Revolutionary Powder Engineering tech adds AI to the mix
Imagine a world without powders. It may sound exaggerated, but our daily lives are intricately connected to powders in various ways from foods, pharmaceuticals, cosmetics to batteries, ceramics, etc. In all these industries, powder mixing is an important unit operation where different types of powders are mixed to achieve uniformity.
However, it can be difficult to predict what conditions are optimal to achieve the desired uniformity as the process often relies on trial and error as well as engineers’ expertise.
Numerical simulations using the discrete element method (DEM) have been used widely as an approach that can accurately predict powder mixing. This is achieved by calculating the motion of all particles in a very short time range (1/1,000,000 of a second), calculating the motion of the entire powder using the calculated values, and then repeating the process over and over again to calculate the motion of each particle a short time ahead. Therefore, the substantial amount of time it takes to predict powder mixing significantly hampers the ability to have large-scale and long-duration powder mixing processes.
A research team led by Associate Professor Hideya Nakamura, Associate Professor Shuji Ohsaki, Professor Satoru Watano, and Ph.D. student Naoki Kishida from the Graduate School of Engineering at Osaka Metropolitan University has developed a new simulation method using AI. Additionally, the team has succeeded in enhancing computational speed by about 350 times.
This new method is characterized by using a recurrent neural network (RNN) that enables a long-time-scale powder mixing simulation with low computational costs while maintaining the same level of accuracy as conventional methods.
“We have successfully harnessed our knowledge in powder technology, which we have honed over many years, and combined it with machine learning to rapidly predict the unique behaviour of complex powders,” explained Professor Nakamura. “We would like to build upon this achievement to contribute to the future of industries seeking to enhance product quality and streamline production.”
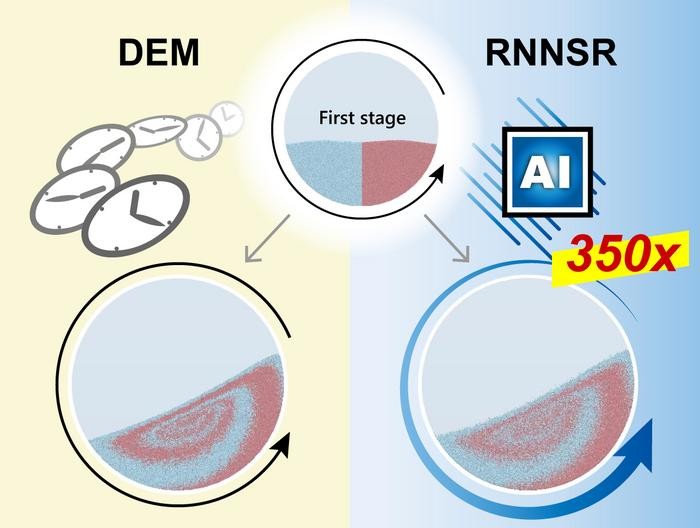
Their findings were published in Chemical Engineering Journal.