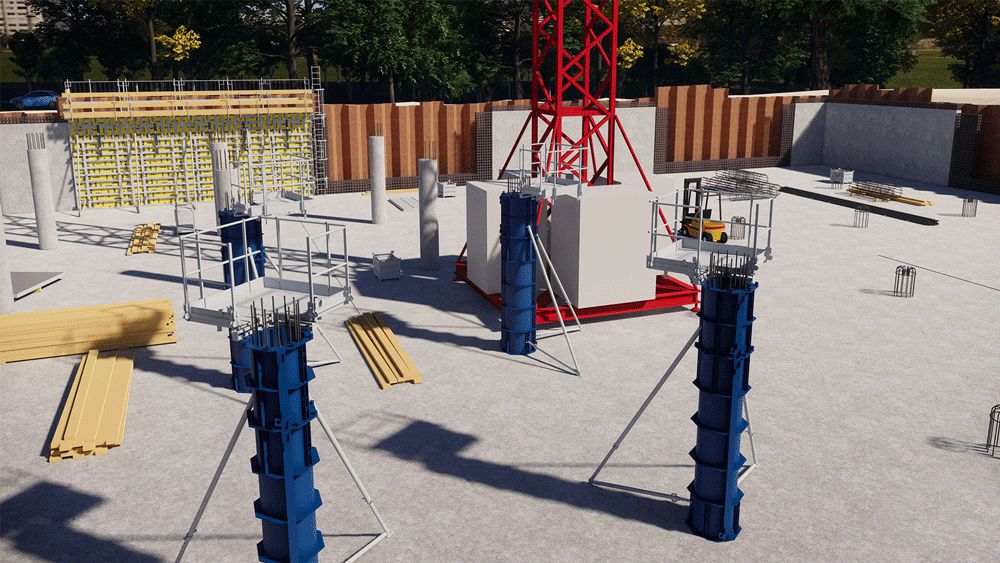
Virtual model ensures rapid execution
HABAU provided the original 3D model in IFC format and the BIM experts at Doka added the formwork plans. Creating a virtual model offered various advantages. The dimensions of the formwork elements were designed to ensure that they would not need to be disassembled on site for use in the next pouring section. BIM Coordinator Bernhard Wieser: “The fact that we were able to calculate the wall cycles in advance in the 3D model meant that flawless planning was guaranteed. All of the parameters, such as the lifting capacity and reach of the crane – 6 tonnes and 55 metres in this case – were taken into account right from the start.” Each of the five repositionable units was 12.5 metres long and, at 5.5 tonnes, they were just the right weight for the crane to move them in a single lift.
Everyone at HABAU and Doka involved in the project had constant access to the 3D model created using the Autodesk Revit software. Without this shared BIM model, the use of different software solutions would have resulted in a loss of time. The “traditional” approach would have involved generating material lists and then entering them into the modelling software. Working on a shared project platform (CDE) made communicating within and coordinating the project significantly easier. It meant that important criteria could be considered during the planning stages, says Wieser. As a result, formwork quantities were optimised to avoid the need for conversion measures, which significantly reduced the time and work required.
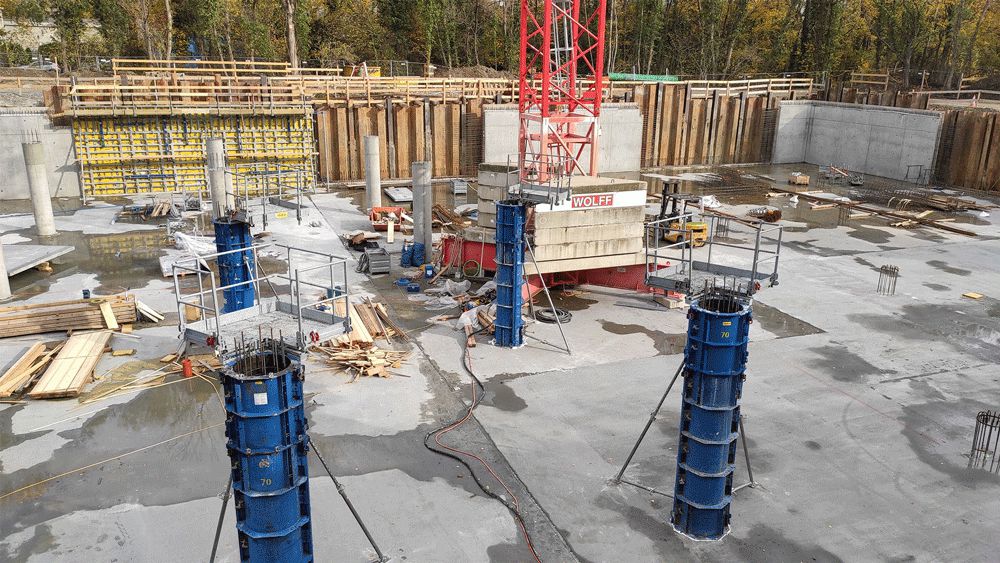
Efficient use of resources – thanks to BIM
Four workers completed a single formwork cycle approximately every three days. Normally, this would take five days and six workers, explains BIM Coordinator Simon Berger, who oversaw the project for Doka. A construction period of roughly two months was required for a total of 13 cycles. That’s how long it took to complete the 230-metre-long, 4.5-metre-tall and 0.4-metre-wide walls.
The advance cycle planning using the Virtual planning BIM method meant that almost no additional material was needed on site. Bernhard Wieser calls it “minimising underutilisation” and describes it like this: “The trick is to minimise the additional material as far as possible so that the formwork is used productively instead of just lying around.”
Construction manager Robert Jungmeister from HABAU was also delighted that everything went as planned: “Having Doka as our project partner for formwork solutions for in-situ concrete ensured that construction went smoothly and allowed us to successfully implement lean management principles. This enabled us to use our resources – both our workforce and our equipment – as efficiently as possible.”
Framax Xlife plus framed formwork was chosen for the wall formwork due to the limited space between the sheet-pile walls and in-situ walls. The concrete poured was the sewage-resistant concrete C30/37 B6 C3A.