Mastering the Marshall Mix Design Method for Durable Pavements
The Marshall Mix Design method, a cornerstone in the field of pavement design, has been a reliable process for producing durable and high-quality asphalt pavements for decades.
Developed by Bruce Marshall in the late 1930s, this method has stood the test of time due to its simple design methodology that was developed to use the aggregates, sand and bitumen that was easily available near the job location, to avoid resourcing, logistics and additional cost.
The Marshall Mix Design method become standard practice in the industry until recently, and was used in most countries around the world due to its effectiveness and straightforward approach. Despite new and improved mix design methods that have evolved out of the the Marshall Mix Design Method, it is still in wide use globally, but it was never used in the UK.
Origins and Evolution
Bruce Marshall, working with the Mississippi State Highway Department, developed the Marshall Mix Design method to create a systematic approach for selecting the optimum asphalt content in a mix.
Over the years, this method has been refined and adopted worldwide, reflecting its robustness, practicality and reliability in diverse conditions, and with diverse material sources.
Since the advent of computers, the production of modified bitumen, and the rise in heavy traffic volumes, regularity authorities have largely moved away from the Marshall Mix Design in favour of new and improved mix design methods emanating from the leading bitumen suppliers, universities and others, in an attempt to upgrade pavement design to improve longer lasting and increased durability necessary to increase the life of the asphalt pavement.
In the USA, Europe, Asia and elsewhere the most popular modern mix designs in use now are based on the Superpave Asphalt Mix Design using modified asphalt and raw materials to provide the parameters required to allow for the optimum performance of the asphalt pavement. The Superpave (Superior Performing Asphalt Pavements) mix design method was developed in the United States as part of the Strategic Highway Research Program (SHRP), which has been widely adopted internationally, including in the UK, due to its comprehensive approach to designing asphalt mixtures that perform well under varying traffic and environmental conditions.
The Marshall Mix Design Procedure
The Marshall Mix Design method involves several critical steps to ensure the asphalt mix achieves the desired performance characteristics. Here’s a closer look at the procedure:
Sample Preparation
The initial phase of the Marshall Mix Design method involves the meticulous preparation of samples, ensuring that both aggregates and asphalt binders meet specific standards.
- Selection of Aggregates: The quality of aggregates significantly impacts the performance of the asphalt mix. Aggregates are selected based on their size, shape, and gradation. Proper grading ensures that the aggregates interlock well and provide structural stability. Aggregates are combined in specified proportions to achieve the desired gradation.
- Asphalt Binder Selection: The choice of asphalt binder is crucial as it influences the mix’s performance under varying temperatures and loads. The binder is selected based on performance grade (PG) specifications that consider the climatic conditions of the region where the pavement will be constructed.
Compaction
Once the samples are prepared with the selected aggregates and binder, the next step is compaction. Proper compaction is essential to simulate the conditions the pavement will experience in the field.
- Marshall Hammer: The samples are placed in moulds and compacted using a Marshall hammer. This device applies a specific number of blows (usually 75) on each side of the sample to achieve the desired density and simulate the compaction process during pavement construction. The compaction process ensures that the aggregates and binder are adequately packed, reducing air voids and increasing the mix’s stability.
Testing and Analysis
After compaction, the samples undergo a series of tests to evaluate their properties. These tests are crucial for determining the mix’s performance characteristics and ensuring it meets the required standards.
- Stability and Flow Tests: The stability test measures the load the sample can withstand before failure, indicating the mix’s ability to support traffic loads. The flow test measures the deformation of the sample under load, providing insights into the mix’s flexibility. Both tests are conducted using a Marshall stability testing machine, where the sample is loaded at a constant rate until failure.
- Density and Void Analysis: The density of the compacted samples is measured to calculate the air voids, voids in mineral aggregate (VMA), and voids filled with asphalt (VFA). These parameters are critical for assessing the mix’s durability and workability.
- Air Voids: The air void content is essential for determining the mix’s susceptibility to deformation and moisture damage. Optimal air void content ensures that the mix has enough voids to accommodate thermal expansion and contraction without cracking.
- Voids in Mineral Aggregate (VMA): VMA represents the space between the aggregates in the compacted mix. Higher VMA values indicate more room for the binder, improving the mix’s durability and flexibility.
- Voids Filled with Asphalt (VFA): VFA is the percentage of VMA filled with asphalt binder. This parameter helps ensure that the binder adequately coats the aggregates, providing the necessary adhesion and cohesion.
Determining the Optimum Asphalt Content
The core of the Marshall Mix Design method lies in determining the optimum asphalt content. This is achieved by analysing the results of the stability, flow, density, and voids tests to find the asphalt content that provides the best balance of properties.
The goal is to achieve a mix that offers:
- High Stability: To withstand traffic loads without deformation.
- Sufficient Flexibility: To resist cracking and brittleness.
- Durability: To endure varying weather conditions and aging.
The process of finding the optimum asphalt content involves plotting the test results against varying asphalt content levels. The optimum content is typically chosen at the point where the mix achieves maximum stability while maintaining acceptable levels of air voids, VMA, and VFA.
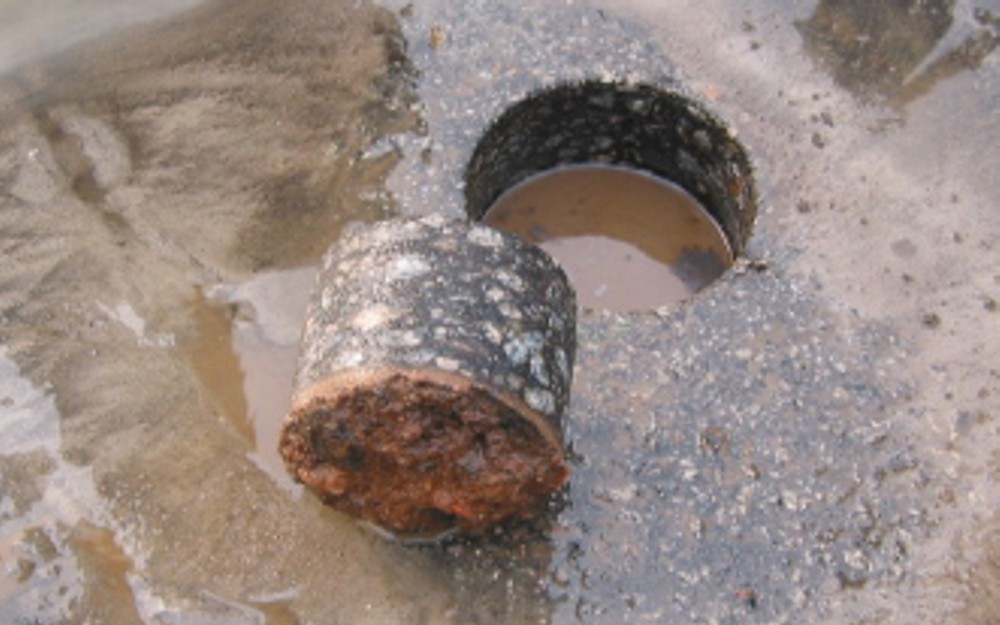
Detailed Step-by-Step Analysis
1. Aggregate Gradation
Aggregate gradation plays a significant role in the mix design process. Properly graded aggregates ensure a dense, stable mix. The gradation process involves sieving aggregates through a series of sieves with different sizes and plotting the cumulative percentage passing each sieve on a semi-logarithmic graph. The target is to achieve a gradation curve that fits within specified limits, ensuring an optimal balance of coarse and fine aggregates.
2. Binder Content Selection
Selecting the appropriate binder content involves creating trial mixes with different asphalt content levels. Typically, mixes are prepared with binder contents ranging from 4% to 6% by weight of the total mix. Each mix is subjected to compaction and testing to determine its stability, flow, density, and void characteristics.
3. Compaction Energy
The amount of compaction energy applied during the process affects the mix’s density and void content. The standard number of blows per side is 75 for heavy traffic conditions and 50 for light traffic conditions. The compaction process is critical as it simulates the field compaction and ensures the mix can achieve the desired density and performance.
4. Stability and Flow Measurement
The stability and flow tests provide vital information about the mix’s performance under load. The stability value indicates the mix’s strength, while the flow value indicates its deformation characteristics. Both values are plotted against the asphalt content to find the optimal balance.
5. Volumetric Analysis
Volumetric properties, including air voids, VMA, and VFA, are calculated based on the compacted density and theoretical maximum density of the mix. These properties are essential for ensuring the mix’s durability and resistance to moisture damage.
6. Selecting the Optimum Asphalt Content
The final step involves selecting the optimum asphalt content based on the combined analysis of stability, flow, density, and volumetric properties. The chosen asphalt content should provide maximum stability while maintaining acceptable air voids, VMA, and VFA levels. This ensures the mix’s durability, flexibility, and resistance to deformation.
Practical Applications
In practical terms, the Marshall Mix Design method is utilized extensively in the construction of roads, highways, and airport runways. Its focus on achieving the optimal mix ensures that pavements can handle heavy traffic loads and adverse weather conditions, leading to longer-lasting surfaces and reduced maintenance costs.
Modern Enhancements
While the Marshall Mix Design method remains a cornerstone in pavement engineering, advancements in technology have led to the development of enhanced testing and analysis techniques. Modern equipment and computer simulations now complement traditional methods, providing even greater precision and efficiency in mix design.
Conclusion
The Marshall Mix Design method continues to be a fundamental practice in the construction industry, especially in developing nations, ensuring that asphalt pavements meet the rigorous demands of today’s infrastructure.
By balancing stability, flexibility, and durability, mix design methods helps create pavements that are not only robust and reliable but also economically viable.
For construction professionals, policy makers, and industry investors, understanding and utilizing the Mix Design methods is crucial for building infrastructure that stands the test of time. The method’s blend of simplicity, proven reliability, and adaptability makes it an indispensable tool in the quest for durable and high-performing pavements.