New treatment method improves friction and wear of steel and titanium
Scientists refined the method of diffusion saturation of steel and combined it with polishing in electrolyte plasma. Under the influence of current in solutions, that contained nitrogen, boron and carbon, on the surface of samples there was a formation of modified structure.
It consisted of oxidic coating and diffusion layer under it, that contained 0,8% nitrogen, 0,87% boron and 0,87% carbon. This layer increased hardness of test samples almost twice. Besides this, due to modified structure the mass loss during friction decreased 25 times. The further polishing of material smoothened roughness on the surface of samples and thus, additionally reduced friction coefficient also 1,34 times. Results of the research are published in Surface Engineering and Applied Electrochemistry.
Steel, cast iron and titanium alloys are widely used in various branches of industry. However, these materials are fast-wearing and become useless, that is why scientists elaborate various variants of their modification, that enable to increase their hardness and wear resistance. One of such methods of improvement is plasma electrolytic diffusion saturation with atoms of light elements, for example, nitrogen. As a result, on the surface of treated product a modified layer is formed, that consists of compounds of iron and titan with modifying components and provides higher hardness and increased hardiness to corrosion and wearing. However, under certain conditions such treatment of metal leads to roughness and formation of interstices on its surface, that tends to development of corrosion.
Scientists from Kostroma State University (Kostroma) improved the method of diffusion saturation, and obtained materials treated with the help of plasma electrolytic polishing. On the first stage authors treated steel samples with plasma electrolytic diffusion saturation by boron, nitrogen and carbon. They used solutions of ammonium chloride (NH4Cl), boric acid (H3BO3) and glycerin (C3H5(OH)3) correspondingly as a source of these elements. Samples were placed in heated solution and exposed to current. In steam of water electrolyte, a surface layer of material got oxidized., thus forming oxidic layer. There was a formation of diffusion layer under it, that consisted of compounds of iron with nitrogen, boron and carbon.
Duration of saturation was determined by structure of oxidic layer. Thus, with the help of microscopy authors found put craters in oxidic coating, however, the longer samples were saturated the smaller craters were, and the less rough was the surface. Authors think that with increasing of time of treatment discharges destroyed the surface loose oxidic layer heavier, without touching more solid oxidic layers.
Then they studied how as a result of diffusion nitrogen, boron and carbon were distributed in diffusion layer. Concentration of all elements raised with increasement of durability of the saturation. By this after 30 minutes of treatment the concentration of nitrogen in the surface layer reached 0,8%, and boron and carbon — 0,87%. As a result of diffusion saturation hardness of samples increased almost twice. By this with increasement of time of treatment thickness of zone of hardening increased.
Besides this, authors found out that during dry friction on steel disc the obtained material rubbed away and wore out less. Thus, mass loss decreased 25 times after diffusion saturation. It was connected with formation of oxidic layer, that worked during friction as a lubrification., and solid diffusion layer under it.
On the second stage of their work scientists used plasma electrolytic polishing in order to improve features of material additionally. To achieve this, they immersed samples into the warmed solution of electrolyte under the action of permanent current (up to 325 V). As a result, after two minutes of polishing samples became as smooth as before saturation. By this mass loss of material were insignificant. In the process of polishing only protruding parts of surface layer were removed, and not the whole layer. Besides this as a result of polishing in electrolyte the surface additionally got oxidized. Thanks to these factors friction coefficient of samples reduced 1.88 times as compared with totally untreated steel and 1.34 times as compared with material, subjected only to saturation.
“For the first time we (in scientific publications we haven’t met it yet) conducted combining of such different as far as use and nature is concerned processes as thermochemical treatment and polishing in conditions of plasma electrolyte. That enabled to solve a number of vital tasks in the sphere of plasma electrolyte technologies. In future we are planning to replicate principles of the method on other materials and elaborate technological processes of industrial scale,” – tells Sergei Kusmanov, professor, director of Department of Mathematical and Natural sciences of Kostroma State University.
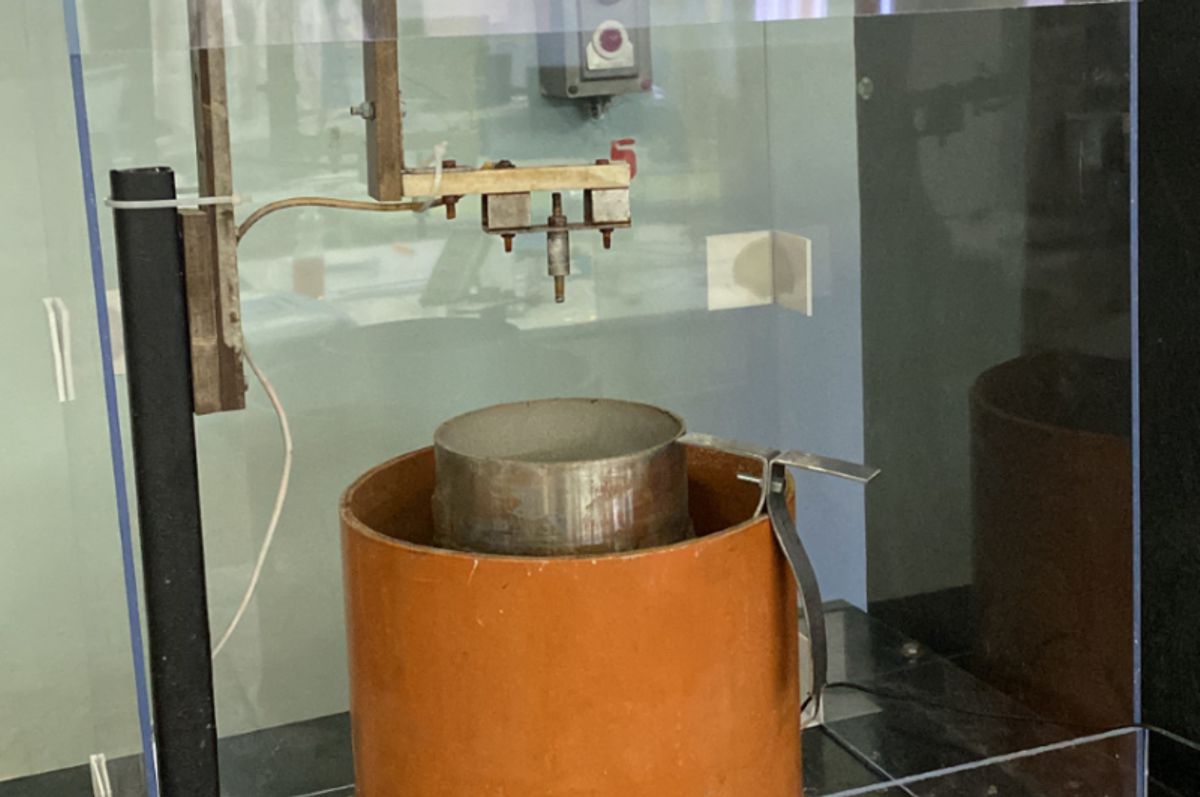