Small and strong magnets could help harness Fusion devices
Researchers at the U.S. Department of Energy’s (DOE) Princeton Plasma Physics Laboratory (PPPL) have found a way to build powerful magnets smaller than before, aiding the design and construction of machines that could help the world harness the power of the sun to create electricity without producing greenhouse gases that contribute to climate change.
The scientists found a way to build high-temperature superconducting magnets that are made of material that conducts electricity with little or no resistance at temperatures warmer than before. Such powerful magnets would more easily fit within the tight space inside spherical tokamaks, which are shaped more like a cored apple than the doughnut-like shape of conventional tokamaks, and are being explored as a possible design for future fusion power plants.
Since the magnets could be positioned apart from other machinery in the spherical tokamak’s central cavity to corral the hot plasma that fuels fusion reactions, researchers could repair them without having to take anything else apart. “To do this, you need a magnet with a stronger magnetic field and a smaller size than current magnets,” said Yuhu Zhai, a principal engineer at PPPL and lead author of a paper reporting the results in IEEE Transactions on Applied Superconductivity. “The only way you do that is with superconducting wires, and that’s what we’ve done.”
Fusion, the power that drives the sun and stars, combines light elements in the form of plasma — the hot, charged state of matter composed of free electrons and atomic nuclei — that generates massive amounts of energy. Scientists are seeking to replicate fusion on Earth for a virtually inexhaustible supply of safe and clean power to generate electricity.
High-temperature superconducting magnets have several advantages over copper magnets. They can be turned on for longer periods than copper magnets can because they don’t heat up as quickly, making them better suited for use in future fusion power plants that will have to run for months at a time. Superconducting wires are also powerful, able to transmit the same amount of electrical current as a copper wire many times wider while producing a stronger magnetic field.
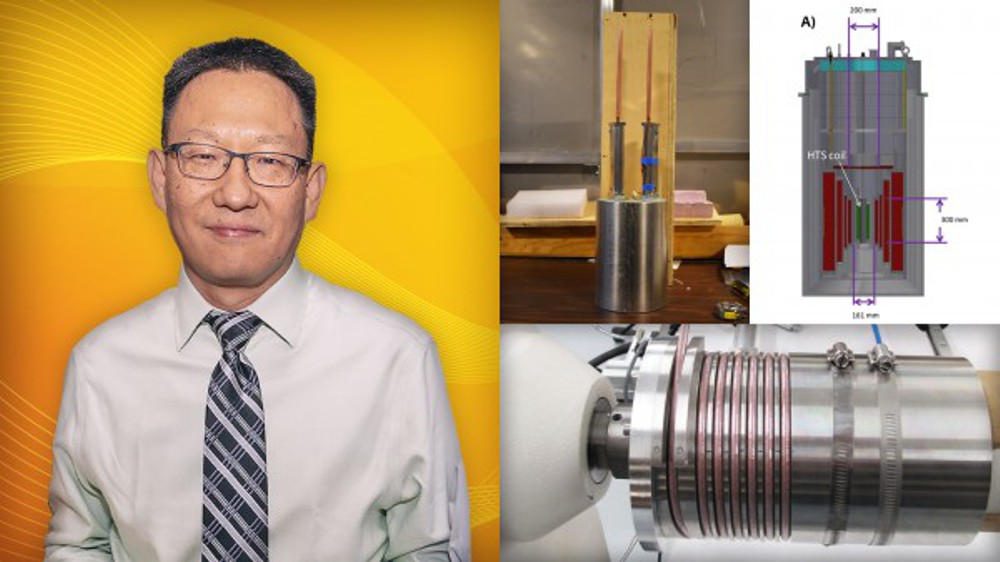
The magnets could also help scientists continue to shrink the size of tokamaks, improving performance and reducing construction cost. “Tokamaks are sensitive to the conditions in their central regions, including the size of the central magnet, or solenoid, the shielding, and the vacuum vessel,” said Jon Menard, PPPL’s deputy director for research. “A lot depends on the center. So if you can shrink things in the middle, you can shrink the whole machine and reduce cost while, in theory, improving performance.”
These new magnets take advantage of a technique refined by Zhai and researchers at Advanced Conductor Technologies, the University of Colorado, Boulder, and the National High Magnetic Field Laboratory, in Tallahassee, Florida. The technique means that the wires do not need conventional epoxy and glass fibre insulation to ensure the flow of electricity. While simplifying construction, the technique also lowers costs. “The costs to wind the coils are much lower because we don’t have to go through the expensive and error-prone epoxy vacuum-impregnation process,” Zhai said. “Instead, you’re directly winding the conductor into the coil form.”
Moreover, “high-temperature superconducting magnets can help spherical tokamak design because the higher current density and smaller windings provide more space for support structure that helps the device withstand the high magnetic fields, enhancing operating conditions,” said Thomas Brown, a PPPL engineer who contributed to the research. “Also, the smaller, more powerful magnets give the machine designer more options to design a spherical tokamak with geometry that could enhance overall tokamak performance. We’re not quite there yet but we’re closer, and maybe close enough.”
This research was supported by the U.S. Department of Energy (Small Business Innovation Research and Laboratory Directed Research and Development).