Leipzig Airport runway and taxiways resurfaced with Trimble 3D accuracy
As part of a modernization and infrastructure improvement effort at Germany’s Leipzig/Halle Airport (LEJ), Mitteldeutsche Flughafen AG recently contracted out the resurfacing of the northern take-off and landing strip and a number of taxiways.
The northern runway has been in operation since March 2000 and since then about 400,000 planes, including some of the largest cargo and passenger planes in the world, have taken off from or landed on the runway.
In total, the 3.8km long, 60m wide north runway and associated taxiways, approximately 300,000 square meters of concrete surfaces, needed to be replaced. In order to preserve the cement treated base course (CTB), the owner stipulated that the removal of the concrete surface needed to be vibration-free. In addition, the new concrete covering should be installed directly onto the milled surface, so the elevation needed to be kept within 10mm.
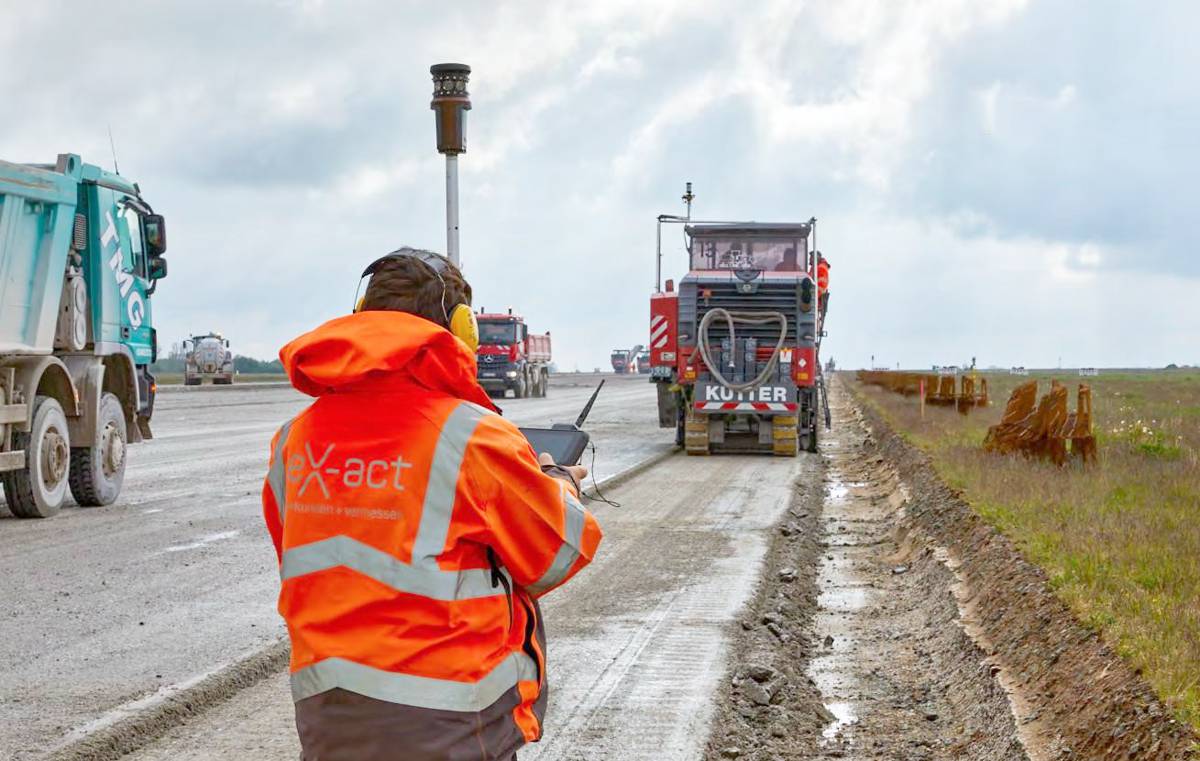
Cold Milling
Kutter GmbH & Co. KG Construction Company, headquartered in Memmingen, Germany, specializes in building construction, civil engineering and road construction, with a particular emphasis on milling. The firm is Germany’s largest milling company and as such was hired for the job. Kutter deployed a Trimble PCS900 3D Paving Control System linked to its cold milling machines to create the new surface.
“Cold milling machines are the ideal solution for vibration-free removal of concrete coverings, and we achieve the precision needed using the 3D control system,” said Bernhard Fischer, Head of Kutter’s Leipzig office.
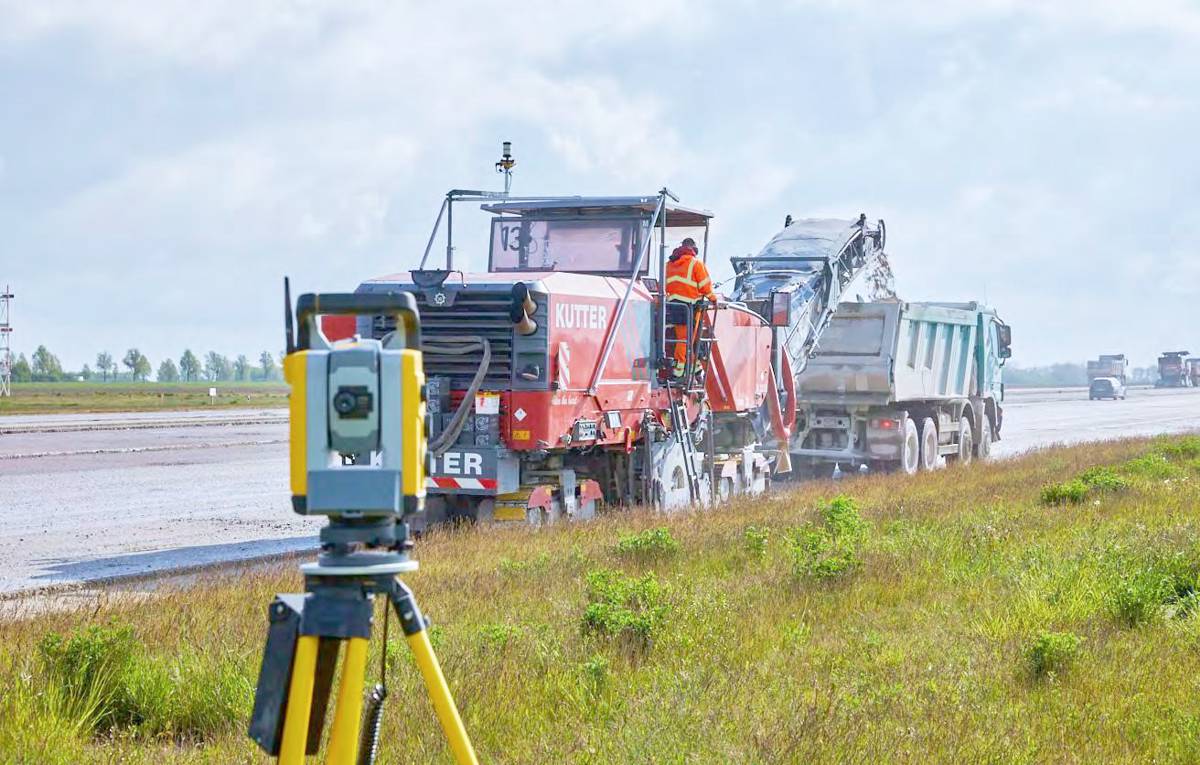
Maximizing Precision
To get work underway, the owner provided a digital model of the surface with defined locations of the upper edge of the new final concrete covering. By deducting the layer thickness, a dataset for the position of the milled surface was produced. This data was then transferred to the cold milling machines. The machines then “know” the target height of the milled surface for every point.
In this instance, the 40cm thick concrete overlay was reinforced with several layers of dowels and anchors. The milling depth was geared to the position of the dowels and anchors.
Kutter accomplished the concrete milling in several passes. “To come to a completely concrete-free planum, we removed 42cm across the whole surface,” recalls Matthias Dreer, site coordinator for the project, who coordinated deployment of the 15 large milling machines for Kutter working over several weeks in a two-shift operation.
The final milling pass was critical for the quality, because the milling machines needed to leave behind a suitably textured surface at the contractually agreed elevation. This pass milled the bottom 4-6 cm of concrete and around 2 cm of the underlying CTB using a standard milling drum. Thanks to 3D-enabled milling, the CTB on the 80,000 square meters of taxiways and 228,000 square meters of runway presented a perfectly flat surface.
On the site, crews relied on the Trimble MT900 Machine Target with patented active tracking technology on the milling machines to guarantee a secure connection with a series of Trimble SPS930 Universal Total Stations placed strategically along the runway.
“Using the total stations, we were able to keep the milling process going smoothly, even if the site was very busy with traffic, numerous machines and trucks,” added Dreer.
A further advantage of this setup proved to be the stable communications between the total stations and the prism. With the Trimble system, each active prism device has an individual address. The total station is programmed to this precise address, which enables rapid re-location of the prism following a break in signal.
“This feature makes the ‘hot swap’ between total stations very easy. It’s an ideal setup for construction sites with several prism devices and other reflective objects,” said Norbert Mattivi, Trimble applications specialist. At Leipzig/Halle Airport, this feature proved particularly useful when milling the long runway.
Accordingly, the milling machine can be permanently controlled with millimetre accuracy. For this, the Trimble prism uses LED lights that transmit on a particular frequency. A CCD camera in the total station recognizes these actively-transmitted light waves via a filter.
“This signal is clearly defined and recognized even under adverse conditions. Dust, rain, snow or fog do not impair communications. And it worked even when the sunlight was directly striking the prism,” explained Mattivi, outlining one of the key advantages.
Dreer confirmed: “Using active tracking, we were able to achieve excellent results at the airport, even under extreme wind conditions where a lot of dust was whipped up. Even under these boundary conditions, the system operated stably.”
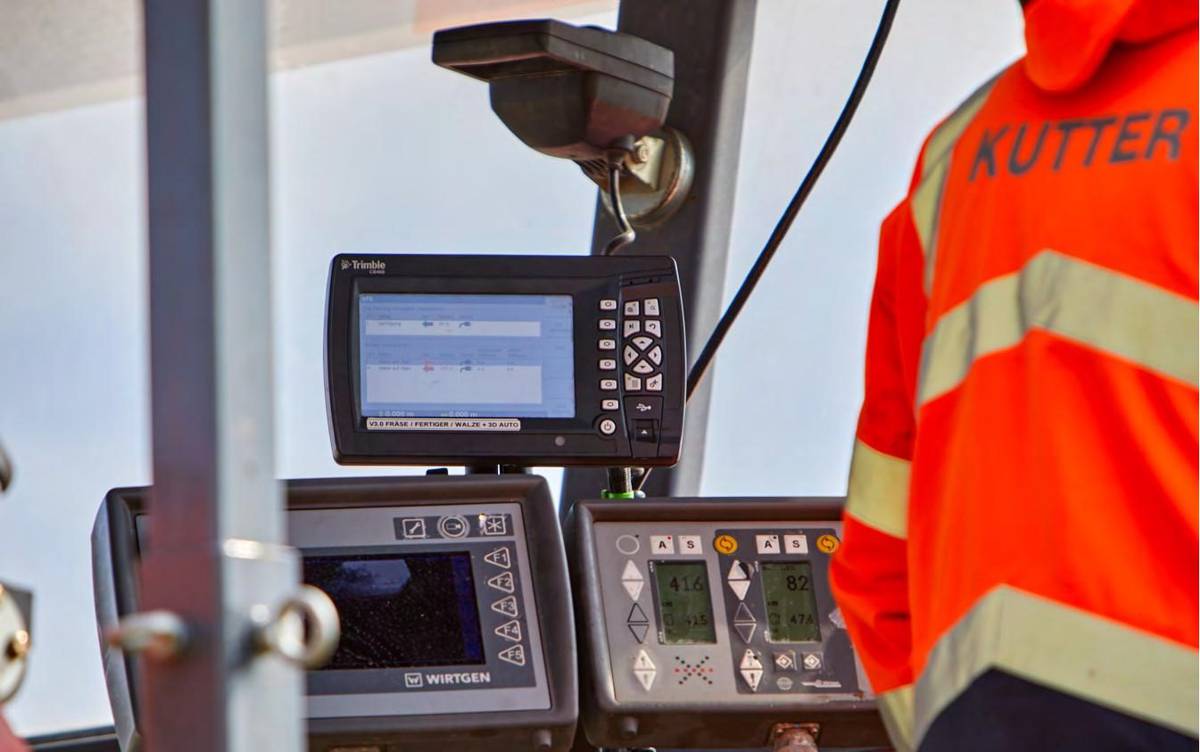
Precision Results
During the milling, a ground-based total station measured the spatial position of the prism on the cold milling machine and transmitted that data to the milling machine’s on-board computer. The on-board computer then compared the measured height with the target values.
The Trimble-enabled solution is engineered for fast communication, meaning that the machine controllers reacted very quickly in the event of deviations. As a result, the milling machines are able to travel at speeds of up to 25 m/min—with the system still delivering very high accuracy. This boosts efficiency when milling large surface areas.
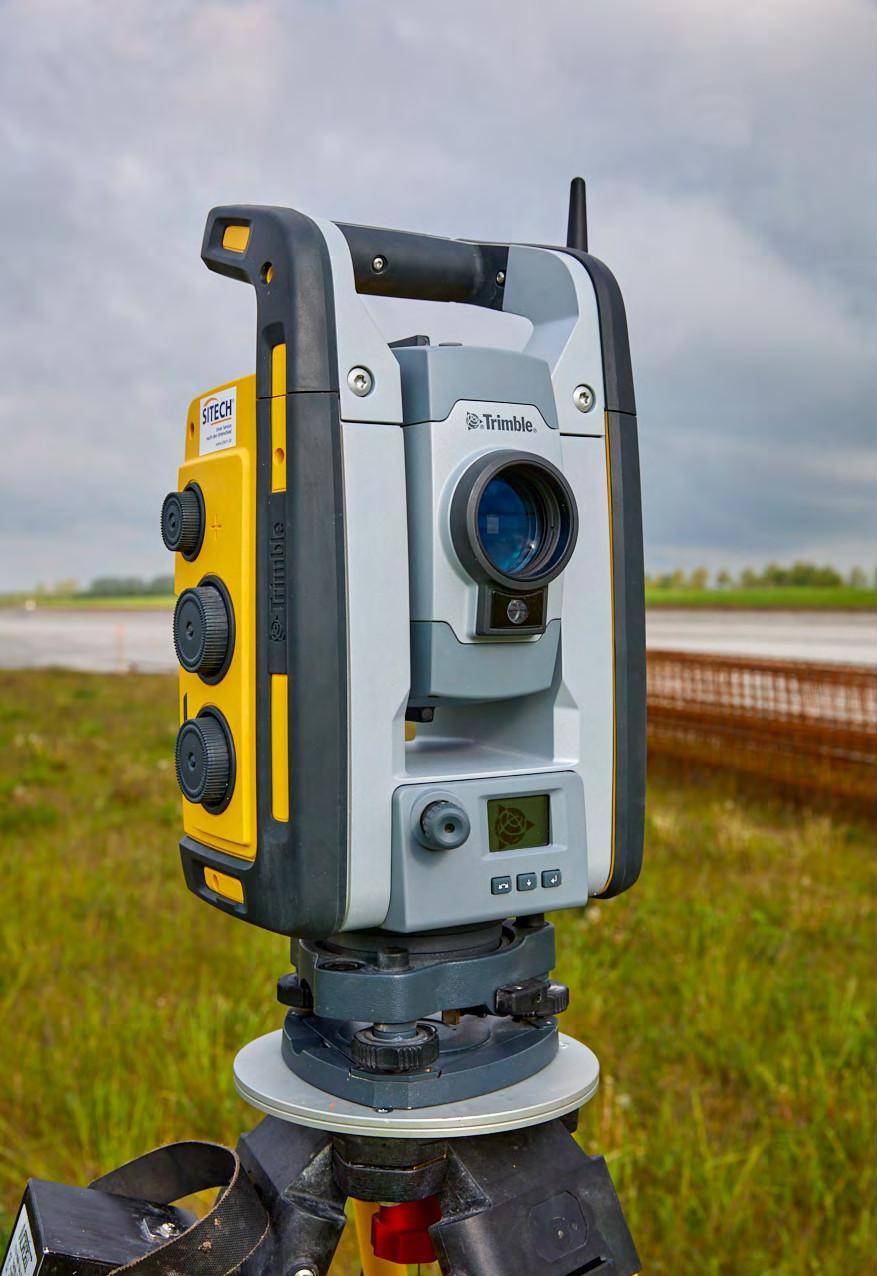
“Using the Trimble system, we are able to remove the runway covering so accurately that the concrete paver can subsequently install the new surface precisely in position on the milled surface. There is no longer any need for leveling layers. That saves our customers a lot of construction materials, and naturally costs, too,” explained Dreer. “With our large milling machines and the 2.20m milling width, we were able to realize over 7,000 m2 per machine per shift, on average.”
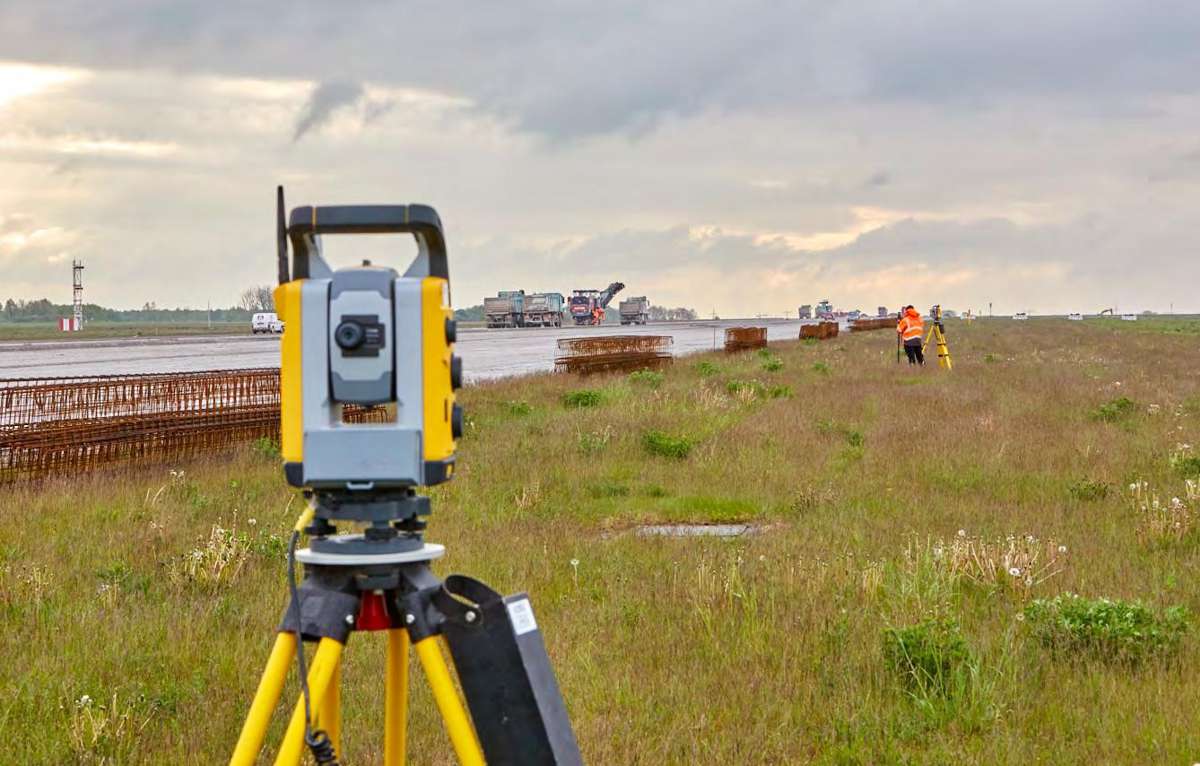
Reliable Partners
When it came to surveying technology, Kutter relied on a collaboration with proven system partners for this project. For the Leipzig/Halle Airport project, the survey team from ex-act GmbH from Zwickau worked with Kutter, in collaboration with local implementation partner SITECH, to handle total station calibration, installation of the components on site and elevation monitoring behind the milling machines.
SITECH consults with contractors and leases the right equipment for each project. With the big advantage being that Trimble uses the same proven components for milling as for excavators, motor graders, dozers and other heavy equipment.
The team completed the milling project in seven weeks. The quality requirements were not just met, but exceeded. Thanks to thorough preparation, the on-site management overseeing milling operations, and the high-performance of the technology, Kutter was ultimately able to hand over a 300,000 m2 surface at an elevation that never deviated by more than 3 mm—well below the specifications put forth by the client.
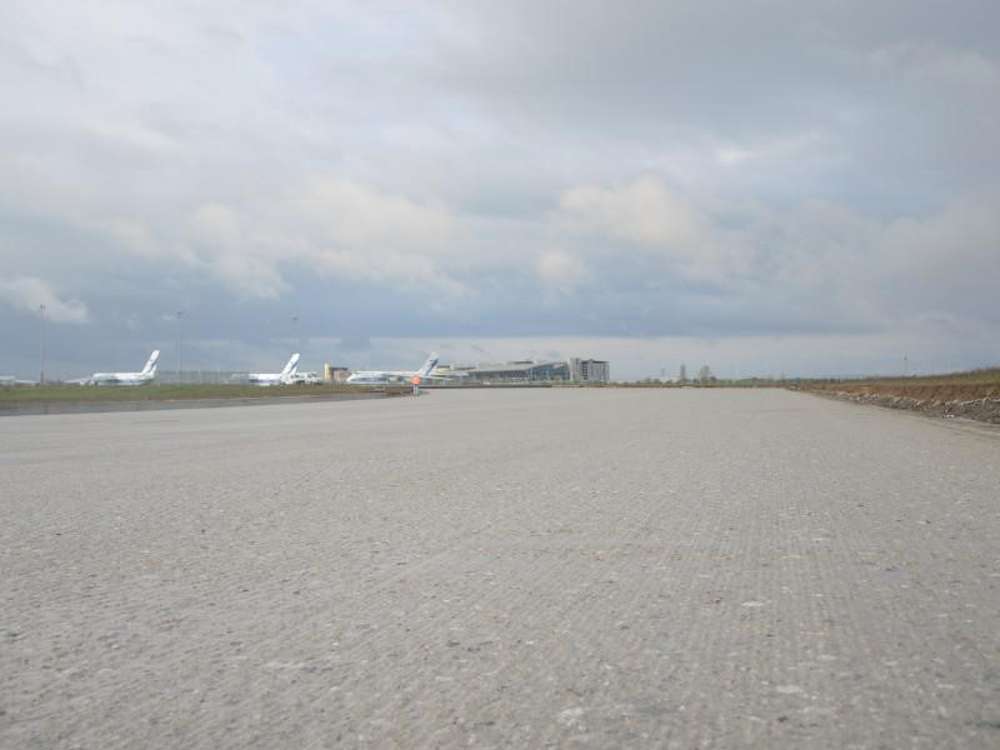